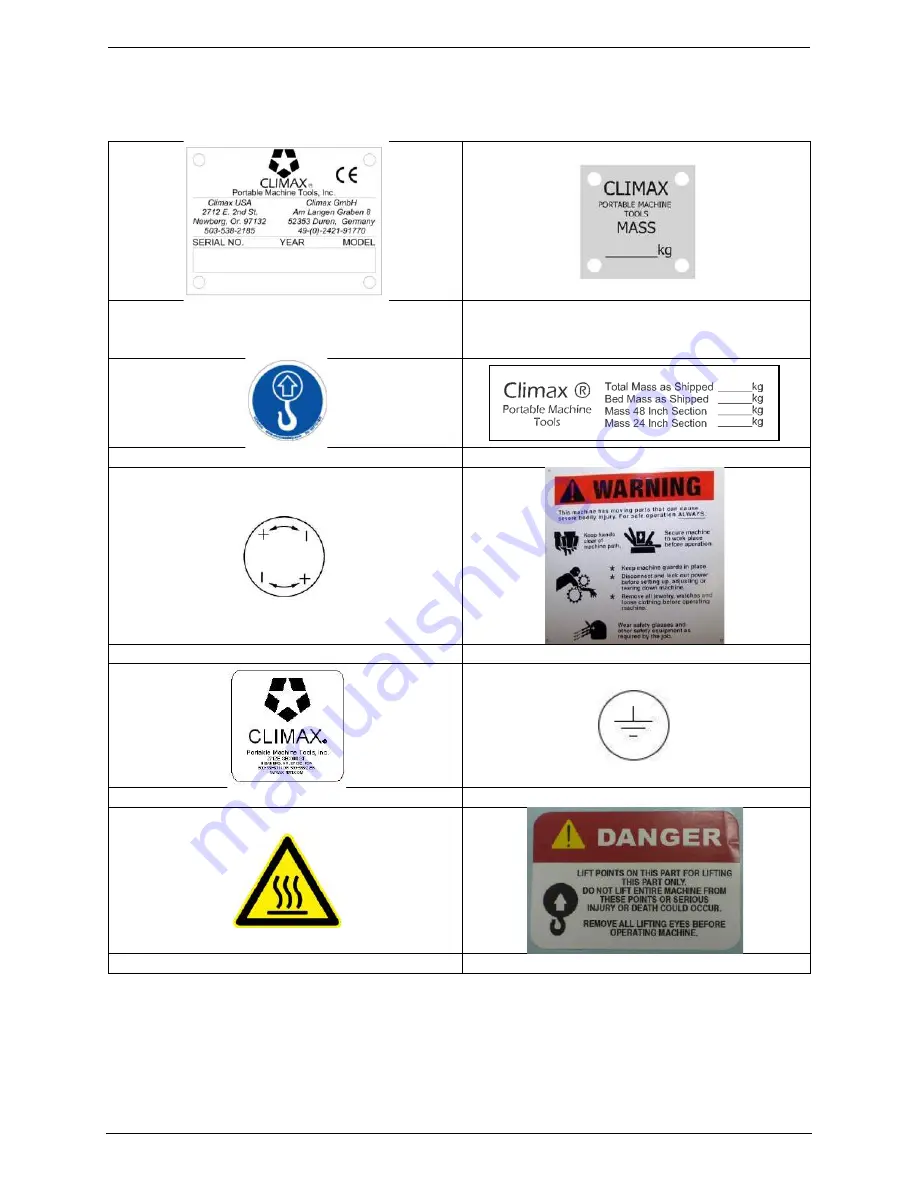
Page 8
LM5200 Operating Manual
Labels
Part Number 29154 – Machine Nameplate
Part Number 29152 – Mass Tag displays the
weight of a group of components or the
assembly in Kilos
Part Number 59039 – Designated Lift Point
Part Number 65487 – Mass Tag
Part Number 35772 – Ball Valve Handle
Part Number 27307 – Warning Label
Part Number 61839 – Climax Logo
Part Number 37572 – PE Ground
Part Number 46902 – Warning Hot Surface
Part Number 62888 – Lift Point Only
Summary of Contents for LM5200
Page 2: ......
Page 7: ...P N 66188 Rev 5 Page 5 This page intentionally left blank...
Page 15: ...P N 66188 Rev 5 Page 13...
Page 20: ...Page 18 LM5200 Operating Manual Operational Dimensions...
Page 21: ...P N 66188 Rev 5 Page 19 Conventional Machining Area Ram at Maximum Recommended Offset...
Page 22: ...Page 20 LM5200 Operating Manual Gantry Machining Area...
Page 23: ...P N 66188 Rev 5 Page 21 Overhead View...
Page 24: ...Page 22 LM5200 Operating Manual Overhead View Ram at Maximum Recommended Offset...
Page 25: ...P N 66188 Rev 5 Page 23 End View Side Milling...
Page 27: ...P N 66188 Rev 5 Page 25 Standard Mounting Pattern Gantry Mounting Pattern...
Page 64: ...Page 62 LM5200 Operating Manual...
Page 65: ...P N 66188 Rev 5 Page 63...
Page 66: ...Page 64 LM5200 Operating Manual...
Page 67: ...P N 66188 Rev 5 Page 65...
Page 68: ...Page 66 LM5200 Operating Manual...
Page 69: ...P N 66188 Rev 5 Page 67...
Page 70: ...Page 68 LM5200 Operating Manual...
Page 71: ...P N 66188 Rev 5 Page 69...
Page 72: ...Page 70 LM5200 Operating Manual...
Page 73: ...P N 66188 Rev 5 Page 71...
Page 74: ...Page 72 LM5200 Operating Manual...
Page 75: ...P N 66188 Rev 5 Page 73 This page intentionally left blank...
Page 76: ...Page 74 LM5200 Operating Manual...
Page 77: ...P N 66188 Rev 5 Page 75...
Page 78: ...Page 76 LM5200 Operating Manual...
Page 79: ...P N 66188 Rev 5 Page 77...
Page 80: ...Page 78 LM5200 Operating Manual...
Page 81: ...P N 66188 Rev 5 Page 79...
Page 82: ...Page 80 LM5200 Operating Manual...
Page 83: ...P N 66188 Rev 5 Page 81...
Page 84: ...Page 82 LM5200 Operating Manual...
Page 85: ...P N 66188 Rev 5 Page 83...
Page 86: ...Page 84 LM5200 Operating Manual...
Page 87: ...P N 66188 Rev 5 Page 85...
Page 88: ...Page 86 LM5200 Operating Manual...
Page 89: ...P N 66188 Rev 5 Page 87...
Page 90: ...Page 88 LM5200 Operating Manual...
Page 91: ...P N 66188 Rev 5 Page 89...
Page 92: ...Page 90 LM5200 Operating Manual...
Page 93: ...P N 66188 Rev 5 Page 91...
Page 94: ...Page 92 LM5200 Operating Manual...
Page 95: ...P N 66188 Rev 5 Page 93...
Page 96: ...Page 94 LM5200 Operating Manual...
Page 97: ...P N 66188 Rev 5 Page 95...
Page 98: ...Page 96 LM5200 Operating Manual...
Page 99: ...P N 66188 Rev 5 Page 97...
Page 100: ...Page 98 LM5200 Operating Manual This page intentionally left blank...
Page 101: ......
Page 102: ......