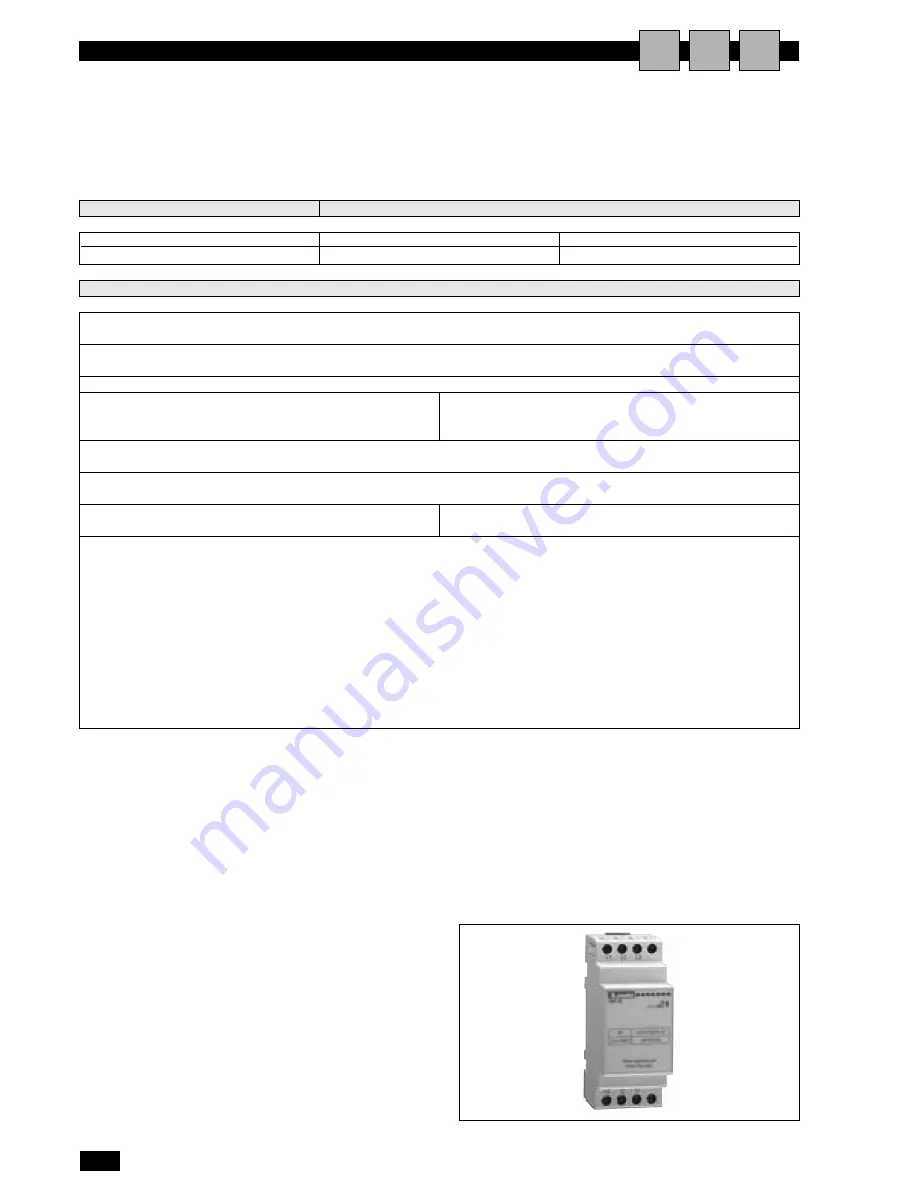
8
English 01/07
ACCURATE AX* - AW*
COMMISSIONING PROCEDURE
Arm
the cutout in the auxiliary circuits;
Arm
all the cutouts on the electrical panel;
Power up the air-conditioner electrical panel and close the main
disconnecting switch on the unit (position 'I');
Check
that the control board is powered;
Check
that both the
LEDs relating to the phase sequence relay (RSF) are on; the yellow
LED indicates power, the green LED indicates that the sequence of
phases is correct.
If the green LED is off, disconnect power supply from the units, rever-
se two phases of the power cable and restart the commissioning pro-
cedure.
(In the units with sump heaters)
After having powered up the air-conditioner, wait at least 12 hours
before starting so as to suitably heat the oil in the compressors.
During extended shutdown there may be spontaneous migration of
refrigerant to the compressor sump, which at the start may cause the
oil to foam and consequent damage due to insufficient lubrication.
As a result, do not disconnect power during weekly pauses;
Open the on-off valves in the refrigerant circuits and check that the
air-cooled remote condensers are connected (air-cooled models);
Check that the external radiators are connected and make sure there
is water flow for cooling (water-cooled models);
Check that the sections of corrugated pipe with the function of drain
trap (both inside and outside of the air-conditioner) have been filled
with water during installation.
AT LEAST 12 HOURS AFTER POWER UP:
Start
the air-conditioner using the buttons on the user terminal;
If an alarm is activated
refer to the controller instruction manual.
COMMISSIONING AND TESTING
A
I
U
EMPTYING THE REFRIGERANT CIRCUIT AND
CHARGING WITH REFRIGERANT
The water-cooled units (AWO, AWU) are already charged with
refrigerant, either R407C or R22 (check the rating plate on the
unit and the compressors to see which type of refrigerant is
used).
The air-cooled units (AXO, AXU) are pre-charged with nitrogen
to prevent moisture from entering the circuit; in this case, the
refrigerant charge must be completed by the installer, following
the instructions shown in this paragraph.
R22
R407C
Open any valves in the unit or in the system to ensure that all the components are involved in the emptying operation;
Connect a high efficiency vacuum pump to the Schrader fittings or to the 1/4” SAE fittings on the compressor suction and discharge side;
Connect a cylinder of refrigerant to the charge fittings.
Empty the lines, ensuring an absolute pressure of less than 100
Pa (0.7 mm Hg) for an extended period, so as to remove the air
and any traces of moisture.
Empty the lines, ensuring an absolute pressure of less than 10 Pa
(0.07 mm Hg) for an extended period, so as to remove the air
and any traces of moisture.
The circuit should be emptied slowly and maintained for an extended period, rather than performed too quickly.
Wait 100 seconds and check that the absolute pressure does not rise above 200 Pa.
Break the vacuum by pre-charging from the cylinder of R22
refrigerant.
Break the vacuum by pre-charging from the cylinder of R407C
refrigerant in the liquid phase.
After having started the compressor, complete the charge slowly, until the pressure stabilises in the lines and the gas bubbles disappear
from the flow indicator;
Refrigerant
Type of oil
R22 (Mineral oil)
Suniso 3 GS
White oil
R407C (POE)
Mobil EAL Arctic 22 CC
ICIEMKARATE RL 32S CF
The charge must be checked at the environmental design conditions
and with a discharge pressure of around 18 bar (equal to a saturated
temperature of 48°C); for units with on-off condenser control, par-
tially close the intake to stop the condenser fan from repeatedly
starting-stopping.
Make sure that the subcooling of the liquid at the thermostatic valve
intake is between 3 and 5°C less than the condensing temperature
read on the pressure gauge and that the superheating of the vapour
at the evaporator outlet is around 5 °C.
The charge must be checked at the environmental design conditions
and with a discharge pressure of around 18 bar (equal to a dew
point of 48°C and boiling point of 43°C); for units with on-off con-
denser control, partially close the intake to stop the condenser fan
from repeatedly starting-stopping.
Make sure that the subcooling of the liquid at the thermostatic valve
intake is between 3 and 5°C less than the condensing temperature
read on the pressure gauge and that the superheating of the vapour
at the evaporator outlet is around 5 °C.
Summary of Contents for ACCURATE
Page 2: ......
Page 26: ...24 English 01 07 ACCURATE AX AW ...
Page 27: ......
Page 28: ...Dé Longhi Group Via L Seitz 47 31100 Treviso Italia COD 5787001000 ...