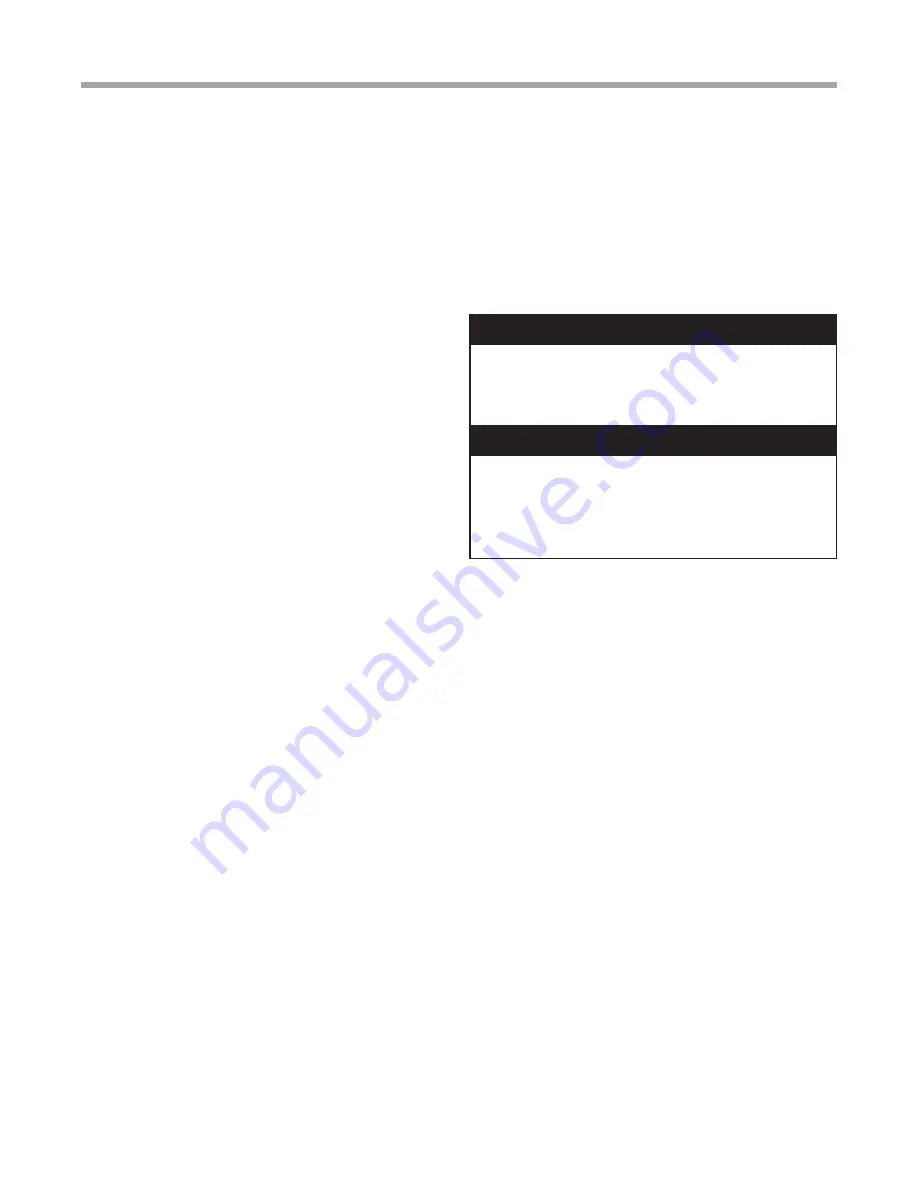
39
R e s i d e n t i a l H & V - 6 0 H z H F C - 4 1 0 A
R e v : O c t o b e r 5 , 2 0 2 1
c l i m a t e m a s t e r.c o m
Unit Start-Up & Operating Conditions
Unit and System Checkout
BEFORE POWERING SYSTEM, please check the following:
UNIT CHECKOUT
Balancing/shutoff valves:
Insure that all isolation valves
are open and water control valves are wired.
Line voltage and wiring:
Verify that voltage is within
an acceptable range for the unit and wiring and fuses/
breakers are properly sized. Verify that low voltage wiring
is complete.
Unit control transformer:
Insure that transformer has
the properly selected voltage tap. Residential 208-
230V units are factory wired for 230V operation unless
specified otherwise.
Loop/water piping is complete and purged of air. Water/
piping is clean.
Antifreeze has been added if necessary.
Entering water and air:
Insure that entering water and
air temperatures are within operating limits of Table 8.
Low water temperature cutout:
Verify that low water
temperature cut-out on the CXM/CXM control is properly
set.
Unit fan:
Manually rotate fan to verify free rotation and
insure that blower wheel is secured to the motor shaft. Be
sure to remove any shipping supports if needed. DO NOT
oil motors upon start-up. Fan motors are pre-oiled at the
factory. Check unit fan speed selection and compare to
design requirements.
Condensate line:
Verify that condensate line is open
and properly pitched toward drain.
HWG pump is disconnected unless piping is completed
and air has been purged from the system.
Water flow balancing:
Record inlet and outlet water
temperatures for each heat pump upon startup. This
check can eliminate nuisance trip outs and high velocity
water flow that could erode heat exchangers.
Unit air coil and filters:
Insure that filter is clean and
accessible. Clean air coil of all manufacturing oils.
Unit controls:
Verify that CXM field selection options are
properly set. Low voltage wiring is complete.
Blower speed is set.
Service/access panels are in place.
SYSTEM CHECKOUT
System water temperature:
Check water temperature
for proper range and also verify heating and cooling set
points for proper operation.
System pH:
Check and adjust water pH if necessary to
maintain a level between 6 and 8.5. Proper pH promotes
longevity of hoses and fittings (see Table 3).
System flushing:
Verify that all air is purged from the
system. Air in the system can cause poor operation or
system corrosion. Water used in the system must be
potable quality initially and clean of dirt, piping slag,
and strong chemical cleaning agents. Some antifreeze
solutions may require distilled water.
Flow Controller pump(s):
Verify that the pump(s) is
wired, purged of air, and in operating condition.
System controls:
Verify that system controls function
and operate in the proper sequence.
Low water temperature cutout:
Verify that low water
temperature cut-out controls are set properly
(FP1 - JW3).
Miscellaneous:
Note any questionable aspects of
the installation.
Unit Start-up Procedure
1. Turn the thermostat fan position to “ON.” Blower
should start.
2. Balance air flow at registers.
3. Adjust all valves to their full open position. Turn on the
line power to all heat pump units.
4. Room temperature should be within the minimum-
maximum ranges of Table 8b. During start-up checks,
loop water temperature entering the heat pump should
be between 30°F [-1°C] and 95°F [35°C].
5. Two factors determine the operating limits of water
source heat pumps, (a) return air temperature, and (b)
water temperature. When any one of these factors is at a
minimum or maximum level, the other factor must be at
normal level to insure proper unit operation.
a. Adjust the unit thermostat to the warmest setting.
Place the thermostat mode switch in the “COOL”
position. Slowly reduce thermostat setting until the
compressor activates.
b. Check for cool air delivery at the unit grille within a
few minutes after the unit has begun to operate.
Note: Units have a five minute time delay in the
control circuit that can be bypassed on the CXM/
CXM control board as shown below in Figure 27.
See controls description for details.
c. Verify that the compressor is on and that the water
flow rate is correct by measuring pressure drop
through the heat exchanger using the P/T plugs and
comparing to Tables 9.
d. Check the elevation and cleanliness of the
condensate lines. Dripping may be a sign of a
blocked line. Check that the condensate trap is filled
to provide a water seal.
⚠
CAUTION!
⚠
⚠
CAUTION!
⚠
CAUTION!
Verify that ALL water control valves are open
and allow water flow prior to engaging the compressor.
Freezing of the coax or water lines can permanently
damage the heat pump.
CAUTION!
To avoid equipment damage, DO NOT
leave system filled in a building without heat during the
winter unless antifreeze is added to the water loop. Heat
exchangers never fully drain by themselves and will
freeze unless winterized with antifreeze.