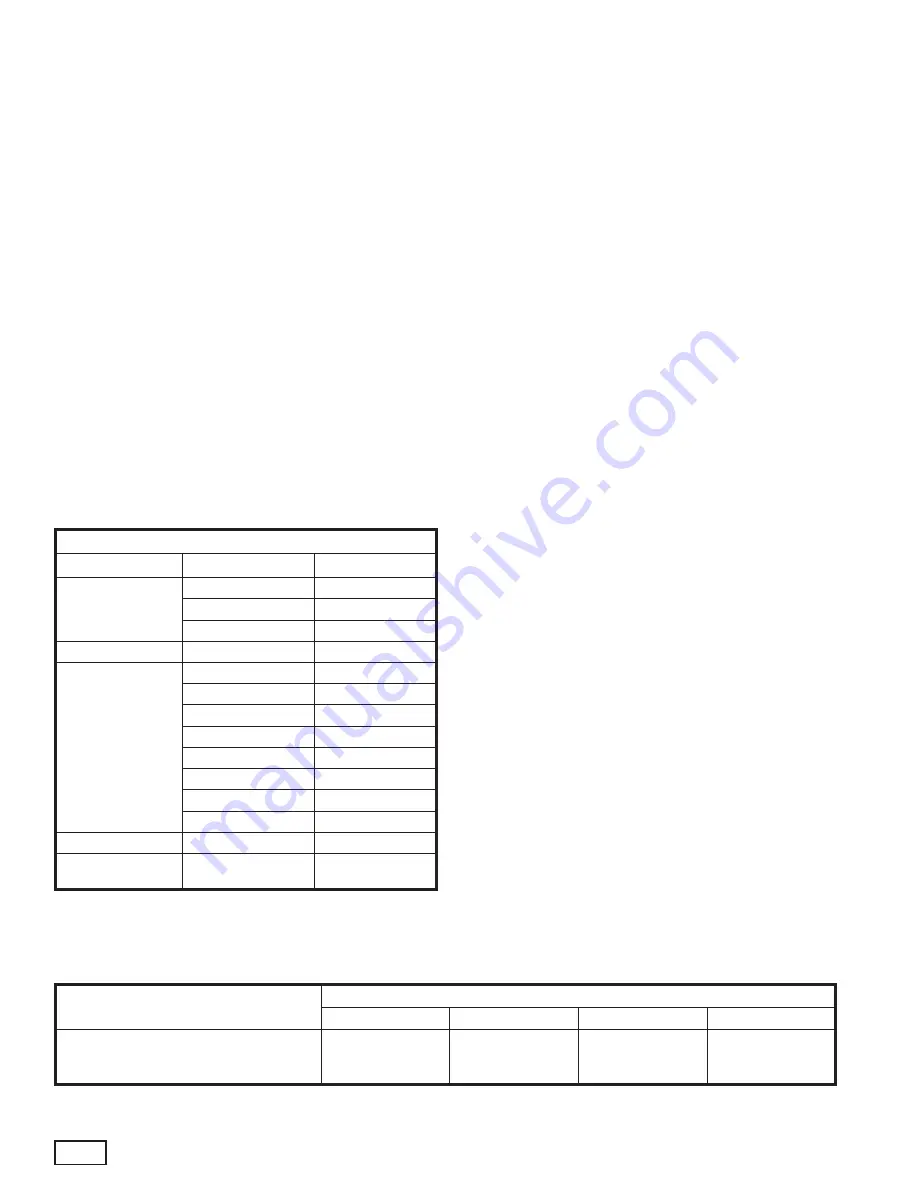
Tranquility THW - 50 & 60Hz R410A - ClimateMaster Geothermal Heat Pumps - Rev.: 30 June, 2008B
10
GROUND-LOOP HEAT PUMP APPLICATIONS
Piping Installation
The typical closed loop ground source system is shown in
Figure 3. All earth loop piping materials should be limited
to only polyethylene fusion in inground sections of the
loop. Galvanized or steel fitting should not be used at any
time due to their tendency to corrode. All plastic to metal
threaded fittings should be avoided due to their potential
to leak in earth coupled applications and a flanged fitting
substituted. P/T plugs should be used so that flow can
be measured using the pressure drop of the unit heat
exchanger in lieu of other flow measurement means.
Earth loop temperatures can range between 25-110°F
[-3.9 - 43.3°C]. Upon completion of the ground loop piping,
pressure test the loop to assure a leak free system.
Horizontal Systems: test individual loops as installed. Test
entire system when all loops are assembled.
Vertical U-Bends and Pond Loop Systems: test vertical U-
bends and pond loop assemblies prior to installation with
a hydrostatic test pressure of at least 100 psi [689 kPa].
Flushing the Earth Loop
Once piping is completed between the unit, flow center
and the ground loop (Figure 3), final purging and charging
of the loop is needed. A flush cart (at least a 1.5 hp [1.1
kW] pump) is needed to achieve adequate flow velocity in
the loop to purge air and dirt particles from the loop itself.
An antifreeze solution is used in most areas to prevent
freezing. All air and debris must be removed from the
earth loop piping system before operation. Flush the loop
with a high volume of water at a high velocity (2 fps [0.6
m/s] in all piping) both directions. The steps below must
be followed for proper flushing. Fill loop with water from
a garden hose through flush cart before using flush cart
pump to ensure an even fill. Once full, do not allow the
water level in the flush cart tank to drop below the pump
inlet line or air can be pumped back out to the earth loop.
Try to maintain a fluid level in the tank above the return
tee so that air can not be continuously mixed back into the
fluid. 50 psi [345 kPa] surges can be used to help purge
air pockets by simply shutting off the return valve going
into the flush cart reservoir. This ‘dead heads’ the pump to
50 psi [345 kPa]. To dead head the pump until maximum
pumping pressure is reached, open the valve back up
and a pressure surge will be sent through the loop to help
purge air pockets from the piping system. Notice the drop
in fluid level in the flush cart tank.
If air is purged from
the system, the level will drop only 1-2 [25-50mm]
inches in a 10" [254mm] diameter PVC flush tank
(about a half gallon) since liquids are incompressible
.
If the level drops more than this, flushing should continue
since air is still being compressed in the loop fluid. Do this
a number of times.
When the fluid level drops less than 1-2" [25-50mm] in
a 10" [254mm] diameter tank the flow can be reversed.
Finally the dead head test should be checked again for
an indication of air in the loop.
This fluid level drop is
your only indication of air in the loop.
Table 3: Approximate Fluid Volume (gal.) per
100' of Pipe
Table 4: Antifreeze Percentages by Volume
Type
Minimum Temperature for Low Temperature Protection
10°F [-12.2°C]
15°F [-9.4°C]
20°F [-6.7°C]
25°F [-3.9°C]
Methanol
100% USP food grade Propylene Glycol
Ethanol*
25%
38%
29%
21%
25%
25%
16%
22%
20%
10%
15%
14%
* Must not be denatured with any petroleum based product
Fluid Volume (gal [liters] per 100’ [30 meters) Pipe)
Pipe
Size
Volume (gal) [liters]
Copper
1”
4.1 [15.3]
1.25”
6.4 [23.8]
2.5”
9.2 [34.3]
Rubber Hose
1”
3.9 [14.6]
Polyethylene
3/4” IPS SDR11
2.8 [10.4]
1” iPS SDR11
4.5 [16.7]
1.25” IPS SDR11
8.0 [29.8]
1.5” IPS SDR11
10.9 [40.7]
2” IPS SDR11
18.0 [67.0]
1.25” IPS SCH40
8.3 [30.9]
1.5” IPS SCH40
10.9 [40.7]
2” IPS SCH40
17.0 [63.4]
Unit Heat Exchanger
Typical
1.0 [3.8]
Flush Cart Tank
10” Dia x 3ft tall
[254mm x 91.4cm tall]
10 [37.9]