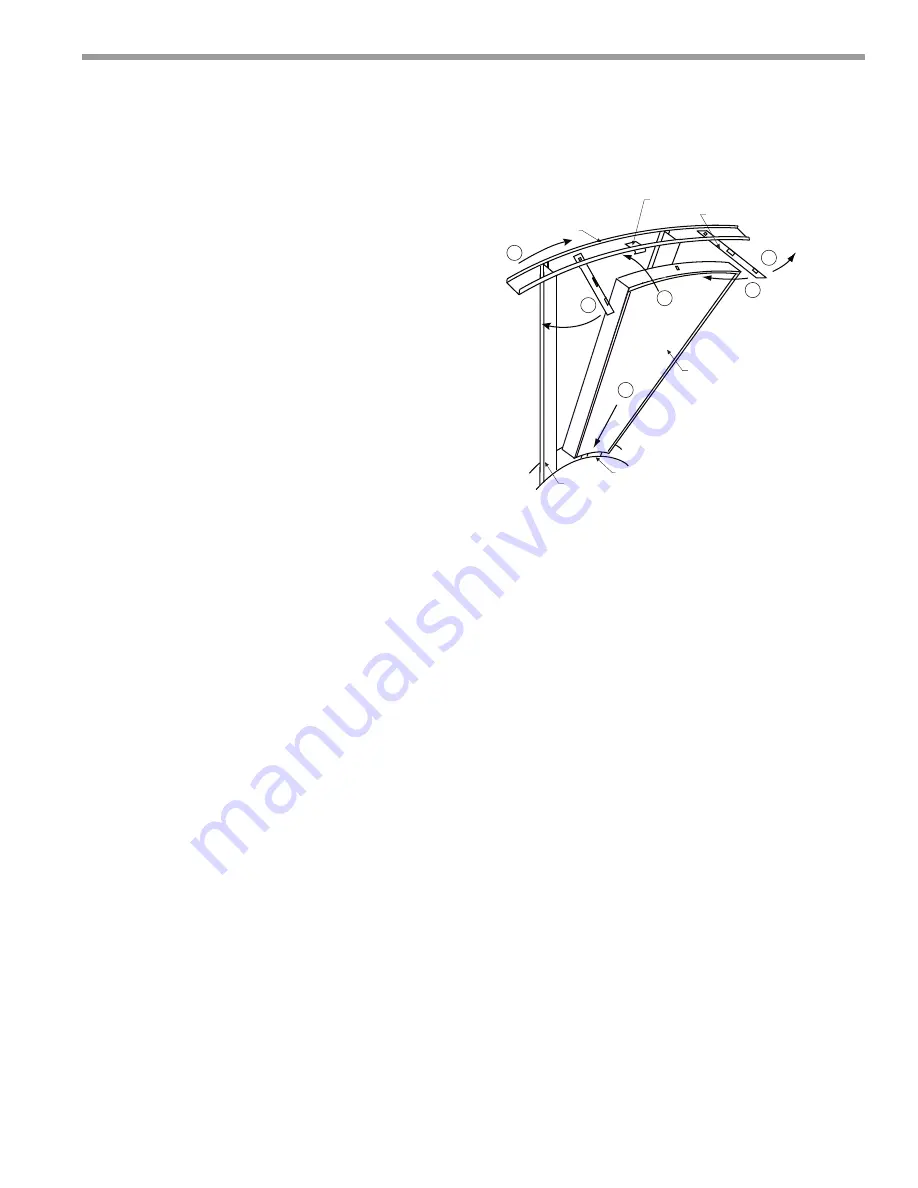
T H E S M A R T S O L U T I O N F O R E N E R G Y E F F I C I E N C Y
T (ERV) Series
R e v. : 1 5 A p r i l , 2 0 1 6
5
c l i m a t e m a s t e r. c o m
lowest tension at which the belt will not slip under peak
load conditions.
1. Disconnect main power to unit before making
adjustment to economizer and/or ERV unit.
2. Replace ERV control access cover.
3. Set thermostat to normal operating position.
4. Restore power to unit.
Maintenance
1. All motors use pre-lubricated sealed bearings; no
further lubrication is necessary.
2. Make visual inspection of motors, belts and wheel
rotating bearings during routine maintenance.
3. Eight pie-shaped segments, are seated on stops
between the segment retainer which pivots on the
wheel rim and secured to the hub and rim of wheel.
Annual inspection of the self cleaning wheel is
recommended. With power disconnected, remove
ERV access panels (rear) and unplug [J150 & P150]
(Refer to wiring diagram in this instruction
manual)
. Remove segment and wash with water and/
or mild detergent.
4. To install wheel segments follow steps A through
E .
See Figure 1.
Reverse procedure for segment
removal.
A. Unlock two segment retainers (one on each side of
the selected segment opening.
B. With the embedded stiffener facing the motor side,
insert the nose of the segment between the hub
plates.
C. Holding segment by the two outer corners, press
the segment towards the center of the wheel
and inwards against the spoke flanges. If hand
pressure does not fully seat the segment, insert
the flat tip of a screw driver between the wheel
rim and outer corners of the segment and apply
downward force while guiding the segment into
place.
D. Close and latch each segment retainer under
segment retaining catch.
E. Slowly rotate the wheel 180º. Install the second
segment opposite the first for counterbalance.
Rotate the two installed segments 90º to balance
the wheel while the third segment is installed.
Rotate the wheel 180º again to install the fourth
segment opposite the third. Repeat this sequence
with the remaining four segments.
Pulley Kit Installation
The units are shipped from the factory at the low static
setting. Pulley kits are available for the medium and high
static settings. To install a pulley kit.
1. Check content of pulley kit, if pulley kit contains:
a. An adjustable sheave and a fixed pitch pulley then
remove belt and both motor and blower pulley
b. An adjustable sheave then remove the motor
pulley.
c. A fixed pitch pulley then remove the blower pulley.
2. Replace pulley(s) with the pulley(s) from pulley kit.
Make sure each pulley is installed with a key. Tighten
the set screw on the pulley(s) to 100 in.lb.
3. Install the belt that came with the pulley kit. Tension
belt as explained in the blower speed adjustment
section.
4. Check the speed of the blower. Adjust the motor
sheave to increase or decrease the speed of the
blower. See blower adjustment section.
B
C
A
D
E
D
HUB
SEGMENT
SPOKE
SEGMENT RETAINER CATCH
WHEEL RIM
SEGMENT RETAINER
Figure 1