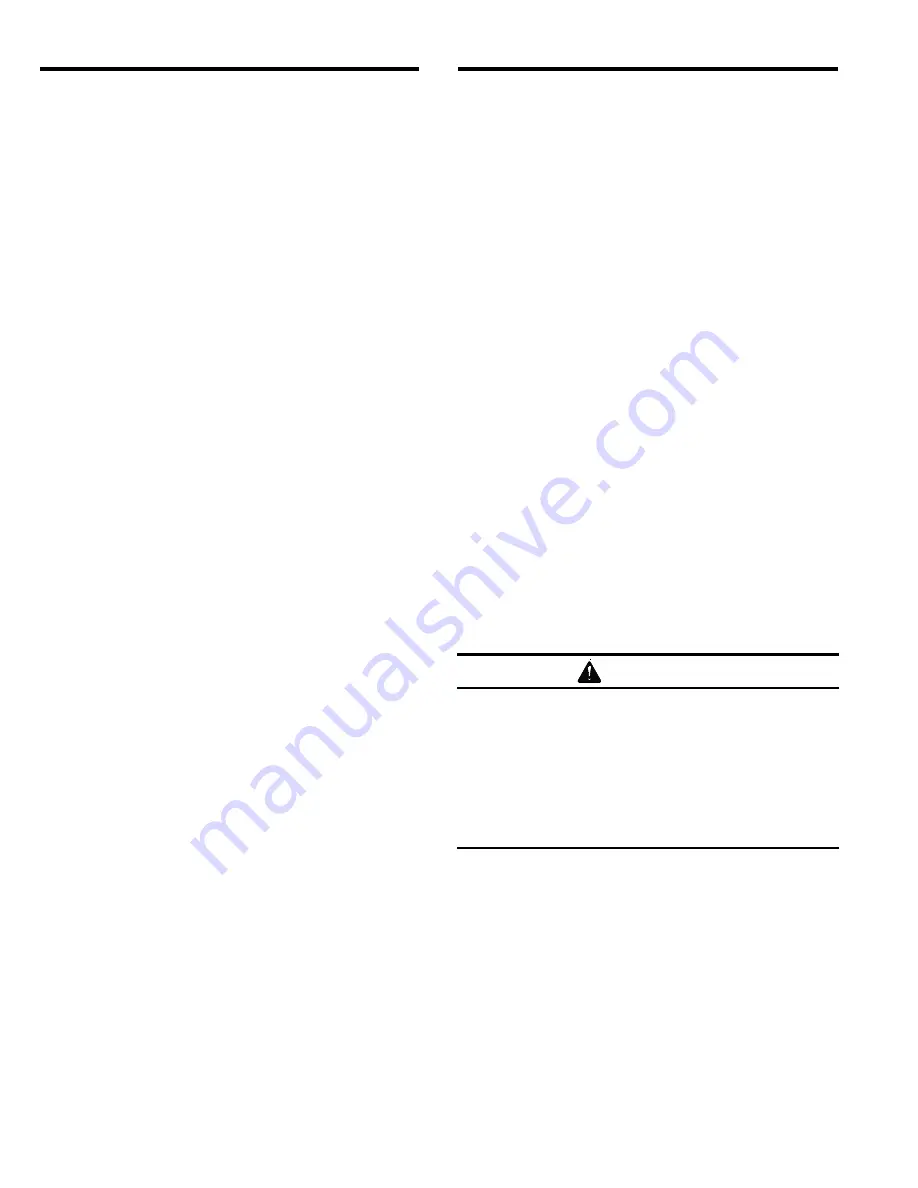
POOL PAL BLAST MACHINE
Page 8
© 2008 CLEMCO INDUSTRIES CORP.
•
www.clemcoindustries.com
•
Manual No. 24813
3.6
Adjust Abrasive Metering Valve
3.6.1
Abrasive flow is adjusted with the knob.
3.6.2
Begin adjustments with the metering valve
closed. The valve is closed when the metering knob is
turned fully clockwise.
3.6.3
While blasting, increase abrasive flow by turning
the knob counterclockwise at 1/4 turn increments. Allow
time for the flow to stabilize before readjusting.
3.6.4
Optimum abrasive flow depends on the type and
size of abrasive and blasting pressure, and can best be
determined by experience. Use as little abrasive as
possible while maintaining the maximum cleaning rate.
The air/abrasive mixture should be mainly air. Abrasive
exiting the nozzle should barely discolor the air when
seen against a contrasting background.
3.7
Loading Abrasive into the Blast Machine
3.7.1
Depressurize machine using normal
procedures. The pop-up valve automatically drops when
air is expelled from the machine and pressure equalizes.
3.7.2
Load
abrasive
into the machine by pouring it into
the concave head. Using an optional screen, placed
over the head, prevents large objects from falling inside.
A screen is recommended to keep objects such as
pieces of abrasive bags or other objects from falling into
the machine. Foreign objects will jam the machine.
Abrasive
flows through the fill port into the machine.
Keep the abrasive level below the pop-up valve.
Abrasive on the pop-up valve could be forced up and out
of the top of the machine when the machine is
pressurized.
NOTE: Use only abrasive specifically manufactured
for blast cleaning, and that is compatible with the
surface being blasted.
3.7.3
After the machine is filled, use normal
procedures to begin blasting.
3.8
Emptying the Machine of Abrasive
3.8.1
When working in environments subject to
extreme temperature changes, or very humid conditions,
condensation may develop inside the machine.
Condensation wets abrasive and causes flow problems.
To prevent this, empty the machine of all abrasive when
shutting down for the day. This will eliminate trouble
from moist abrasive when starting a new day's blasting.
One way to avoid having to empty the machine is to load
only as much abrasive as will be used during the work
period. If the machine must be purged of abrasive, do
the following:
3.8.2
With the blast machine off, turn the blast
pressure to approximately 40-50 psi, close the choke
valve and set the abrasive metering valve at full open.
3.8.3
To prevent rapid wear of the nozzle holder
threads, the nozzle should be firmly attached to the
nozzle holder. Removal of the nozzle is not
recommended. If circumstances require the nozzle to be
removed, also remove the nozzle washer. Purging the
machine without a nozzle, will eventually erode the
thread area of the nozzle holder, which could cause a
hazardous condition.
3.8.4
Point the nozzle (or hose end) into a drum or
suitable container, or in the direction the abrasive is to
be disposed.
3.8.5
Hold the hose securely (do not leave the hose
unattended), and pressurize the machine by activating
the control handle. Be prepared for surging, or recoil of
the hose, which can be severe.
3.8.6
When the machine is empty, release the control
handle lever, open the safety petcock, and open the
choke valve.
3.8.7
If the nozzle was removed, thoroughly inspect
the nozzle holder threads for wear before installing the
nozzle washer and attaching the nozzle.
WARNING
Inspect he threads on the nozzle and nozzle
holder each time the nozzle is secured to the
holder. Check threads for wear, and make sure
nozzle holder securely grips the nozzle. The
nozzle washer must also be inspected for wear.
Worn nozzle washers cause thread erosion. A
loose fitting nozzle may eject from the holder
under pressure and cause severe injury.
3.9 Shutdown
3.9.1
When finished blasting, and after cleanup is
completed, remove the respirator outside the respirator-
use area and where the air is safe to breathe.
3.9.2
Close the air supply valve at the compressor.
3.9.3
Drain
the air filter (bottom section of the filter/
regulator combination), drain receiver tank, and water
collecting devices, and bleed the compressed-air supply
hoses.