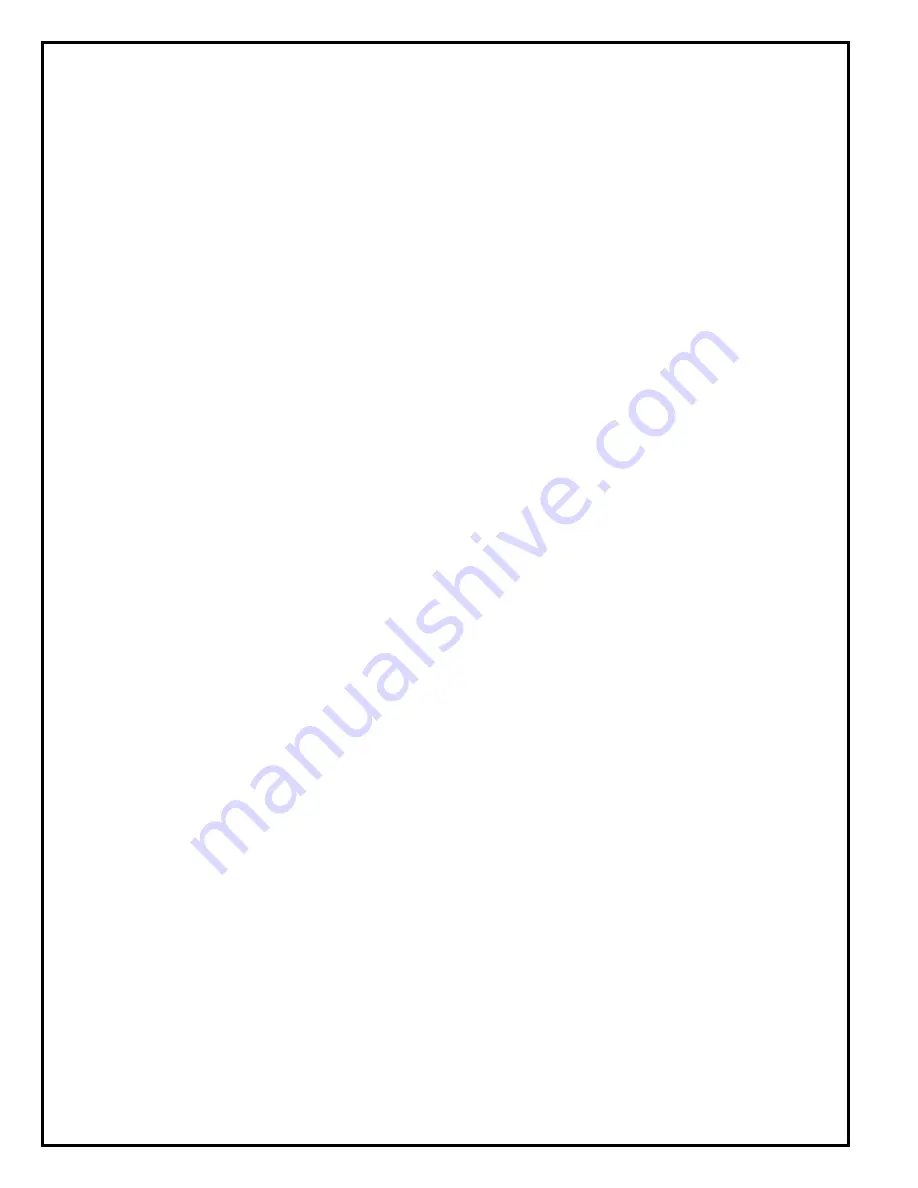
4
OPERATION
This tool is designed to operate on 90 psig (6.2 bar) air pressure,
measured at the tool's air inlet with the tool running, using a 3/8"
(10 mm) hose up to 8' (2.5m) in length. Installation of an auto-
matic in-line filter-regulator- lubricator is highly recommended to
supply the tool with clean lubricated air. This will keep the tool in
sustained operation and increase its service life.
The air hose should be cleared of accumulated dirt and moisture,
then 1 teaspoon (5ml) of 10W machine oil should be poured into
the tool's air inlet before connecting the hose to the tool.
IMPORTANT: If a quick-disconnect coupling is used with the tool.
it should be separated from the tool by a whip hose.
All tools and hoses should be installed by trained competent per-
sonnel. Hoses and fittings should be inspected regularly for wear
or damage and replaced if necessary.
The correct socket retainer should always be used on your tool.
Tools equipped with a square drive commonly use an "O"-ring
and pin for a socket retention. Tools equipped with a spline drive
have an integral socket retainer pin, and a screwdriver or similar
tool is used to depress the socket retainer plunger to either install
or remove the socket. Always use the socket retainer compo-
nents recommended by the socket manufacturer. Never substi-
tute wire, nails, or welding rods for retaining pins. Always use
sockets designed for impact wrench service.
The air supply to the tool should always be off when changing
sockets.
Sockets, retainers, and drives should be inspected regularly for
wear or damaged parts and the parts should be replaced if nec-
essary.
LUBRICATION
An automatic in-line filter-lubricator is recommended as it in-
creases tool life and keeps the tool in sustained operation. The
inline lubricator should be regularly checked and filled with a good
grade of 10W machine oil. Proper adjustment of the in-line lubri-
cator is performed by placing a sheet of paper next to the ex-
haust ports and holding the throttle open approximately 30 sec-
onds. The lubricator is properly set when a light stain of oil col-
lects on the paper. Excessive amounts of oil should be avoided.
In the event an in-line lubricator is not used, the oil reservoir in
the handle should be utilized.
The oil reservoir marked "30W oil" should be checked periodi-
cally. The tool should be held with the rear of the tool up and the
two oil plugs should be removed. Fill the reservoir with 30W oil
until it comes out the other oil plug hole.
STORAGE
In the event that it becomes necessary to store the tool for an
extended period of time (overnight, weekend, etc.), it should re-
ceive a generous amount of lubrication at that time and again
when returned to service. The tool should be stored in a clean
and dry environment.
DISASSEMBLY
Loosen and remove the four (4) housing bolts. This will allow the
anvil housing and impact mechanism to be removed from the
front of the motor housing. The motor unit may now be slipped
out the rear of the motor housing.
Remove the anvil and anvil timing pin from the front of the cam
shaft. Clamp the hammer in a soft-jawed vise with the spring cap
up. Depress the spring cap and remove the two (2) spring keep-
ers. This will allow the cam shaft and related components to be
removed from the rear of the hammer.
Slip the two (2) bearing plates off the rotor and remove the cylin-
der and six (6) rotor blades.
Unscrewing the air inlet bushing will allow the throttle valve to be
removed for inspection of the throttle valve seal. Remove the air
inlet screen for cleaning and inspection. The throttle valve bush-
ing may be removed by drilling and tapping a 1/4-20 N.C. thread
and using a 1/4-20 bolt to remove the bushing.
REASSEMBLY
All parts should be cleaned in a solvent and inspected for wear or
damage. If rotor blades measure less than 11/32" (8.7mm) on
either end they should be replaced. Replace blade if less than
11/32" (8.7mm) on either end.
Rotor bearings should be replaced if they feel rough or show ex-
cessive looseness. Rotor shaft seals and the anvil seal should
be replaced if they are badly worn or are no longer flexible .
IMPORTANT NOTE: During reassembly of the WP-2059 motor,
the blue coded bearing plate, No. 869745, is assembled to the
rear of the motor. During reassembly of the WP-2060B motor,
the blue coded bearing plate, No. 869745, is assembled to the
front of the motor.
Clean the bearing plates and anvil housing with a solvent and
coat the seal bores with " PERMATEX "Aviation Form-a-gasket
#3H. Allow to air dry at least four (4) minutes before pressing in
the seals. Press the rotor shaft seals into the bearing plates with
their "lips" facing outward (visible after assembly). Press the an-
vil seal into the anvil housing with its "lip" toward the rear of the
housing ("lip" not visible after assembly).
All impact mechanism parts should receive a thin coating of 30W
oil before reassembly. Insert the cam timing pin into the recess
located on the small O.D. of the cam and then install the cam and
pin into the rear of the hammer. Slip the cam shaft through the
cam and assemble the hammer spring and spring cap to the front
of the cam shaft. Depress the spring cap and insert the two (2)
spring keepers into the groove on the cam shaft. After assembly
of the complete tool, the tool should be held with the rear of the
tool up and 1-1/4 fluid ounces (40ml) of 30W oil should be added
to 30W oil fill hole. A few drops of 10W machine oil should be
poured into the air inlet of the tool to ensure lubrication of the
motor parts as soon as air is applied.
All tools should be tested after repair or replacement of parts to
ensure that they are functioning properly.