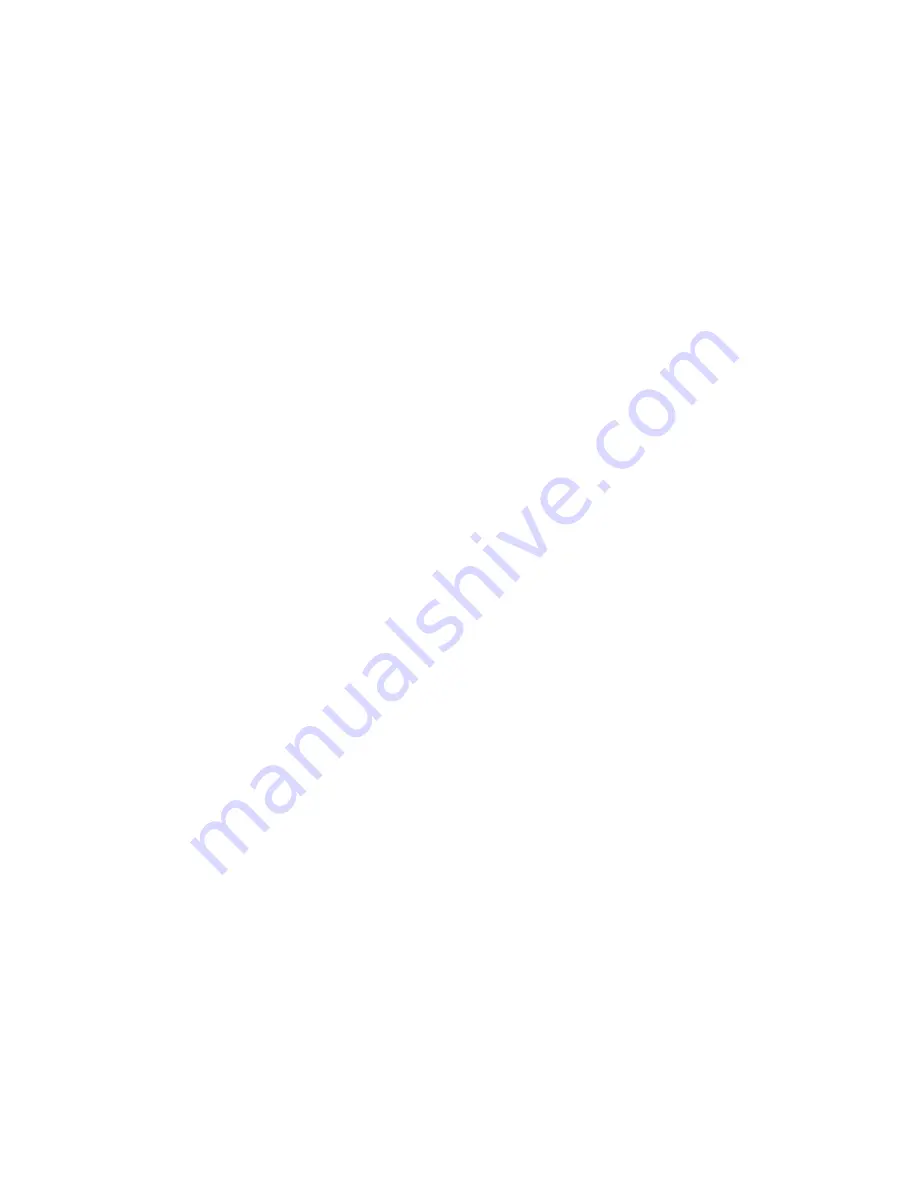
TO:
Owners, Operators and/or Maintenance Personnel
This operating manual presents information that will help to properly operate and care for the equipment. Study its con-
tents carefully. The unit will provide good service and continued operation if proper operating and maintenance instruc-
tions are followed. No attempt should be made to operate the unit until the principles of operation and all of the
components are thoroughly understood.
It is the responsibility of the owner to train and advise not only his or her personnel, but any contractor’s personnel who
are servicing, repairing, or operating the equipment, in all safety aspects.
Cleaver-Brooks equipment is designed and engineered to give long life and excellent service on the job. The electrical
and mechanical devices supplied as part of the unit were chosen because of their known ability to perform; however,
proper operating techniques and maintenance procedures must be followed at all times.
Any "automatic" features included in the design do not relieve the attendant of any responsibility. Such features merely
free him of certain repetitive chores and give him more time to devote to the proper upkeep of equipment.
It is solely the operator’s responsibility to properly operate and maintain the equipment. No amount of written instruc-
tions can replace intelligent thinking and reasoning and this manual is not intended to relieve the operating personnel of
the responsibility for proper operation. On the other hand, a thorough understanding of this manual is required before
attempting to operate, maintain, service, or repair this equipment.
Operating controls will normally function for long periods of time and we have found that some operators become lax in
their daily or monthly testing, assuming that normal operation will continue indefinitely. Malfunctions of controls lead to
uneconomical operation and damage and, in most cases, these conditions can be traced directly to carelessness and
deficiencies in testing and maintenance.
The operation of this equipment by the owner and operating personnel must comply with all requirements or regulations
of the insurance company and/or other authority having jurisdiction. In the event of any conflict or inconsistency between
such requirements and the warnings or instructions contained herein, please contact Cleaver-Brooks before proceeding.
Summary of Contents for PCS140e.1
Page 6: ...PCS140e 1 4 750 329...
Page 10: ...PCS140e 1 8 750 329...
Page 22: ...PCS140e 1 20 750 329...
Page 23: ...PCS140e 1 750 329 21 CHAPTER 6 PARTS...
Page 27: ......
Page 28: ...e mail info cleaverbrooks com Web Address http www cleaverbrooks com...