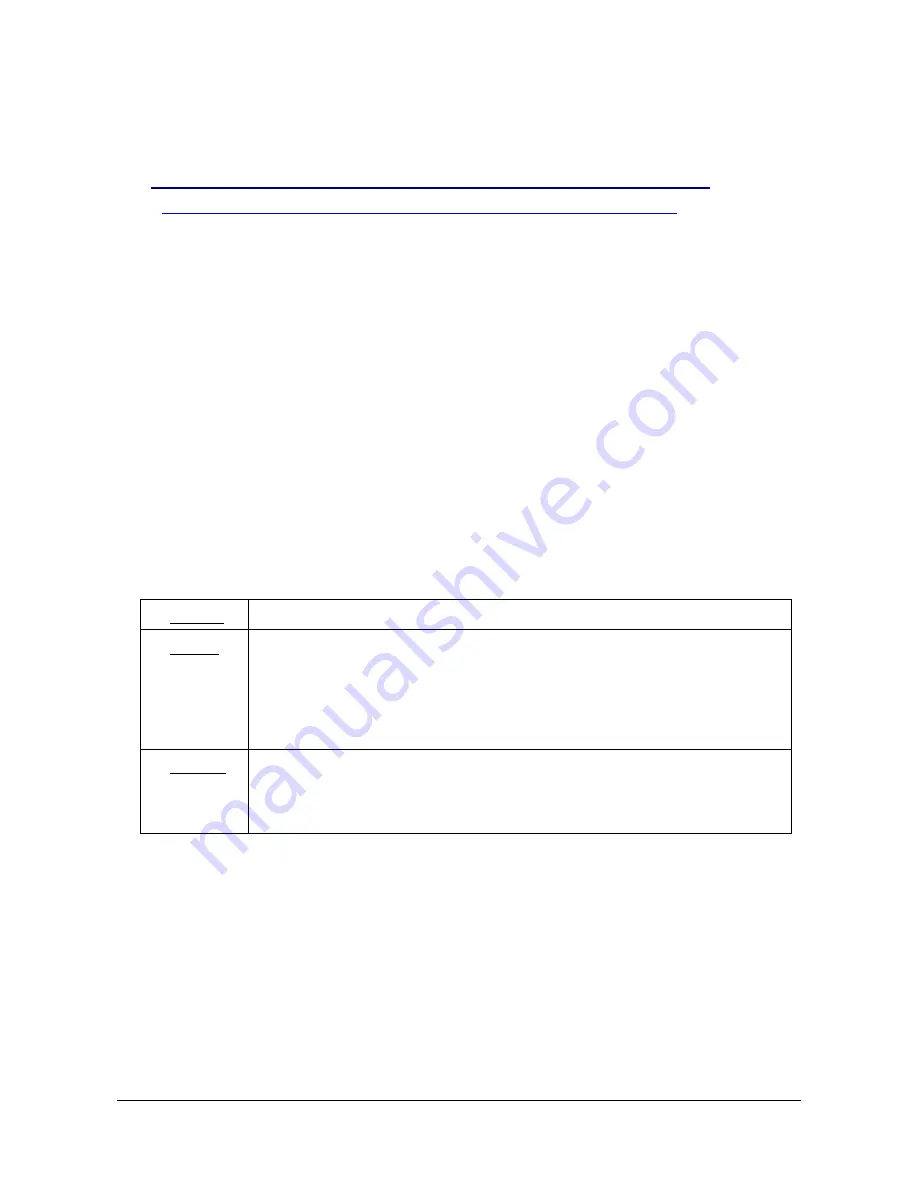
Clayton Steam Generator model EO-100-1M
PAGE 38 / 70
Instruction Manual, doc.nr.: MAN18206 Rev A PSC
•
After test is accomplished, regulate limit pressure switch and reset steam parameter to desired working
pressure.
•
Open steam discharge valve completely. Service or replace steam safety if test fails.
8.7
PERIODIC INSPECTION OF SAFETY, CONTROL AND MONITORING DEVICES.
8.7.1
SAFETY AND CONTROL DEVICES ON THE STEAM GENERATOR ASSEMBLY.
Each steam generator assembly is as a minimum to be provided with the instrumentation, monitoring, control
and safety devices as required by the harmonized standard EN 12952-7 and EN 12952-10 for the water steam
system and EN 12952-8
(which refers to EN 12953-7 for coil type boilers)
for the firing system.
The type and quantity of monitoring, control and safety devices depends on the mode of operation and the
options the user included in his order, and of the degree of automation.
The P& ID diagrams give a schematic presentation of these devices and the options.
EN 12952 distinguishes plants with permanent supervision
(attended operation)
or plants without permanent
supervision
(unattended operation).
For a generator operated under permanent supervision, the qualified generator/plant operator has to observe
the good functioning of the generator and its appurtenances on a permanent basis, either in the boiler room,
either in a control room adjacent to the boiler room and from which this operator has immediate and direct
access to the safety lock-out controls.
For plants operated without permanent supervision, supplemental monitoring, control and safety devices as
defined in EN 12952-7/8 are required for both the steam generator assembly and for the steam installation,
essentially to monitor and lock-out the generator when the limits are exceeded. See paragraphs 8.7.2
Clayton of Belgium offers 3 different options of steam generator equipment for the different modes of
operation :
1)
EN-AT :
Attended operation: this generator assembly is equipped for permanent supervision
2)
EN-24 :
Unattended 24h: this generator is supplemental equipped for maximum 24 hours
continuous operation without interruption and without permanent supervision.
The only difference with EN-1W is that the flame detector
(UV-cel)
and combustion
controller are approved for maximum 24 hours continuous operation though not of
the self-checking type. The burner shall be stopped at least once every 24 hours to
allow the combustion controller to do its test cycle.
3)
EN-1W :
Unattended 1 week: this generator assembly is supplemental equipped with a self-
checking flame detector and fail-safe, special design type approved and/or redundant
safety lock-out devices for continuous operation without interruption and without
permanent supervision during maximum 1 week.
Because of the very low, almost un-existing risks to create a steam explosion with a Clayton type steam
generator
(with all safety devices removed, Clayton did practical firing tests which resulted in a complete
coil burn down but no explosion),
and because of use of special limiting devices, the periodicity of the
periodic inspection and testing or checking of the functioning of these devices is specified in Table 8.7-1.
For a generator operated under permanent supervision, the interval of periodic testing and inspection shall be
as a minimum the same as for EN-24.