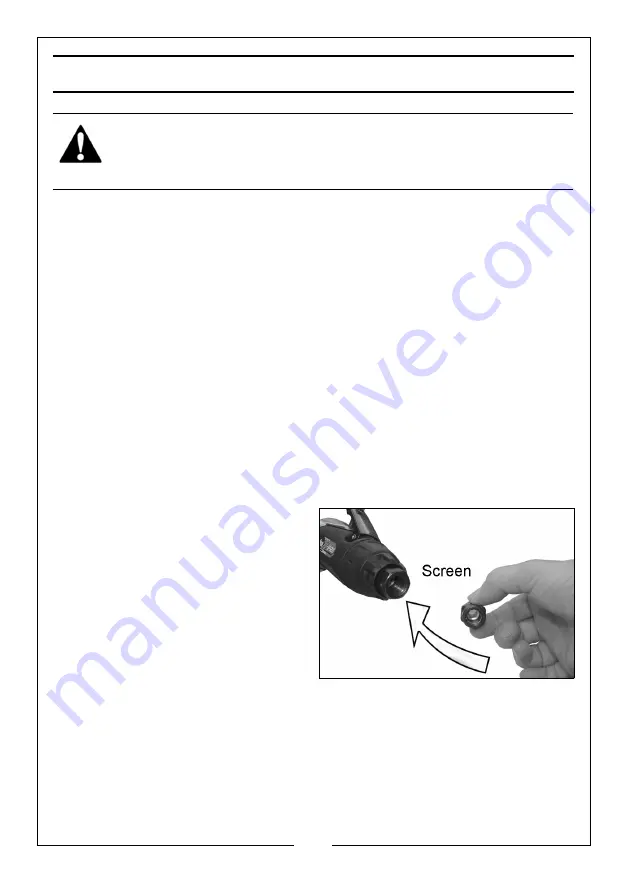
10
Parts & Service: 020 8988 7400 / E-mail: [email protected] or [email protected]
MAINTENANCE
Please note that factors other than the drills condition may effect its operation
and efficiency, such as reduced compressor output, excessive drain on the
airline, moisture or restrictions in the air-line, or the use of connectors of
improper size or poor condition which will reduce air supply.
DAILY
1. Before use, drain water from the air-line and compressor.
2. Lubricate the drill daily for optimum performance. Use CLARKE high quality
airline oil either via a lubricator in the air supply system or by placing a few
drops into the air inlet immediately before use. This should be carried out
regardless of whether or not an in-line lubricator is used.
CLEANING & OVERHAUL
1. Keep the drill clean and free from debris.
2. If the drill becomes sluggish and the air supply is of good quality, it may be
necessary to replace worn or damaged parts.
3. Grit or gum deposits in the
mechanism may eventually
reduce efficiency. This condition
can be corrected by cleaning the
air inlet filter and flushing out the
drill with gum solvent oil or an
equal mixture of SAE No10 oil and
paraffin.
4. Failing this, the drill should be
disassembled, thoroughly
cleaned, dried and reassembled.
You may prefer to take the drill to your CLARKE dealer if internal
maintenance is required.
WARNING: MAKE SURE THAT THE DRILL IS DISCONNECTED FROM THE AIR
SUPPLY BEFORE PERFORMING ANY CLEANING OR MAINTENANCE.
Summary of Contents for X-Pro CAT207
Page 16: ......