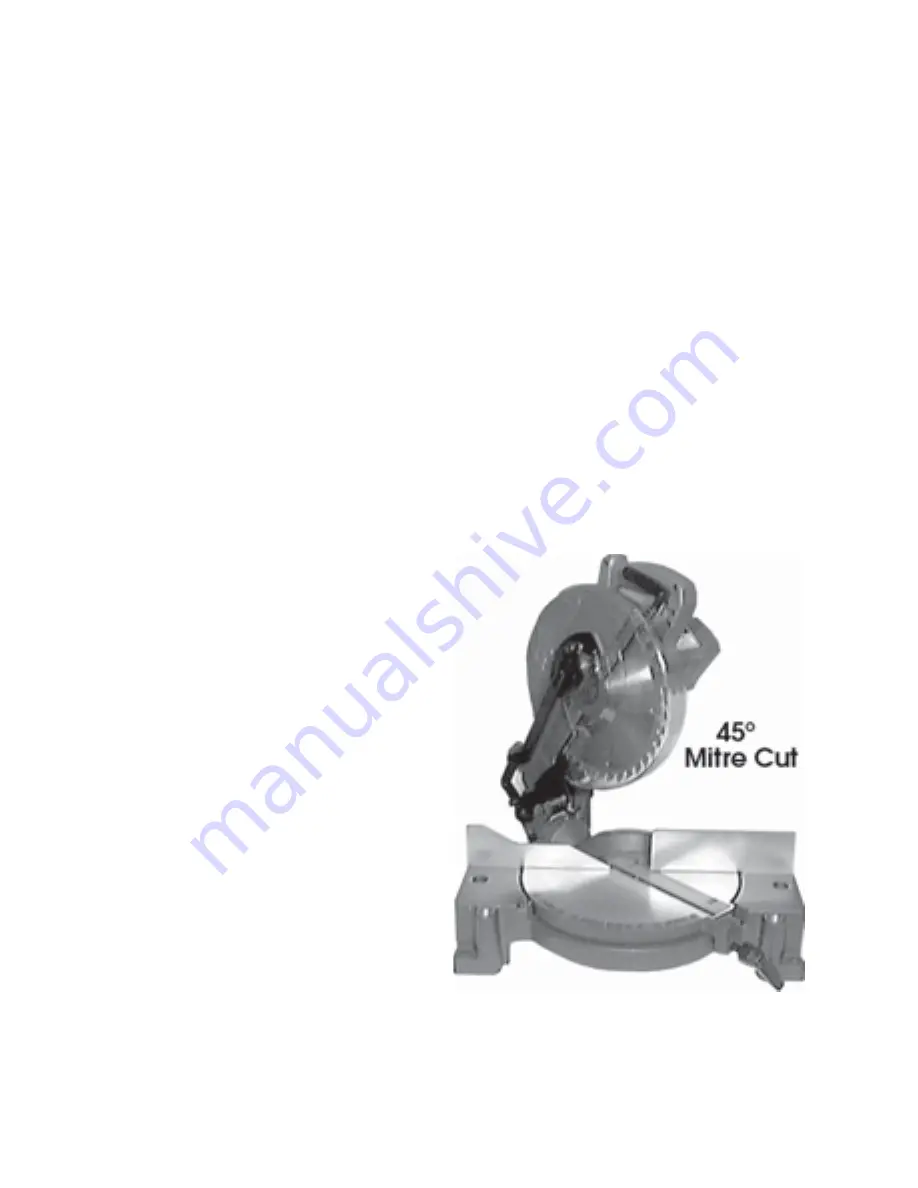
Allow the blade to reach full speed. If any unusual sounds or vibrations
occur, release the Trigger immediately and investigate the cause.
When satisfied, move the Head Release Lever, (C fig.7 and also shown in
fig.10), sideways with the fingers of your right hand, and gently lower the
head so that the blade comes into contact with the workpiece. Do not
force the blade, a light pressure is all that is required.
You will notice that to provide maximum safety, the blade is not exposed
at any time, and the guard rises automatically as the blade is lowered.
Nevertheless, NEVER treat the machine with indifference, and NEVER be
casual with your approach.
To switch off, release the Trigger whilst still maintaining full control of the
head.
NOTE: The Head should rise under spring pressure, gently. If the movement
is too rapid or conversely, too sluggish, spring tension needs to be adjusted.
Refer to ‘Adjustments on page 16.
B. Mitre Cutting
This is a cross cutting operation,
except that the saw blade is set
at an angle to the work, but
remains perpendicular to the
table. The head is mounted on
the table which is free to rotate
by up to 45°, left and right.
To set the required mitre angle
unscrew the Table Lock Handle
and rotate the Table, with the
Head and saw blade, to the
desired position, lining up the
angle on the scale, with the
pointer shown in Fig. 3 on page
9. Lock the Table in position with
the Locking Handle.
The procedure for cutting is the
same as that for cross cutting.
For convenience, positive stops are provided at various angles. These are:
Zero (90°), 22.5° and 45°
Fig. 8
12
Summary of Contents for Woodworker CMS254
Page 1: ...OPERATING MAINTENANCE INSTRUCTIONS CMS254 COMPOUND MITRE SAW 0604...
Page 8: ...PRINCIPAL PARTS OF THE SAW Fig 1 82...
Page 18: ...PARTS DIAGRAM 18...
Page 21: ...23...