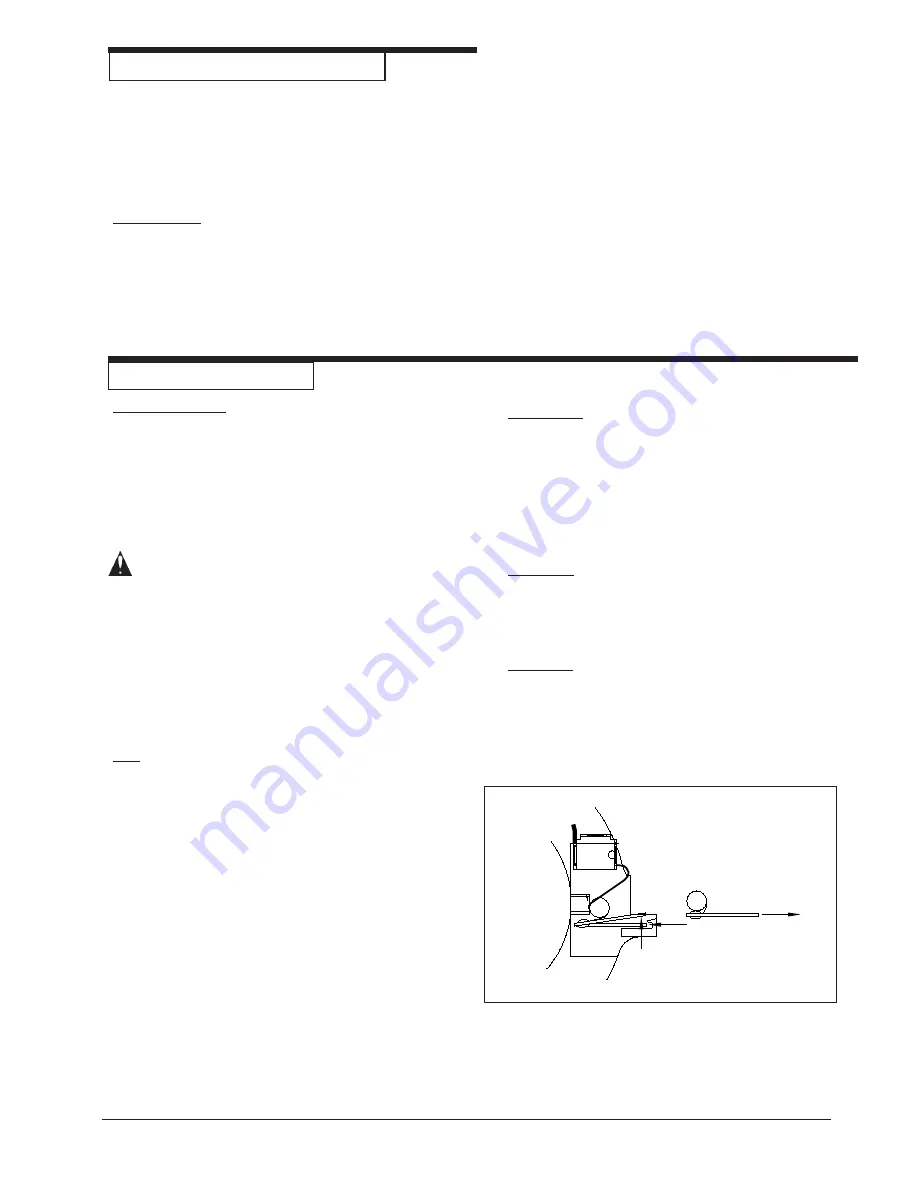
Clarke
®
American Sanders
Super E Operator's Manual
Page 9
ADJUSTMENT PROCEDURES (cont)
Condition - Pad creates a ridge on only one side of the
pad: Either rotate the stem of the side effected clock-
wise or rotate the stem opposite conterclockwise,
depending on whether the ridge terminates beyond the
tip of the pad or prior to it. If it is prior to the tip, adjust
the side effected, otherwise adjust the opposite side.
Belt Tension
The design of the belt allows it to deliver the power with
very little tenstion. The tension should be great
enough to prevent slippage and wear. Excessive
tension will only shorten bearing and belt life.
ROUTINE MAINTENANCE
Carbon Brushes
Inspect all four brushes every 6 months or 250 hours.
Access to the brushes is gained through the front and
back motor vent plugs and under both covers. Press
tab on spring clip assembly in, rotate, then remove
(figure 5). Use needlenose pliers to disconnect the
shunt wire. If any brush has worn to 3/8" in length or
shorter, replace the entire set.
CAUTION: Use only motor brush part no. 40818A
or 40055A with shunt wire or motor
failure will occur.
When replacing the brushes, make sure that the brush
seats against the commutator, the tab on the spring
clip assembly is fully seated in pocket, and the brush
is free to travel. When returning the switch covers,
keep all wires clear of the commutator and any pinch
sites.
Pad
In time the elastomer on the pad may wear or become
damaged. To replace, remove pad by placing screw-
driver in slot of shaft, grasp pad and rotate shaft
counterclockwise. Remove existing elastomer and
clean hub throughly to remove old adhesive. Roughen
surface of new elastomer to provide good bond sights.
Apply a good rubber cement to both surfaces and allow
to tack. 3M# 1300 rubber and gasket cement is a
suitable choice. Apply elastomer to hub and knead
throughly. Apply pressure to elastomer and allow to
stand over night. Apply a medium strength thread
locker to the external threaded end of the shaft. Install
belt in grooves on hub and screw down on shaft.
Install abrasive retainer on to shaft. Locate a flat
surface and tape 80 grit abrasive to surface. Using
machine "dress in" by sanding the elastomer on the
pad. Continue sanding until the entire surface of the
elastomer shows signs of sanding. As in operation of
the machine, take precautions performing this proce-
dure.
Pad Driver
Periodically inspect belt grooves on pad driver for an
accumulation of paint or varnish especially after jobs
where several layers of paint or varnish have been
removed. Particles of paint or varnish can deposit in
the grooves, creating vibration and damaging the
drive belt. Use a plastic putty knife or similar object to
remove the deposits.
Dust Bag
Periodically the dust bag should be turned inside out,
shaken vigorously and machine washed in cold water
to prevent pore blockage and loss of dust control.
Bearings
To insure reliable performance, armature and pad
driver bearings should be inspected for wear or
damage after 1500 hours. If used heavily the bear-
ings should be replaced seasonally.
Figure 5