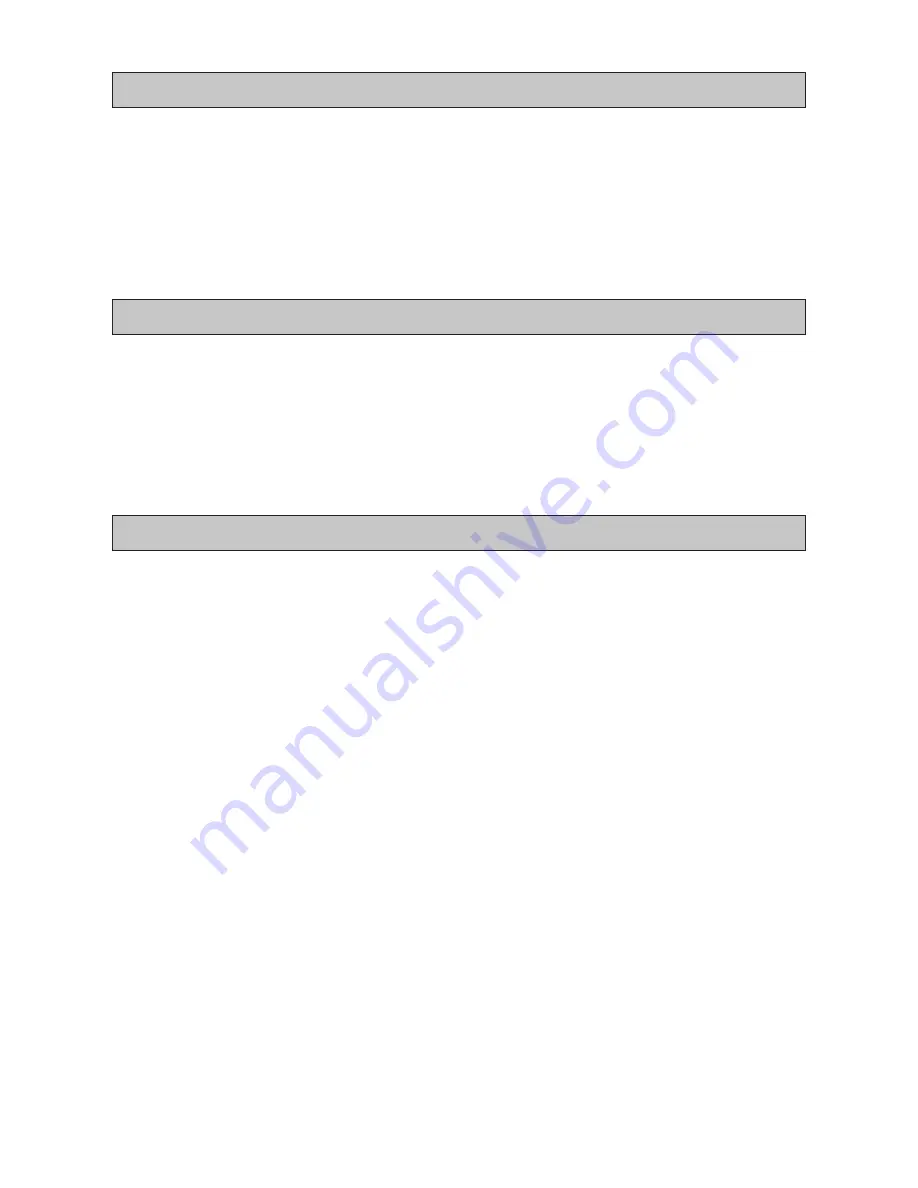
3
INTRODUCTION
Thank you for purchasing your CLARKE 20mm Drill Press.
Before attempting to operate the machine, please read this instruction manual
thoroughly, and follow all directions carefully. By doing so you will ensure the safety
of both yourself and others around you, and at the same time, you should look
forward to long and trouble free service from your Clarke Drill Press.
GUARANTEE
This product is guaranteed against faults in manufacture for 12 months from date
of purchase. Keep your receipt as proof of purchase. This guarantee is invalid if the
product has been found to have been abused or tampered with in any way, or
not used for the purpose for which it was intended. The reason for return must be
clearly stated. This guarantee does not affect your statutory rights.
TABLE OF CONTENTS
PAGE
Safety Precautions .......................................................................... 4
Additional Safety Rules for Drill Presses ......................................... 5
Electrical Connections and Wiring Diagram ................................ 6
Preparation for Use ......................................................................... 7
Description of Parts ......................................................................... 8
Assembly .......................................................................................... 9
Settings and Adjustments ............................................................. 11
Operation ....................................................................................... 13
Removing the Chuck .................................................................... 14
Maintenance ................................................................................. 14
Troubleshooting ............................................................................. 15
Parts Lists and Diagrams ........................................................ 16 - 20
Drill Speed Table ............................................................................ 21
Spare Parts & Servicing ................................................................. 21
Cutting Speed Chart ..................................................................... 22
Specifications ................................................................................ 23
Optional Accessories .................................................................... 23
Summary of Contents for Metalworker CDP501F
Page 1: ...1 SERIAL No 0307 ...
Page 17: ...17 HEAD ASSEMBLY ...