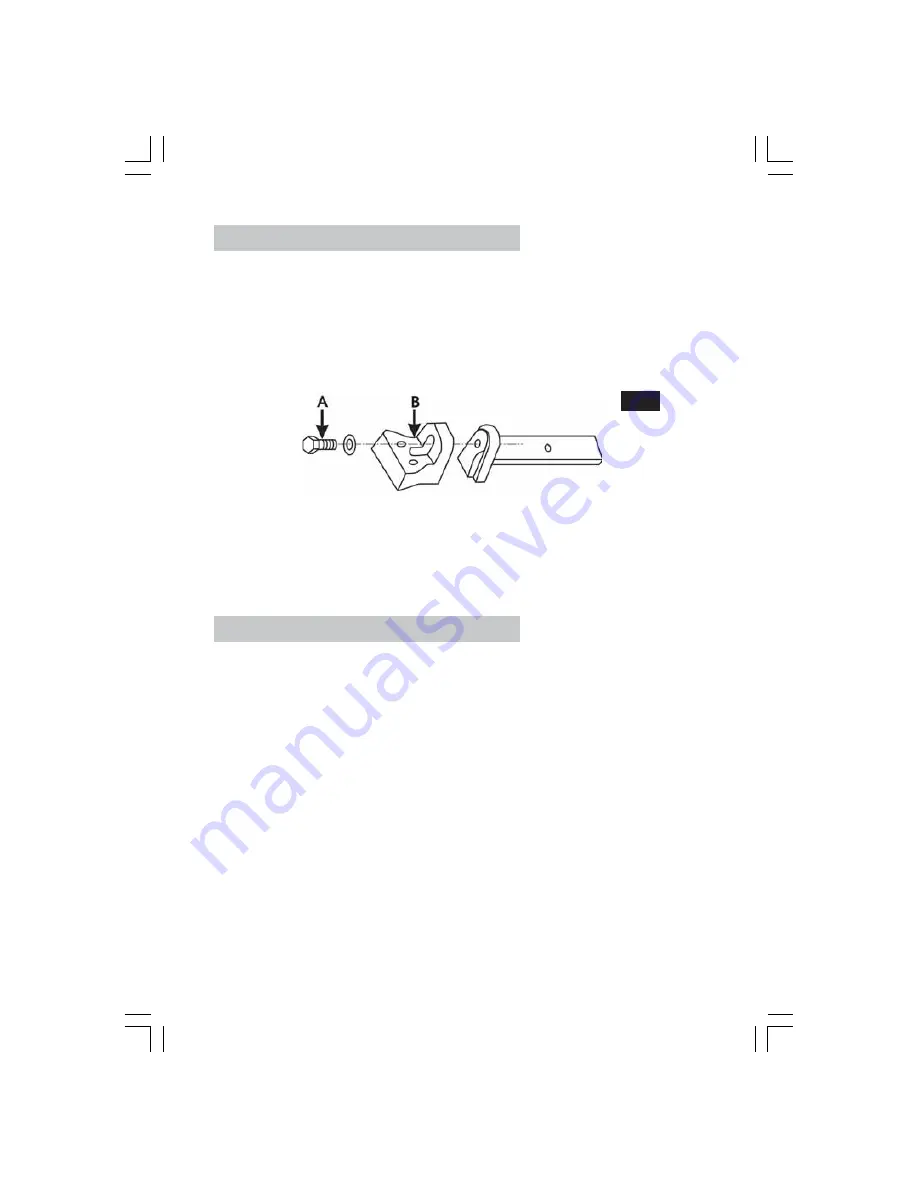
15
8. ADJUSTING BLADE ANGLE
Fig.4
When horizontal cutting, the blade must be at right angles (or vertical) to the
bed. To achieve this:
1.
Loosen the screw (A, Fig.4).
2.
Adjust the blade guide (B, Fig.4) to make the blade vertical to the bed.
3.
Place can engineers square on the bed to check the blade Is vertical, It not,
repeat the process. 1 to 3.
4.
Tighten the screw (11)
LUBRICATION
All bearings are lubricated for life. It is not necessary therefore to lubricate guide
bearings etc.
A thin film of oil on all unpainted surfaces will protect your saw and prevent
oxidation.
Lubricate all screw threads regularly, depending upon useage.
The drive gears run in an oil bath and will not require a lubricant change more
often than once a year.
When needing a change, first lower the arm to a horizontal position, then remove
the 4 screws securing the gearbox cover.
Open the cover (item 6).
Place a container under the right lower corner of the gear box, slowly raise the
head until the oil flows into the container.
Lower the head then wipe up excess oil and foreign matter with a soft rag, then
add Iubricant into the box until it is full. Close the cover, and tighten the 4 screws.