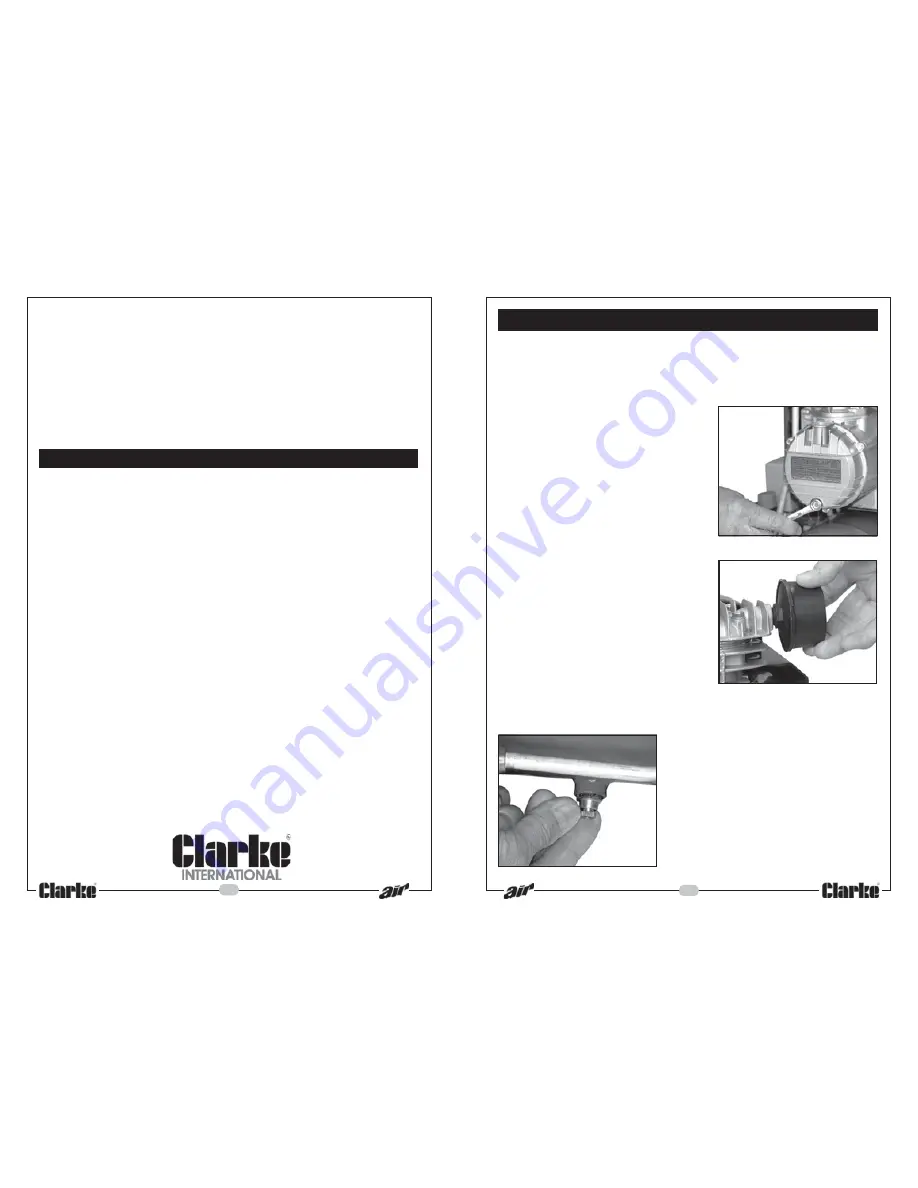
7.
The Pressure Switch should not require adjustment. This is an automatic device
and has been pre-set at the factory to stop the motor when the pressure in
the receiver reaches its maximum (115 psi), and to start it again when the
pressure in the receiver falls to the minimum precept value. This operation is
completely automatic and does not affect the spraying process in any way.
NOTE:
If the machine pumps continuously without cutting-out then the compressor
is too small for the application/tool being used, and damage to the
machine may result.
8
1.
Press the ON/OFF switch to the off ‘O’ position.
NEVER USE THE MAINS SWITCH TO STOP THE MOTOR.
2.
IMPORTANT!...... ALWAYS
depress equipment trigger (spraygun) to release air
from the hose and compressor
BEFORE
disconnecting from the machine.
3.
Switch off and disconnect from the mains supply.
SHUTTING DOWN THE COMPRESSOR
MAINTENANCE
Fig. 9
3.
After the first 50 hours use, replace the
oil completely (use Clarke SAE 40
compressor oil) and then, after every 100
hours. To empty the oil from the
machine, remove the screw on the front
of the crankcase cover (fig.7).
4.
Every 50 hours use, remove the black
plastic air filter (fig.8), then unclip the
back cover.
Remove the filter and wash it in clean
soapy water. Allow to dry completely
before reassembling. Renew the filter if
it is badly contaminated or damaged in
any way.
5)
At least once a week drain the
condensate from the receiver by
unscrewing the drain plug underneath
the air receiver (fig.9).
NOTE: If the compressor is used on a daily
basis, then the tank should be drained before
each use.
6)
In the event of an air leak follow the
procedure below:
•
Load compressor to maximum pressure
•
Unplug the compressor
•
With a brush and soapy water wet all
‘screwed’ connections
•
Any leaks will show through the
formation of air bubbles
NEVER UNSCREW A CONNECTION WHILE THE
RECEIVER TANK IS UNDER PRESSURE...ALWAYS
MAKE CERTAIN THAT THE TANK HAS FIRST
BEEN EMPTIED.
1.
After the first 5 hours of running the compressor, check the cylinder head bolts
and motor housing, screws and re-tighten if any have worked loose.
2.
Check the oil level every time you start working and top-up if necessary (use
Clarke SAE 40 compressor oil).
Fig. 7
Fig.8
9