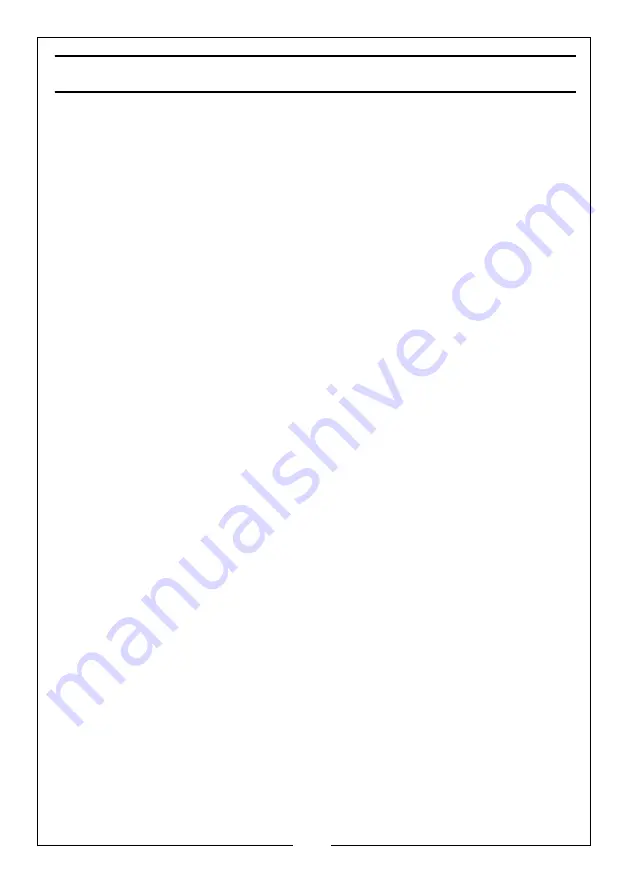
7
Parts & Service: 020 8988 7400 / E-mail: [email protected] or [email protected]
MAINTENANCE
A visual inspection must be made before each use of the press, checking for
leaking hydraulic fluid, and damaged, loose or missing parts.
Owners and/or users should be aware that repair of this equipment may
require specialised knowledge and facilities. It is recommended that a
thorough annual inspection of the press be made and that any defective
parts, decals or warning labels be replaced with genuine Clarke parts.
Any press which appears to be damaged in any way, is found to be badly
worn, or operates abnormally SHOULD BE REMOVED FROM SERVICE until the
necessary repairs are made.
PERIODICALLY
• Check the press frame to make sure all bolts are tight and inspect for
cracked welds, bent, loose or missing parts.
• Check the hydraulic connections for leaks. Replace or properly repair any
damaged or leaking hydraulic components before using.
EVERY 6 MONTHS
• Check the hydraulic pump oil level, by removing the plug from the front of
the unit. Oil should be level with the bottom of the hole. If necessary top up
with CLARKE Hydraulic Oil, Part No. 3050830 only.
This operation is carried out
with the ram fully retracted.
EVERY 2 YEARS
• Replace the hydraulic oil. This operation requires the dismantling of the
hydraulic system, for which you should consult your CLARKE dealer.
• If any rust is apparent it must be removed completely and reinspected.
Summary of Contents for 7615115
Page 12: ......