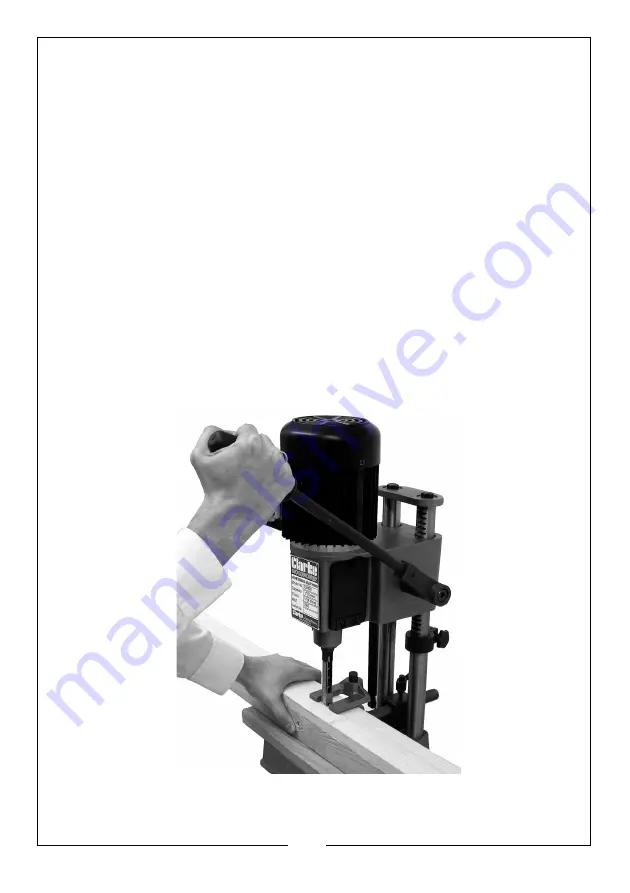
17
Parts & Service: 020 8988 7400 / E-mail: [email protected] or [email protected]
• A dull chisel can be detected by the amount of excess force
required to complete a cut.
• After the first cut, the workpiece must be moved along in the correct
direction relative to the slot in the chisel, to allow chips to clear
freely. Move the workpiece so that the chisel slot is releasing chips
into the already cut part of the mortice.
• Do not have the slot against the blind end of the mortice, as the
chips will not be able to clear from the chisel. This will cause
overheating and possible breakage to the chisel or bit.
• When cutting deep mortises, make the cut in several stages of
approximately 25mm each, to allow chips to clear.
• When performing a through mortice, a piece of wood should be
placed between the workpiece and the table. This prevents the
wood from splintering when breaking through the bottom of the
mortise and also prevents damage to the table.
• Always switch the morticing machine off after use. Never leave the
machine running unattended.
Summary of Contents for 6500015
Page 24: ......