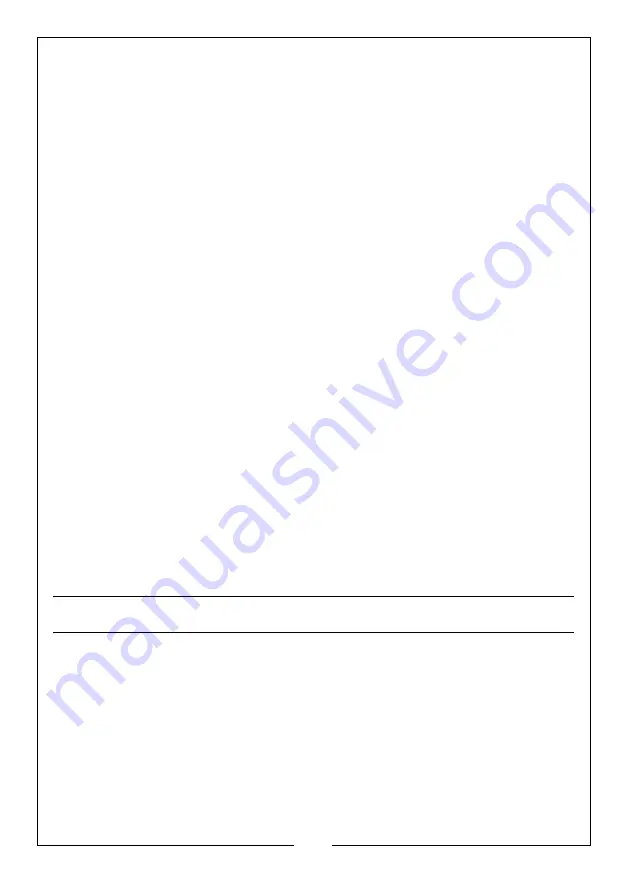
10
Parts & Service: 020 8988 7400 / E-mail: [email protected] or [email protected]
2. After drilling material to the full depth, do not simply pull out the drill but
maintain chuck rotation to ease withdrawal.
3. Reduce the pressure on the drill bit when it is about to break through. This
will prevent the drill from jamming.
4. If drilling a large hole, first drill a pilot hole using a smaller drill bit.
5. Always apply pressure to your drill bit in a straight line and, where possible,
at right angles to the workpiece.
6. When drilling holes or driving screws into walls, floors etc., always make sure
that there are no live electrical wires in the path of the bit.
7. When drilling in metal, the materials being drilled can become hot. To
reduce overheating use a suitable cooling lubricant. No cooling lubricant is
necessary when drilling cast iron or brass as they should be drilled dry.
8. When drilling metal, the harder the metal the slower the drill speed.
Similarly, the bigger the drill bit the slower the speed.
9. Always start drilling at a slow speed to prevent the drill from slipping out of
the pop mark or indent, gradually increasing speed until the optimum
cutting speed is achieved whilst maintaining a MODERATE pressure ONLY.
NEVER force the drill bit into the work. This will overheat the tip and cause it
to dull very quickly.
10. To prevent the drill bit from slipping when starting to drill a hole in metal, use
a centre punch to make an indentation at the start point.
11. When drilling in wood, clamp a piece of scrap wood to the underside of
the material to avoid splintering.
12. Always drill directly in line with the bit. Do not use sideways movement as
this may damage the drill or cause the bit to break.
13. Large holes should be drilled with wood augers, flat wood bits or hole saws.
MAINTENANCE AND SERVICING
1. After use, remove the drill or screwdriver bit, open the chuck jaws and tap
the side of the chuck to remove any dust, or chippings etc.
2. Keep the cooling vents clear.
3. Keep the handle clean and free from oil and grease.
4. Worn or damaged parts must be replaced by qualified personnel.
5. Clean the tool regularly, use a soft brush and or soft cleaning cloth. DO
NOT use any chemicals or harsh abrasives to clean the tool.
Summary of Contents for 6482015
Page 17: ......