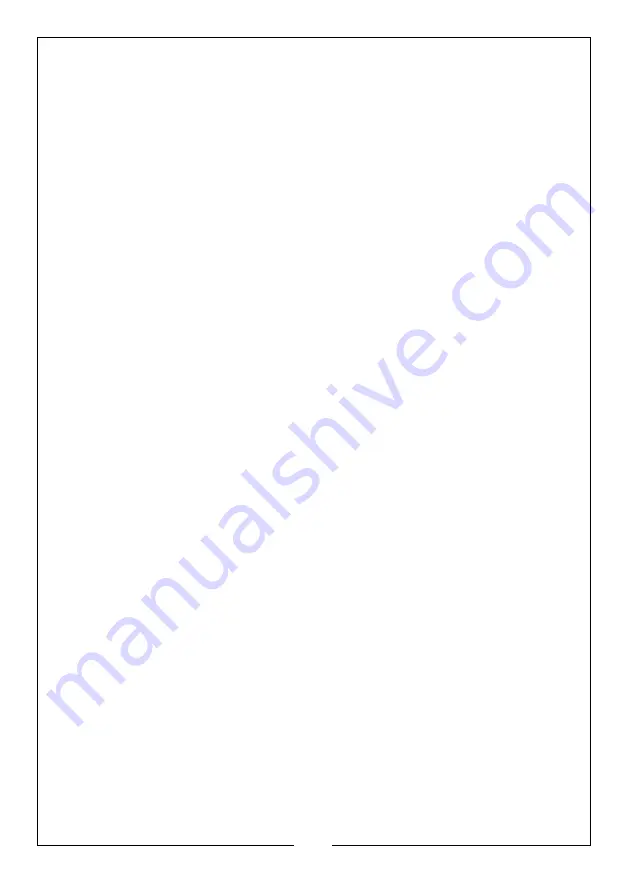
4
Parts & Service: 020 8988 7400 / E-mail: [email protected] or [email protected]
perchloroethylene vapours to form phosgene. DO NOT WELD where solvent
vapours can be drawn into the welding atmosphere or where the radiant
energy can penetrate to atmospheres containing even minute amounts of
trichloroethylene or perchloroethylene.
FIRE AND EXPLOSION PREVENTION
Causes of fire and explosion are:
1. Combustibles reached by the arc, flying sparks, hot slag or heated
material;
2. Short circuits.
BE AWARE that flying sparks or falling slag can pass through cracks, along
pipes, through windows or doors, and through wall or floor openings, out of
sight of the goggled operator.
To prevent fires and explosion: keep equipment clean and operable, free of
oil, grease, and (in electrical parts) of metallic particles that can cause short
circuits. If combustibles are in the area, do NOT weld. Move the work if
practicable, to an area free of combustibles.
Avoid working in paint spray rooms, dip tanks, storage areas, ventilators. If the
work cannot be moved, move combustibles away from sparks and heat; or
protect against ignition with suitable fire- resistant covers or shields.
Walls, ceilings, and floor near work should be protected by heat resistant
covers or shields. Fire watcher must be standing by with suitable fire
extinguishing equipment during and for some time after welding or cutting if:
1. appreciable combustibles (including building construction) are within 10m.
2. appreciable combustibles are further than 10m, but can be ignited by
sparks.
3. openings (concealed or visible) in floors or walls can expose combustibles
to sparks.
4. combustibles adjacent to walls, ceilings, roofs or metal partitions can be
ignited by radiant or conducted heat.
After work, check that area is free of sparks, glowing embers and flames. An
empty container that held combustibles or that can produce flammable or
toxic vapours when heated, must never be welded on or cut, unless the
container has first been cleaned. This includes a thorough steam or caustic
cleaning (or a solvent or water washing, depending on the combustible’s
solubility) followed by purging and inerting with nitrogen or carbon dioxide,
and using protective equipment.
Water filling just below the working level may substitute for inerting.
A container with unknown contents should be cleaned (see paragraph
above). Do NOT depend on sense of smell or sight to determine if it is safe to
Summary of Contents for 6012163
Page 24: ......