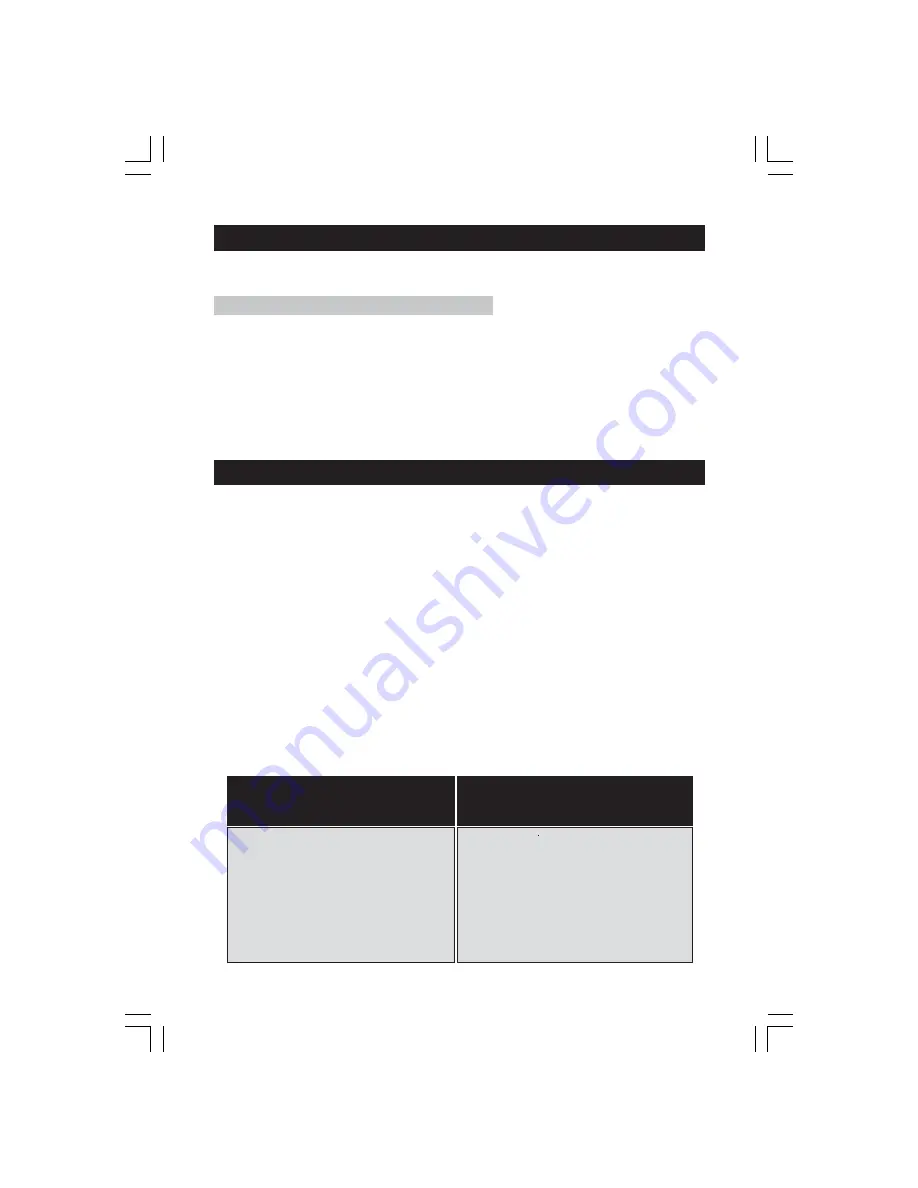
FEATURES
The welding capabilities of your welder are given on the data label printed on the rear
panel of the machine (see list on page 22 for an explanation of markings and symbols).
Thermal Overload Protection
If the duty cycle of the welder is exceeded (see Specifications), the
Overload
Protection Device
will automatically cut the power to prevent damage to the
machine. Should the cut-out operate, the amber light on the front panel will illuminate,
and you will have to wait until the transformer cools down (approx. 30 minutes),
when the overload device will automatically reset itself and you can continue
welding. (On smaller welders the lamp is built in to the ON/OFF switch).
Although no harm will be done to the machine if/when the overload device is
actuated, its frequent use could eventually result in damage.
PREPARATION FOR WELDING
1. With the machine correctly connected to the mains supply in accordance
with the instructions given under ‘Electrical Connections’, attach the leads to
the machine as shown in Fig.1 on page 14.
Ensure the EARTH lead is connected to the WORKPIECE, and the other lead to
the ELECTRODE HOLDER.
IMPORTANT: Ensure also that the earth clamp is attached to clean, solid metal.
If necessary thoroughly clean with a wire brush or similar to guarantee a
good connection.
2. Select the appropriate electrode, which should be approximately the same
thickness as the piece to be welded, for single pass welding.
3. Select the appropriate welding current by turning the handwheel (H) and
observing the setting on the scale (J), on top of the machine.
NOTE: With practice you will get a feel for the best current settings for different
welding rod thicknesses.
The chart below is an indicator of the thickness of material/ welding rod thickness
and the corresponding welding current. This is intended as a guide only.
14
SIZE OF WELDING ROD
THICKNESS OF METAL
AMPERAGE SETTING
1/l6 16 swg
1.5 mm
40-55
14 swg
2.0 mm
50-70
12 swg
2.5 mm
75-95
1/8 10 swg
3.25mm
100-140
4.0 mm
140-180
5.0 mm
100-240
6.0 mm
240-250