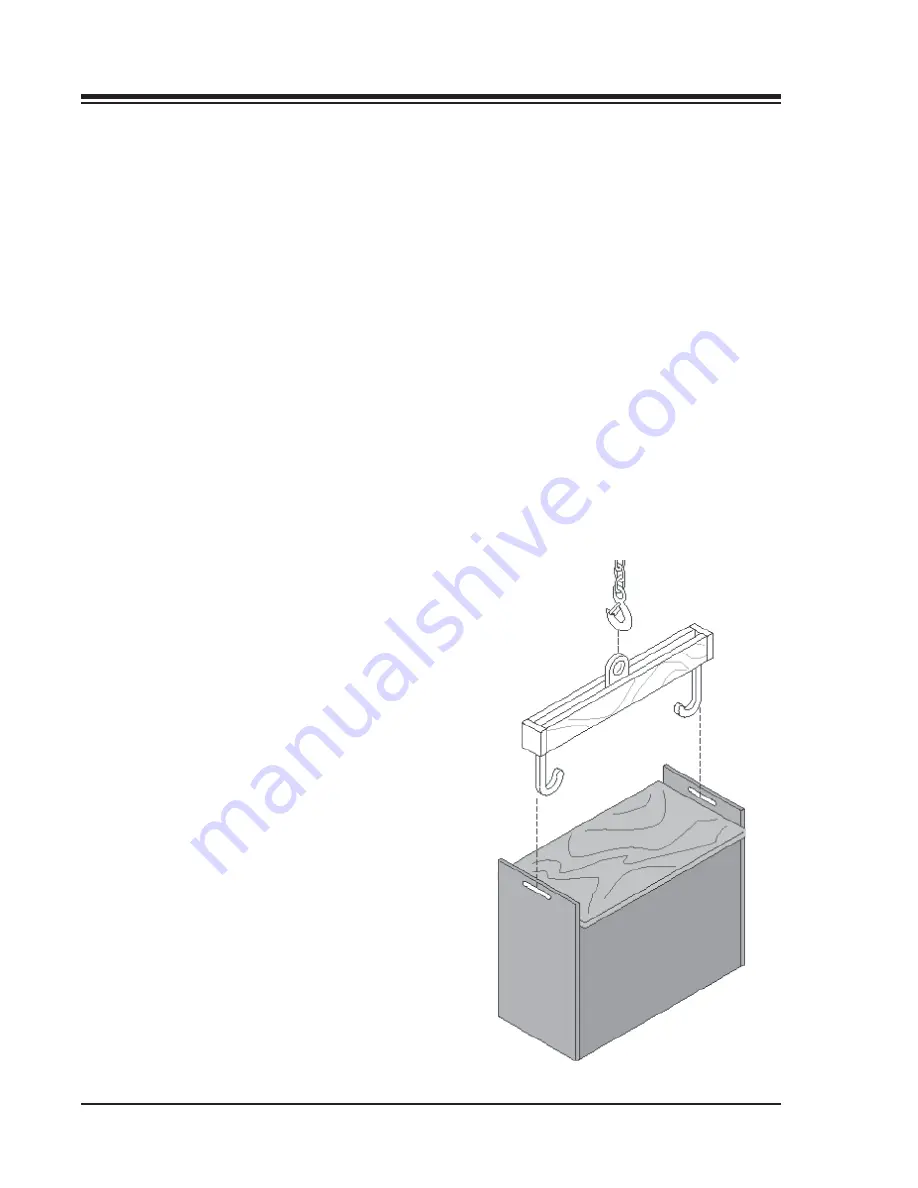
6.9
Battery Handling
1. Change (remove) or service storage batteries only in an area des-
ignated for this purpose.
2. Be sure this area has provisions to fl ush and neutralize spillage,
to ventilate fumes from gassing batteries, and for fi re protection.
3. This area should be equipped with material handling tools de-
signed for removing and replacing batteries, including a conveyor
or overhead hoist. Use lift hooks that have safety latches.
4. Always use a special lifting device such as an insulted spreader
bar to attach the hoist to the battery. The width of the spreader
bar must be the same as the lifting eyes of the battery, to prevent
damage to the battery. If the spreader bar hooks are movable,
carefully adjust the position (width) of the hooks so that the pull is
directly upward (vertical) and no side load or force (pressure) is
exerted on the battery case. Be sure the lift hooks are the correct
size to fi t the lifting eyes of the battery.
5. If the battery does not have
a cover of its own or has ex-
posed terminals and con-
nectors, cover the top with a
non-conductive (insulating)
material, such as a sheet of
plywood or heavy cardboard,
prior to attaching the lifting de-
vice.
Summary of Contents for HWX 30-40
Page 1: ...OM 746 Do not remove this manual from the truck Operator s Manual PWX 30 40 HWX 30 40 ...
Page 6: ...iv ...
Page 22: ...1 10 General Safety Rules ...
Page 50: ...4 10 ...
Page 58: ...5 8 ...
Page 72: ...6 14 ...
Page 74: ...7 2 ...
Page 76: ...8 2 ...