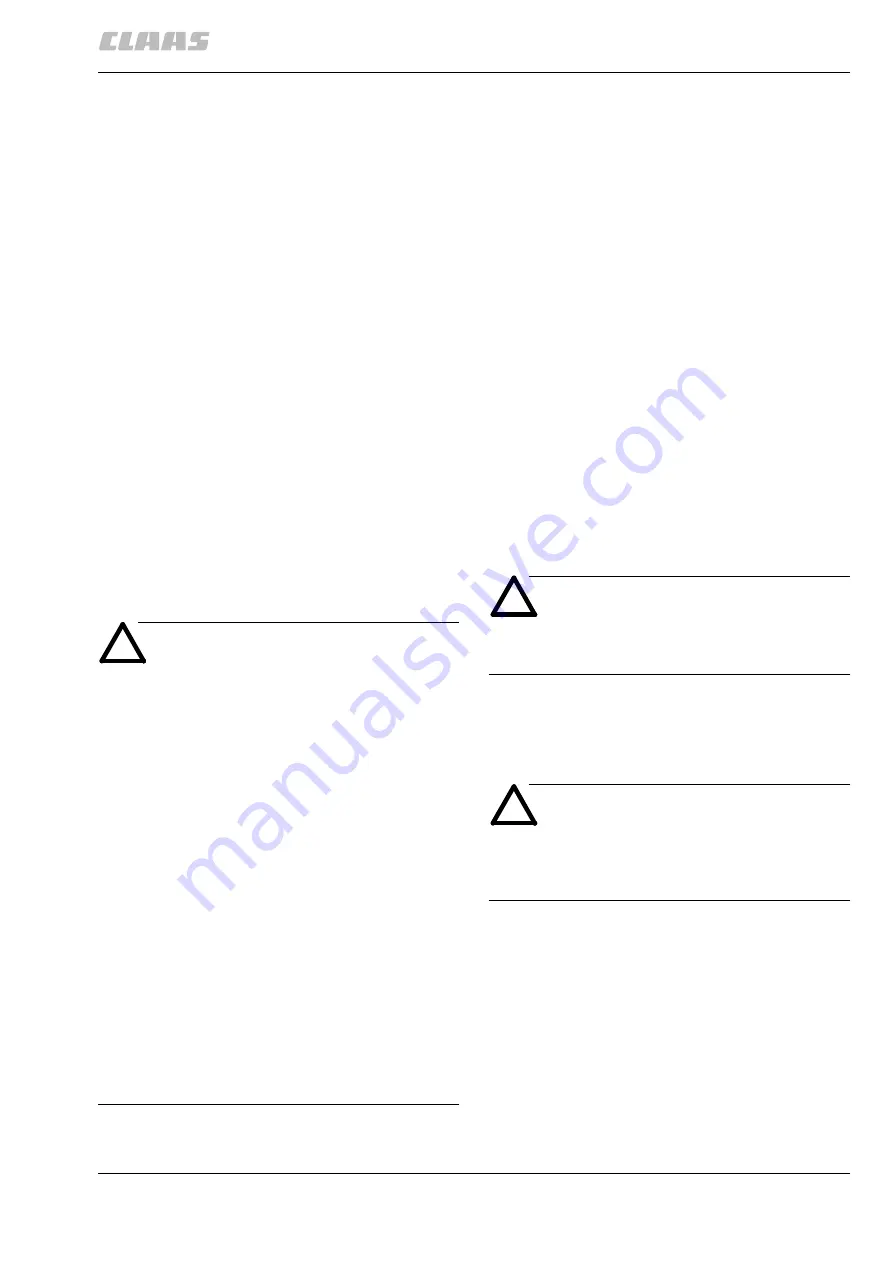
1.3.1
General repair information
GENERAL REPAIR INFORMATION
Reason of damage
Identify reason of damage, limit the case of damage
and safeguard the machine.
Spare parts
Use genuine CLAAS spare parts and corresponding
CLAAS special tools.
Indicate the machine number of the CLAAS combine
and when the engine, front attachments, maize
header, cutterbar and maize picker are concerned,
also the respective serial numbers when ordering
spare parts and in case of technical questions. This is
necessary as otherwise, incorrect spare part deliveries
may result.
Engine
Always disconnect the battery cable (–) prior to
starting work on the engine.
Gearboxes
When removing the gearboxes, first drain the oil and
then remove the gearbox. Separate parts which are
firmly connected with each other by means of a soft
metal-tip or plastic-tip hammer.
Alternator
ATTENTION!
– Never disconnect the cables connecting the
controller, alternator and battery whilst the
alternator is running.
– Ensure correct polarity when connecting the
cables to the battery as otherwise the diodes will
be burnt out.
– Do not carry out any work on live parts unless
the engine is stopped and the battery cables are
disconnected.
– The normal practice of striking a cable against
earth to check for current is not permitted with
alternators. This will damage the semiconductors.
– Before doing any electric welding on the combine,
be sure to disconnect the cables from the
alternator terminals!
– The battery provides the current for the field
excitation required to start the alternator via the
battery charge indicator bulb. Blown bulbs must
therefore be replaced to ensure reliable field
excitation.
Tensioning the steel roller chains
Find the centre point in the slack span between
sprockets. With the tight span slightly under load, push
in the centre point of the slack span with the thumb.
The chain tension is correct when its slack span
deflects about 2 % of the centre distance between
shafts. Check chain tension more frequently when
using new chains.
Example: For a distance between centres of shafts of
500 mm, the slack span of the chain should deflect
about 10 mm.
Taper ring fasteners
Taper ring fasteners provide a safe mechanical
connection, even when transmitting high forces from
the driving element on the shaft and vice versa, if they
are properly prestressed.
Installation:
When installing taper ring fasteners, it is important that
the shaft, hub, parallel key and the taper rings have
been thoroughly cleaned, that semi-fluid lubricant of
NLGI class 00 (e.g. CLAAS semi-fluid lubricant EP 00)
is applied and that the components are tightened to
the specified torque in the correct order of assembly.
ATTENTION!
No
solid grease must be used when
assembling the parts.
Removal:
After loosening the axial clamping, loosen the taper
ring fasteners with a sharp blow, using a block-ended
tube.
ATTENTION!
The inside diameter of the block-ended tube
must be large enough to extend over the
tapered ring.
Self-locking bolts
(with microencapsulated adhesive)
Replace self-locking bolts, e.g. Verbus-Plus /
Imbus-Plus and similar types every time such bolts are
removed. In exceptional cases, they may be reused up
to three times. Always observe the specified tightening
torque.
Summary of Contents for LEXION 480
Page 1: ...REPAIR MANUAL LEXION 480...
Page 2: ...R e a d a n d f o l l o w s a f e t y i n s t r u c t i o n s...
Page 14: ...0 1 12 RHB LEXION 480 188 678 1 Contents...
Page 15: ...1 General information...
Page 16: ......
Page 20: ...1 1 4 RHB LEXION 480 188 678 1 General...
Page 24: ...1 2 4 RHB LEXION 480 188 678 1 Safety Rules...
Page 38: ...1 6 4 RHB LEXION 480 188 678 1 Sectional view of machine...
Page 41: ...2 Operator s platform...
Page 42: ......
Page 74: ...2 1 32 RHB LEXION 480 188 678 1 Air conditioner...
Page 98: ...2 5 2 RHB LEXION 480 188 678 1 Engine electric system...
Page 99: ...3 Threshing mechanism...
Page 100: ......
Page 138: ...3 1 38 RHB LEXION 480 188 678 1 Feed rake conveyor...
Page 238: ...3 6 24 RHB LEXION 480 188 678 1 Axial rotors...
Page 239: ...4 Cleaning unit...
Page 240: ......
Page 246: ...4 1 6 RHB LEXION 480 188 678 1 Return pan...
Page 295: ...5 Grain delivery...
Page 296: ......
Page 373: ...6 Straw discharge...
Page 374: ......
Page 390: ...6 1 16 RHB LEXION 480 188 678 1 Straw chopper...
Page 397: ...188 678 1 RHB LEXION 480 6 2 7 Uni spreader 23...
Page 402: ...6 2 12 RHB LEXION 480 188 678 1 Uni spreader...
Page 403: ...7 Drives...
Page 404: ......
Page 408: ...7 1 4 RHB LEXION 480 188 678 1 Drive diagram...
Page 444: ...7 2 36 RHB LEXION 480 188 678 1 Left hand drive belts...
Page 542: ...7 4 66 RHB LEXION 480 188 678 1 Cutterbar drive...
Page 556: ...7 5 14 RHB LEXION 480 188 678 1 Left hand threshing mechanism drive...
Page 580: ...7 6 24 RHB LEXION 480 188 678 1 Right hand threshing mechanism drive...
Page 594: ...7 7 14 RHB LEXION 480 188 678 1 Threshing drum reduction gearbox...
Page 634: ...7 11 12 RHB LEXION 480 188 678 1 Straw spreader drive...
Page 644: ...7 13 8 RHB LEXION 480 188 678 1 Sieve pan drive...
Page 708: ...7 15 22 RHB LEXION 480 188 678 1 Axial rotor drive...
Page 730: ...7 16 22 RHB LEXION 480 188 678 1 Engine output...
Page 736: ...7 17 6 RHB LEXION 480 188 678 1 Rotary screen drive...
Page 766: ...7 18 30 RHB LEXION 480 188 678 1 Final drives...
Page 818: ...7 21 20 RHB LEXION 480 188 678 1 Steering axle...
Page 819: ...8 Machine body...
Page 820: ......
Page 839: ...9 Hydraulic system...
Page 840: ......
Page 848: ...9 2 4 RHB LEXION 480 188 678 1 Maintenance...
Page 866: ...9 4 10 RHB LEXION 480 188 678 1 Hydrostatic fixed displacement motors...
Page 902: ...9 5 36 RHB LEXION 480 188 678 1 Hydraulic cylinders High pressure hydraulic circuit...
Page 981: ...10 Engine...
Page 982: ......
Page 1003: ...11 Index...
Page 1004: ......
Page 1016: ...11 1 12 RHB LEXION 480 188 678 1 Index...