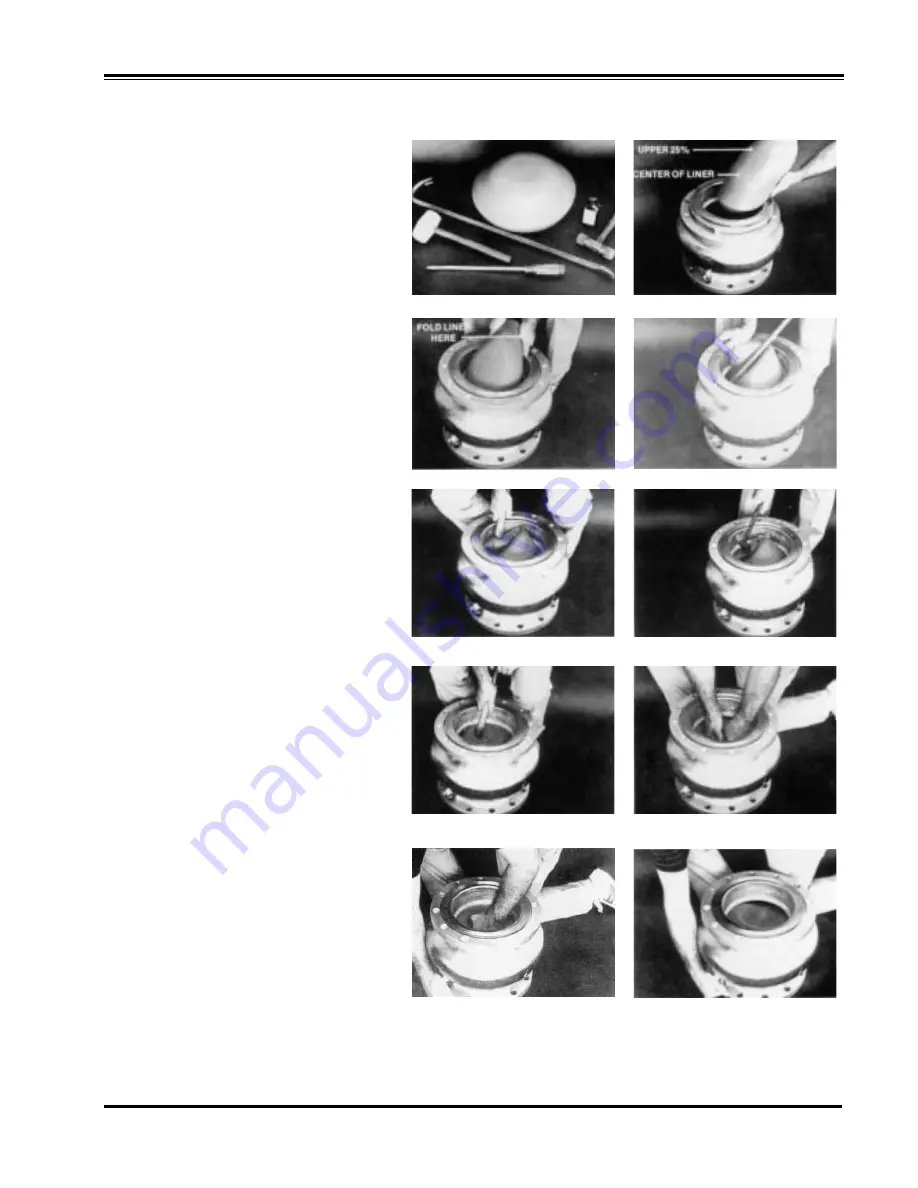
Liner Installation
6", 8", 10", 12" sizes
1. Tools required: Bottle of drugstore glycerine,
30" crowbar, double headed plastic hammer
with 14" handle, rubber mallet and large flat
blade screwdriver.
2. Liberally wipe glycerine on the inside of the
valve and on the outer edge of the liner. Fold
liner in half and insert into valve body.
3. Push liner in as far as possible forcing it out side
ways.
4. Place the crowbar at the upper 25% point of the
liner. Take your other hand and push on nose of liner
to bend the liner over the crowbar. The less material
folded over, the easier it will go into the valve. If too
much is folded over, it will be difficult to complete
liner installation.
5. Continue bending liner nose down into the valve.
Use your hands and/or hammer handle to continue
forcing it down into valve. It is important to keep the
"V" of the bend near the 25% point. If it goes over
the center, The liner won't go in, and it will be nec-
essary to start over at Step 3.
6. Use the hammer to force the liner down and out into
the valve body.
7. Use the hammer handle for the final insertion.
Sometimes it is helpful to beat on the liner with the
hammer for the final step.
8. To seat the liner on the manifold ring use the ham-
mer handle to push down on the liner near bore of
valve inlet and pry handle and liner towards the cen-
ter. Continue this prying action for 360° around the
liner for proper seating.
9. To test for liner seating, push down on the center of
liner and close the loading port shut-off cock, or
block it with your hand. When you release your hand
from the liner, it should remain in the down position
until the loading port is opened.
10. If liner appears seated, open loading port cock and
liner should pop-up to the closed position. Repeat
Steps 6-10 if liner is not seated.
When the liner is fully seated, the inside diameter of
the liner will be seated over the outside diameter of
the manifold ring. The manifold ring is a raised circu-
lar ridge at the bottom of the open cavity which pro-
vides for even distribution of the fluid coming in and
going out the loading port.
Install liner retainer into body.
1
3
5
7
9
2
4
6
8
10
Distributed By: M&M Control Service, Inc.
http://www.mmcontrol.com/claval-index.php
800-876-0036 847-356-0566