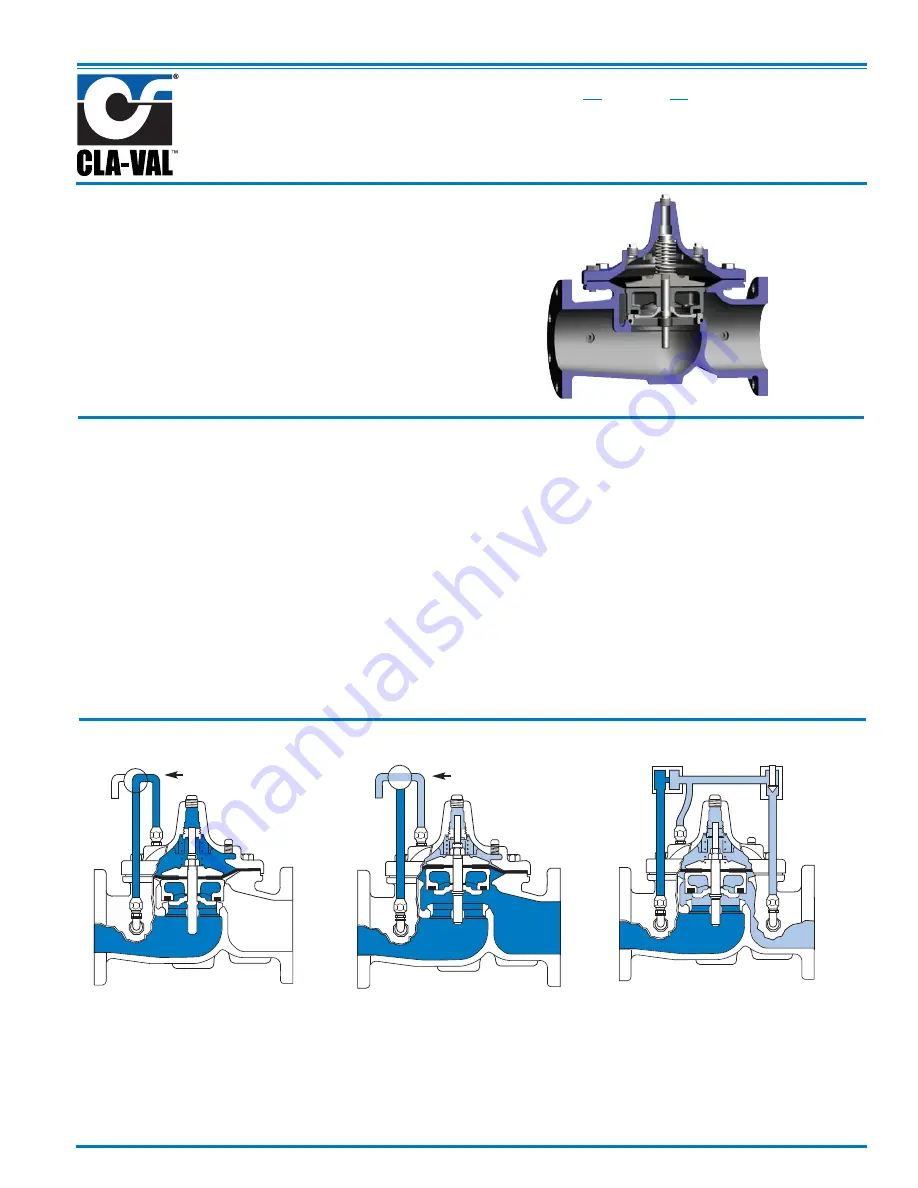
Description
The CIa-VaI Model 100-01 Hytrol Valve is a main valve for CIa-VaI
Automatic Control Valves. It is a hydraulically operated, diaphragm-actu-
ated, globe or angle pattern valve.
This valve consists of three major components; body, diaphragm assem-
bly, and cover. The diaphragm assembly is the only moving part. The
diaphragm assembly uses a diaphragm of nylon fabric bonded with syn-
thetic rubber. A synthetic rubber disc, contained on three and one half
sides by a disc retainer and disc guide, forms a seal with the valve seat
when pressure is applied above the diaphragm. The diaphragm assem-
bly forms a sealed chamber in the upper portion of the valve, separating
operating pressure from line pressure.
Installation
1. Before valve is installed, pipe lines should be flushed of all chips,
scale and foreign matter.
2. It is recommended that either gate or block valves be installed on
both ends of the 100-01 Hytrol Valve to facilitate isoIating the valve for
preventive maintenance and repairs.
3. Place the valve in the line with flow through the valve in the direc-
tion indicated on the inlet nameplate. (See “Flow Direction” Section)
Note: Valve can be installed in the vertical or horizontal position.
4. Allow sufficient room around valve to make adjustments and for dis-
assembly.
5. CIa-VaI 100-01 Hytrol Valves operate with maximum efficiency when
mounted in horizontal piping with the cover UP, however, other posi-
tions are acceptable. Due to size and weight of the cover and internal
components of 8 inch and larger valves, installation with the cover UP
is advisable. This makes internal parts readily accessible for periodic
inspection.
6. Caution must be taken in the installation of this valve to
insure that galvanic and/or electrolytic action does not take
place. The proper use of dielectric fittings and gaskets are
required in all systems using dissimilar metals.
7. If a pilot control system is installed on the 100-01 Hytrol
Valve, use care to prevent damage. If it is necessary to
remove fittings or components, be sure they are kept clean
and replaced exactly as they were.
8. After the valve is installed and the system is first pressur-
ized, vent air from the cover chamber and pilot system tub-
ing by loosening fittings at all high points.
Tight Closing Operation
When pressure from the valve inlet (or
an equivalent independent operating
pressure) is applied to the diaphragm
chamber the valve closes drip-tight.
Full Open Operation
When pressure in diaphragm chamber
is relieved to a zone of lower pressure
(usually atmosphere) the line pressure
(5 psi Min.) at the valve inlet opens the
valve.
Modulating Action
Valve modulates when diaphragm pres-
sure is held at an intermediate point
between inlet and discharge pressure.
With the use of a Cla-Val. "modulating
control," which reacts to line pressure
changes, the pressure above the
diaphragm is varied, allowing the valve
to throttle and compensate for the
change.
Principles of Operation
Three Way
Pilot Control
Three Way
Pilot Control
Restriction
Modulating
Control
100-01
Hytrol Valve
MODEL
INSTALLATION / OPERATION / MAINTENANCE