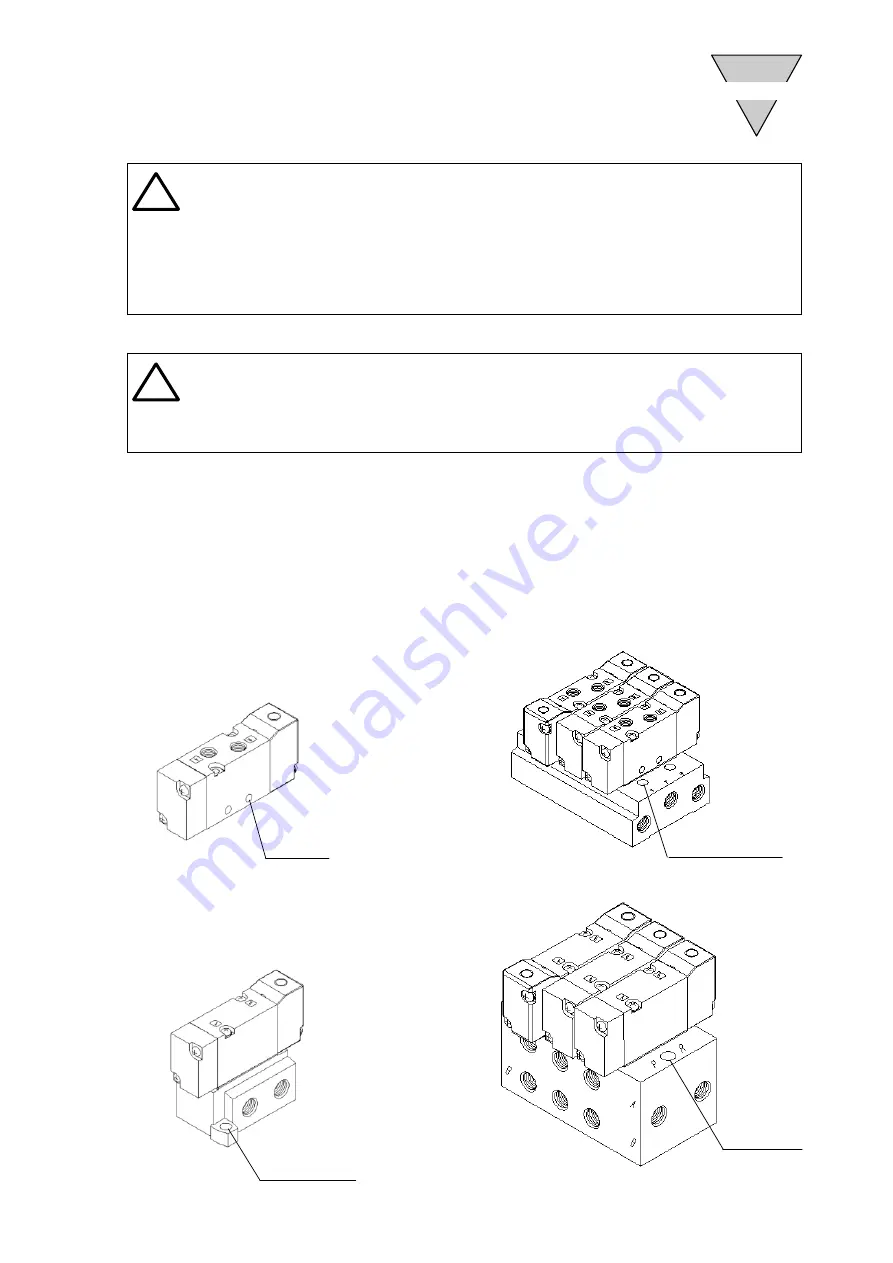
[SM-206792-A/3]
−
12
−
INSTALLATION
4
2-
φ
3.2
f) The packing and gaskets may deteriorate sooner than
usual if used in an atmosphere with a higher than
normal density of ozone (for example, the atmosphere
near a beach or in an area with frequent thunder-
storms).
Consult us for the packing and gaskets to be used in an
atmosphere with a higher ozone density.
4.2 Installation
When installing a master valve unit, never attempt to hold
it in position by means of the pipes connected to it.
Mount the master valve by applying the mounting screws
and/or mounting plate to the master valve.
4.2.1 A work space for installation, removal, wiring, and piping opera-
tions should be provided around the installed master valve sys-
tem.
4.2.2 Direct mounting
1) Direct piping Type
Use two or four through holes
unit
manifold
2) Sub plate piping Type
Use two mounting holes
unit manifold
!
WARNING :
!
CAUTION :
4-
φ
4.5
2-
φ
4.5
2-
φ
5.5