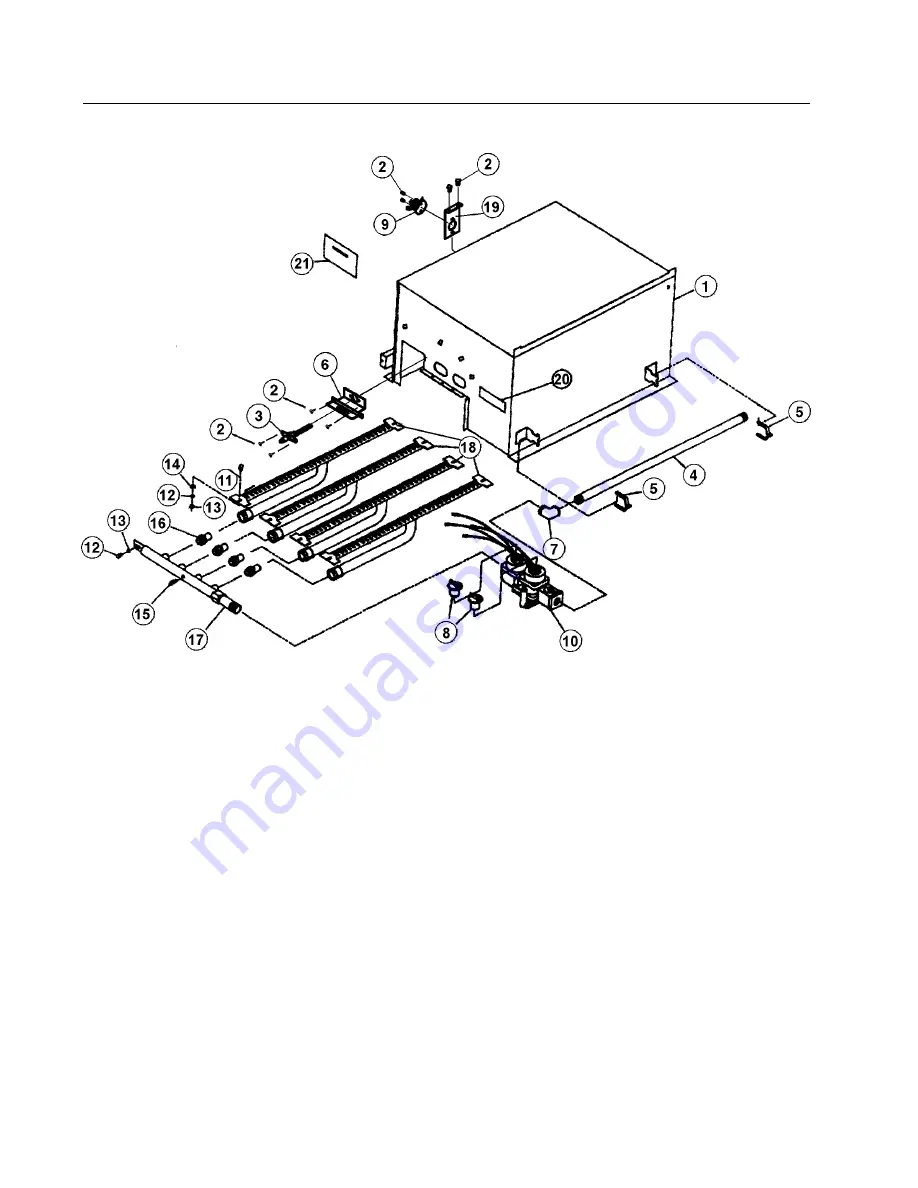
Page 70
Parts—Standard Gas Bonnet
1
TU8683
Bonnet
2
TU7733
#8 - 18 x 1/2" Self Drill Screw
(Pkg. of 6)
3
GA-00764-0
Electrode Spark Igniter
4
TU13212
1/2" Pipe Nipple 24"
5
TU2226
Manifold Mounting Bracket
6
TU13826
Electrode Spark Mounting
Bracket
7
OP291
1/2" Elbow (Street)
8
C1365
Connector T & B
9
TU13678
Thermostat, Man. Reset 300°
10 TU13523
1/2" Combination Gas Valve
(Natural Gas)
TU13513
1/2" Combination Gas Valve
(LP Gas)
11
CB36
1/2" - 20 x 1/2" Hex Head Screw
12
TU2846
1/4" Split Lockwasher
13
TU4934
1/4" - 20 Hex Nut
14
TU2847
1/4" Flat Washer
15
TU2224
1/8" Pipe Plug
16
TU3539
Gas Burner Orifice
(Specify Size)
17
TU8288
Manifold Assembly
18
TU7840
Burner
19
TU13695
Bonnet Thermostat Bracket
20
TU8645
Installation Instructions
21
---------
Spark Ignition Instructions
GAS BONNET ASSEMBLY - TU13675 (Natural Gas) DSI
GAS BONNET ASSEMBLY - TU13716 (LP Gas) DSI
Summary of Contents for L36URD30E
Page 11: ...Page 11 50 lb Dryer Dimensions Standard Gas Steam and Electric Heated Illustration ...
Page 12: ...Page 12 50 lb Dryer Dimensions Gas Energy Saver Model Illustration ...
Page 24: ...Page 24 Steam Piping Installation Illustration ...
Page 36: ...Page 36 Double Timer Models Illustration Double Timer Panel ...
Page 43: ...Page 43 DIRECTSPARK IGNITIONOPERATION FLOW CHART ...
Page 58: ...Page 58 50 lb Laundry Dryer Front Exploded View Illustration ...
Page 60: ...Page 60 50 lb Laundry Dryer Single Motor Model Rear View Illustration ...
Page 62: ...Page 62 50 lb Laundry Dryer Double Motor Model Rear View Illustration ...
Page 76: ...Page 76 ...