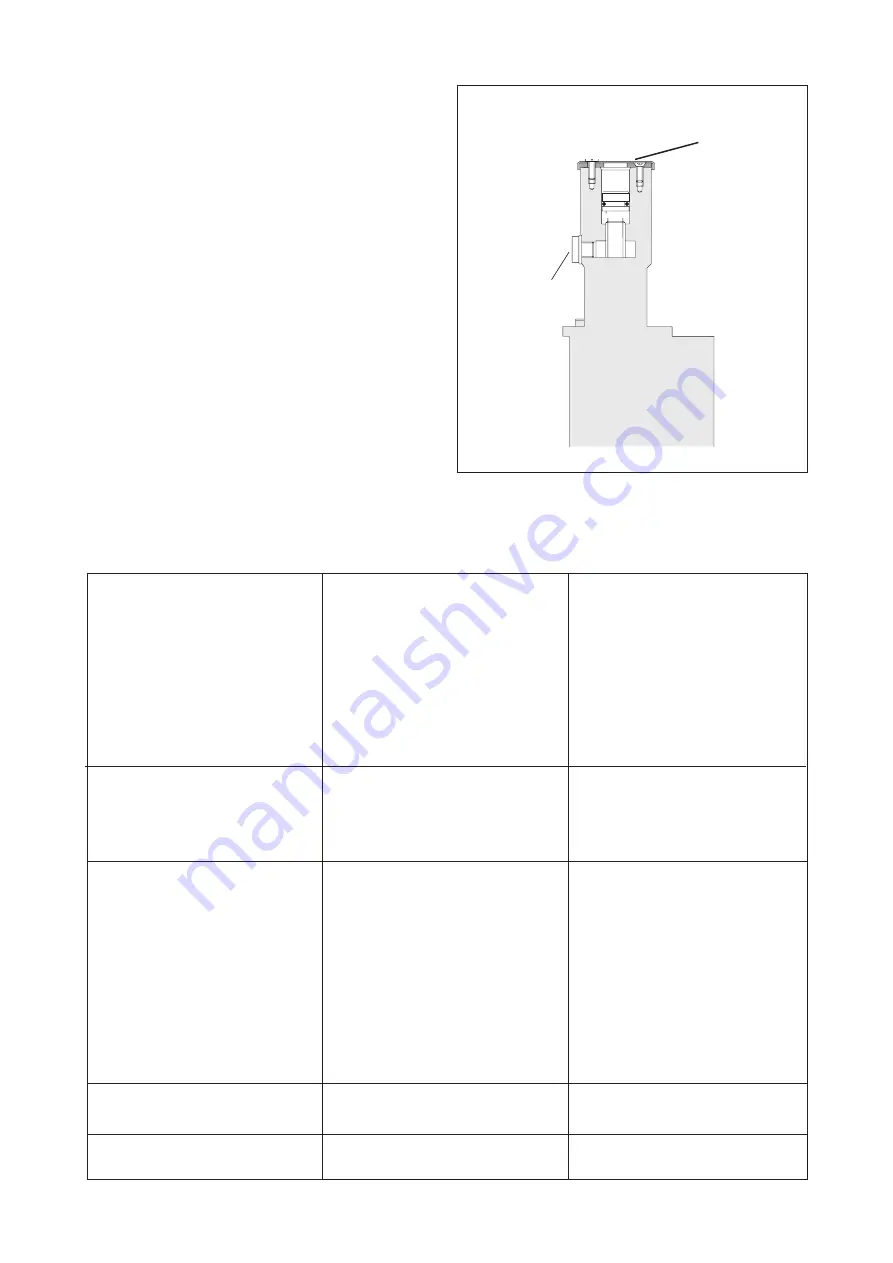
4
www.imo.se
GA
0601.03 en-GB, ID-No.: 901930331, 161-490/A
Start-up
Before starting
Check that all valves necessary for the operation
are fully open and set the pressure to minimum by
turning the set screw CCW.
Starting
Start the pump (or system).
Deaerate the valve and slowly increase the pressure
to the desired value by using the set screw.
In horizontal installations with the outlet downwards
and in vertical installations this is done by opening
the deaeration plug on the spring housing a few
turns and when liquid is coming out, closing the plug.
In horizontal installations with the outlet upwards the
deaeration will be done automatically.
If the valve does not work properly see ”Trouble
shooting”.
- The pressure relief valve is set
too low.
- Counter pressure in the pump
discharge line is too low due to a
major leakage.
- The valve piston of the pres-
sure relief valve is stuck in open
position.
- The valve is too small.
- Improper valve spring.
Pressure too low
What to do
Problem
Cause
Pressure too high
Pressure is fluctuating
”Hunting”
Pressure accumulation too big
Pressure drops below set value
when overflow increases
- The pressure relief valve is set
too high.
- The valve is too big.
- Trapped air in the valve
- Too high viscosity.
- Liquid too cold.
- Valve internals damaged due to
wear or corrosion.
- The throttle screw is not tuned to
the system.
- The throttle screw is not tuned to
the system.
Re-adjust the pressure relief
valve.
Check the components in the
discharge line inclusive the
recipients.
Check the valve. See under
”dismantling”.
Contact your IMO AB representative.
Contact your IMO AB representative.
Re-adjust the pressure relief
valve.
Contact your IMO AB representa
-
tive.
See ”Starting”
The compensation in the valve is
too high for the conditions. The
Compensator piston must be
adjusted. Contact your IMO AB
representative.
Run the system till operating tem
-
perature is reached. If problem
still remains, see above.
Open the valve. See under ”Dis
-
mantling”.
Adjust the throttle screw 647 CW.
Adjust the throttle screw 647
CCW.
Fig. 3
Trouble shooting
Deaeration
plug
537
Set
screw
608