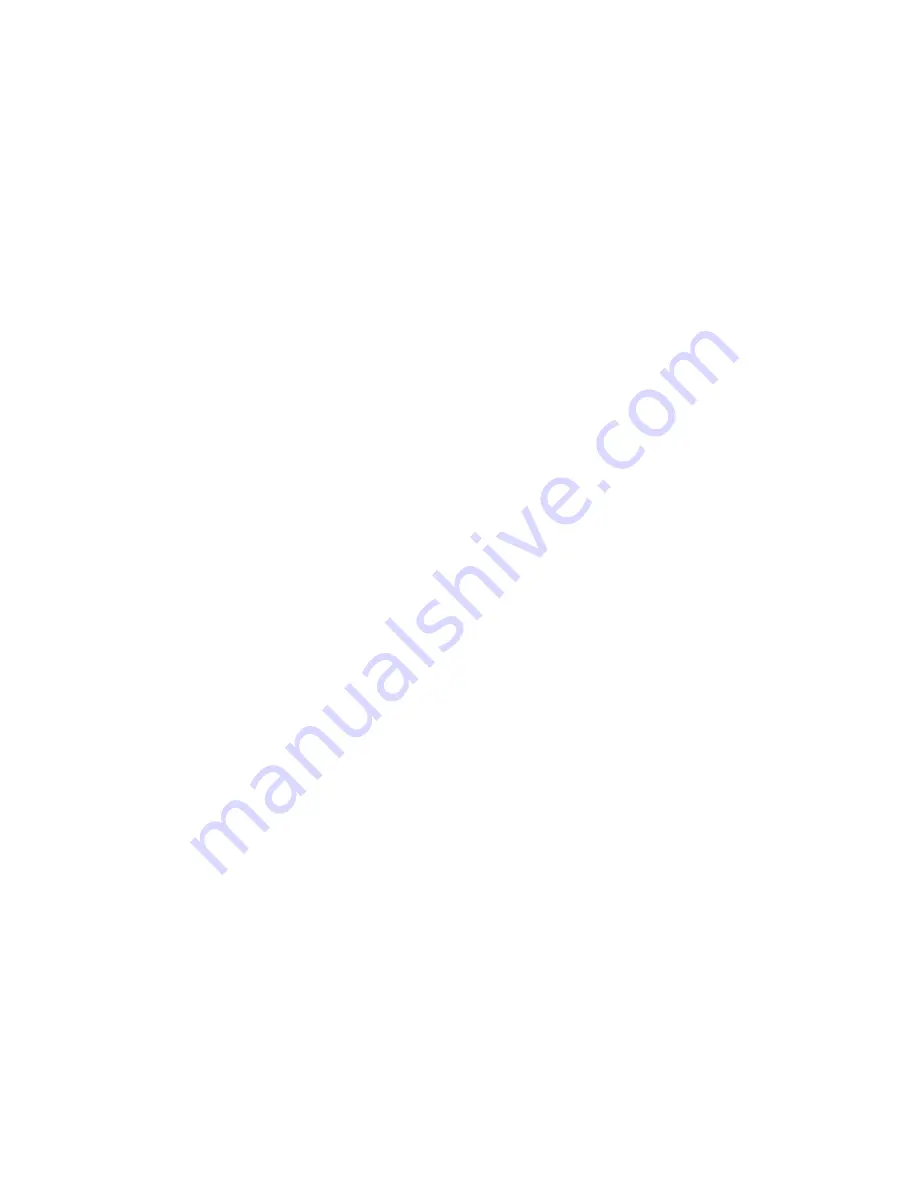
4. Lubricate power rotor (34) with light oil and slide into rotor housings (11). Install inboard idler rotors (40)
by aligning threads with power rotor threads, rotate idlers while pushing towards center of pump. Idler
position may be observed by looking into pump inlet port. Repeat procedure for both outboard idlers
(41).
5. Install assembled brackets (12) on each end of housings (11) using capscrews (16) washers (15) and
nuts (68). Before tightening capscrews (16) in brackets (12), and with each bracket in place, check idlers
(40, 41) to ensure bracket (12) idler stops are in line with ends of idlers. Turning power rotor (34) in its
normal direction of rotation will pull idlers (40 & 41) toward center of pump. Torque capscrews (16) to
value on assembly drawing.
6. Install shim (18) and cover (19) on outboard bracket (12) with capscrews (20) and washers (21). Torque
capscrews (20) to value on assembly drawing.
7. Push coupling end of power rotor (34) into pump as far as it will go. Mount a dial indicator on inboard
bracket (12) with indicator point resting on end of power rotor (34). Set indicator pointer to "zero". Pull
power rotor (34) out from pump until collar (42) contacts face of inboard bushing (45). Check dial
indicator to determine total end float travel. Correct end float is 0.055 to 0.060 inches. If end float
requires shim adjustment, remove cover (19) and shim (18). Remove or add shim lamination to obtain
correct end float. Brass shims have 0.003 inch lamination. Steel shims require full face grinding of metal
to reduce shim thickness. Faces of steel shims after grinding are to be smooth and parallel within 0.002
inch full indicator runout (FIR). If shims are removed for adjustment, install shim (18), cover (19),
capscrews (20) and washers (21). Torque capscrews (20) to value on assembly drawing. Remove dial
indicator from bracket (73). Rotate power rotor (34) to check for any binding.
8. Install O-rings (6) in inboard and outboard covers (2) and install covers (2) on pump case (1) using
capscrews (59). Torque capscrews (59) to value on assembly drawing.
9. Install gasket (5) and rear cover (3) on cover (2) at back end of pump using capscrews (9). Torque
capscrews (9) to value on assembly drawing.
10. Installation of mechanical seal. Reference seal type in pump nomenclature and seal detail on Pump
Assembly drawing. John Crane Type 8-1 and FlowServe (formerly Borg Warner) Type QWD mechanical
seal rotating assembly is installed on the power rotor (34) shaft with setscrews. When the seal housing
(63) is installed, with the mechanical seal stationary seat, the seal is compressed to it correct working
length only if the rotating assembly is correctly positioned when it is installed.
a. Clean and polish pump shaft. Make sure there are no sharp edges or rough spots on shaft to
damage seal O-ring (6) during installation.
b. Pull power rotor (34) in direction toward coupling until thrust collar (42) contacts face of bushing (45).
Place a straight edge across the end face of inboard cover (2) and lightly scribe power rotor shaft at
this point. Measure 15/32” from the scribe mark and lightly scribe the power rotor shaft at this point.
c. Apply a coat of light lubricating oil to pump shaft to aid installation of seal assembly.
d. Apply a coat of light lubricating oil to O-ring in seal rotating assembly and insure O-ring is properly
seated in its groove. Slide seal rotating assembly on to shaft up to scribe mark that is 15/32” from
end face of inboard cover (2). Securely tighten rotating assembly set screws to power rotor shaft.
e. Install a light coat of lubricating oil to mechanical seal stationary sea O-ring. Install mechanical seat
stationary seat into seal housing (63) counter bore. Insure that slot on bottom of seal seat aligns with
anti-rotation pin in seal housing counter bore.
f. Wipe seal faces with a clean lint free cloth.
g. Install seal housing, with installed seal stationary seat, to cover (2) using gasket (5) and hex
capscrews (9). Toque hex capscrews (9) to value on assembly drawing.
11. Install tubing (54) from case (1) on inboard seal housing (63) and outboard cover (2) using tube fittings
(55) and (53).
5
Summary of Contents for IMO G323FHF Series
Page 9: ......