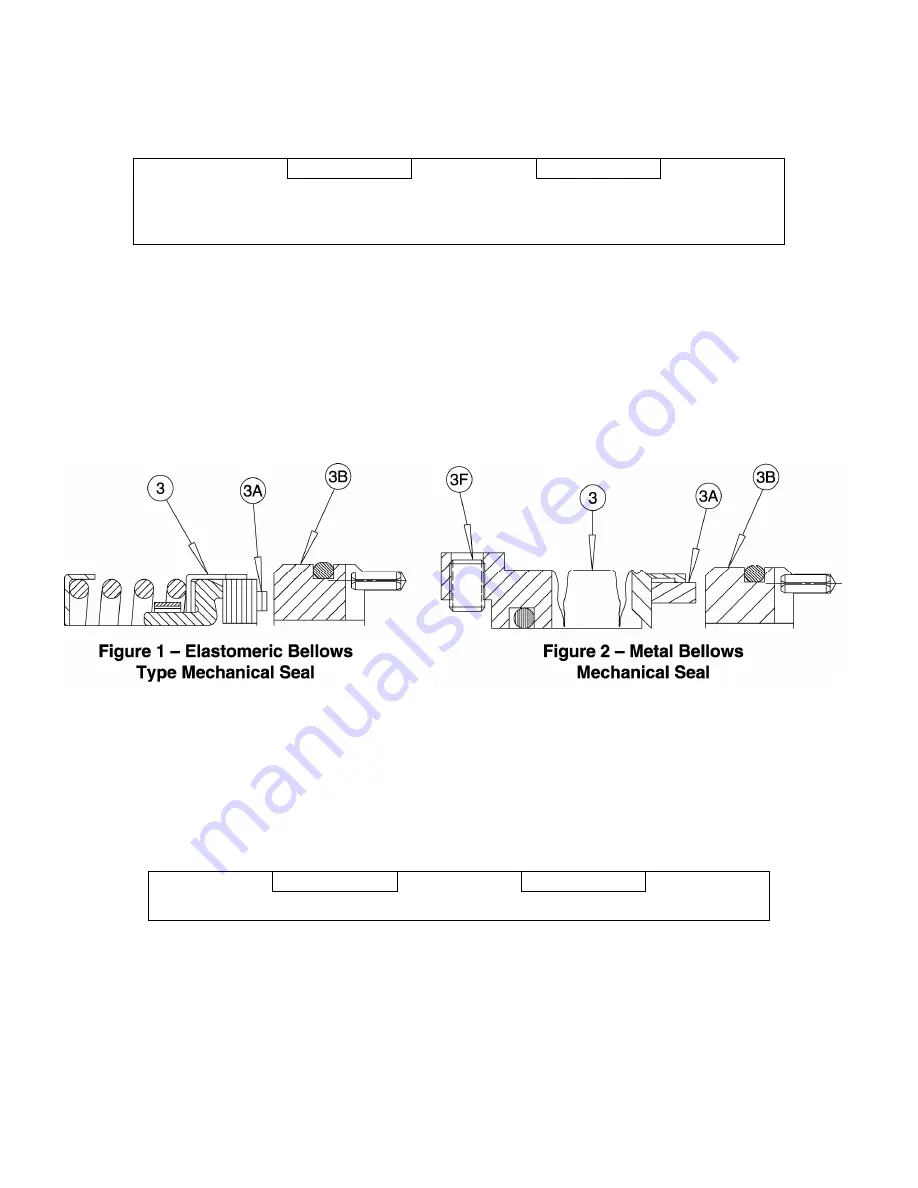
1.
Remove bolts (6) from inboard cover (4) and then remove inboard cover (4) from pump housing (1).
2. For lip seal installed pumps, remove lip seal (16) and O-ring (31) from inboard cover (4). For
mechanical seal installed pumps, remove stationary seat of seal (16) and O-ring (31) from inboard
cover (4).
CAUTION
ATTENTION
In next step, the rotors will be removed from the pump. They will come out as a unit.
Use care to support the rotors set as it is withdrawn from housing so idlers will not be
dropped on floor.
3.
Remove power rotor (7) and idlers (8) by grasping shaft of power rotor and easing it out of housing
(1). Set idlers (8) aside.
4.
For mechanical seal pumps, perform the following:
a) For Elastomeric Bellows Type Seals (see Figure 2 below) – Slide rotating assembly (3) of
mechanical seal (16) off power rotor (7).
b) For Metal Bellows Type Seals (see Fig 3 below) – Loosen set screw (3F) and slide rotating
assembly (3) from power rotor (7).
NOTE:
IF ONLY REPLACING SEALS
, pump disassembly is complete. For seal installation, proceed
to section H5 and complete steps 3 and 7 through 10 and 12 through 16. For mechanical
seal installation, complete steps 4 through 9 and 11 through 16. If the remainder of pump
needs to be disassembled, proceed below.
5.
Remove ball bearing (11) from power rotor (7) by first removing retaining ring (15) from groove in
power rotor (7) shaft. Ball bearing (11) can then be removed with a gear puller or arbor press.
CAUTION
ATTENTION
Removal of bearing by force applied to its outer ring could damage bearing.
NOTE:
Imo Pump strongly recommends replacement of the ball bearing every time the bearing is
pressed off the power rotor.
6.
Remove inlet head (2) by removing four bolts (3 or 6).
7.
Remove O-ring (31 or 26 depending on pump size) from inlet head (2).
5