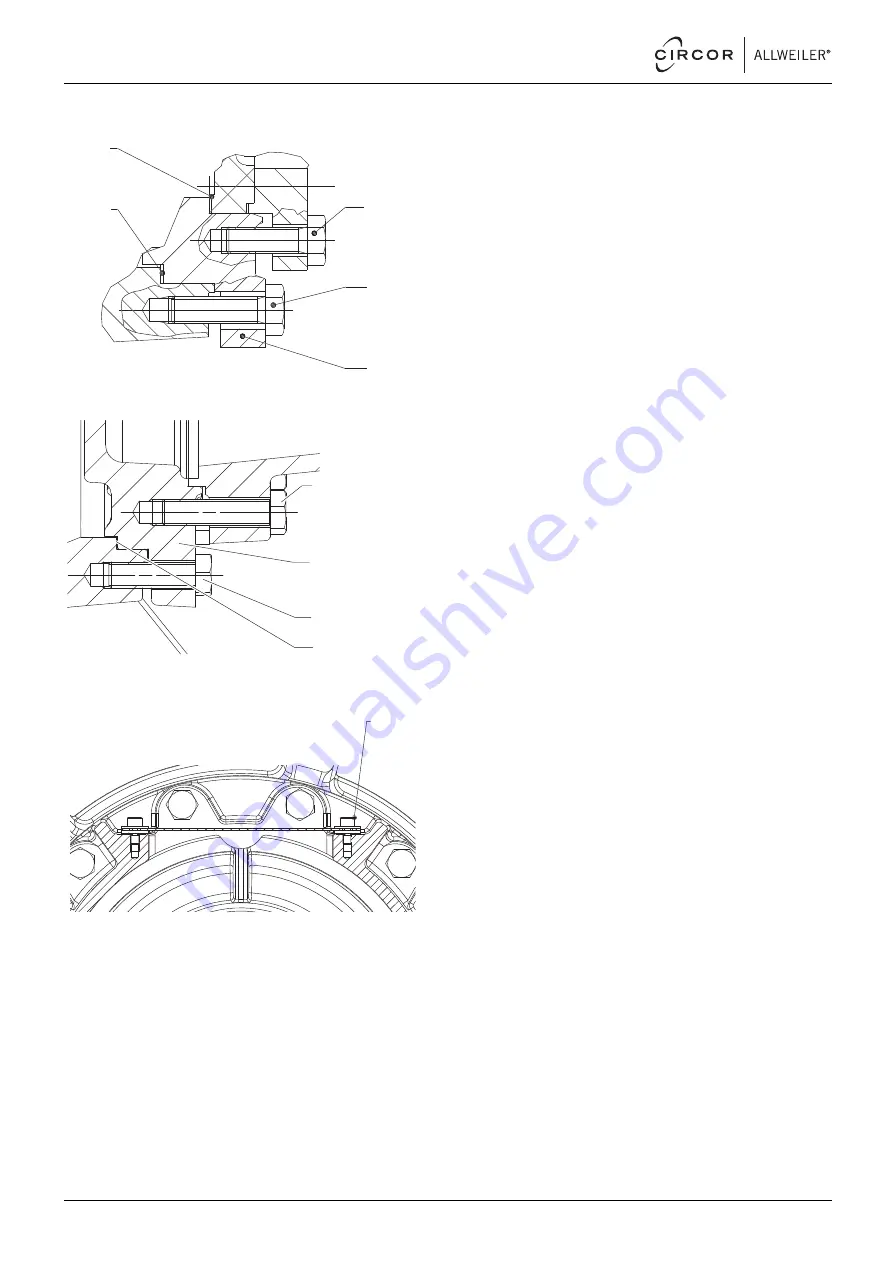
Appendix
901.01
901.02
509.01
400.01
400.02
Fig. 22
Version with intermediate ring for sizes 65-400
901.01
161.01
901.02
400.02
Fig. 23
Version with housing cover 470-315, sizes
65-315, 80-315 and 100/-315
686.01
Fig. 24
Attachment of the guard sheet to the
motor bell housing
38
NI series
BA-2021.06 en-US
550 113 – 146-900/E