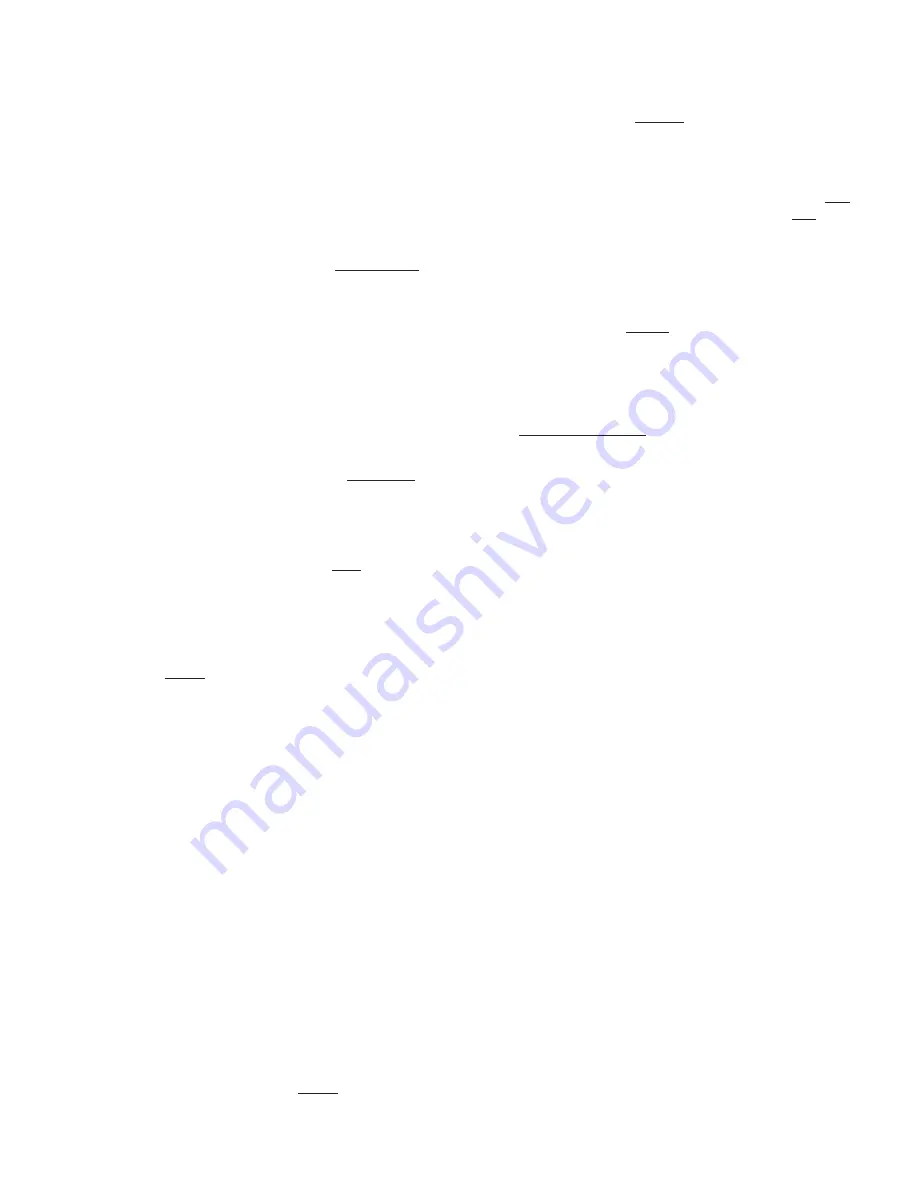
A. Hardware:
All blower and foundation hardware should be checked to make sure it is tight. Wheel set screws or taper-lock bush-
ings should be tightened to the torque values shown in
Tables 1 and 2
on page 5.
NOTE:
If any set screws have come loose, they must be thrown away and replaced.
NEVER
use set screws more
than once.
Replace with knurled, cup-point set screws with a nylon locking patch.
B. Motor Bearing Lubrication:
1. Motor Bearings:
Most smaller motors have sealed bearings that never require re-lubrication for the life of the motor. For any motors with
grease fittings, consult the motor manufacturers recommendations with reference to the lubrication frequency and the
type of grease that should be used.
DO NOT
over grease the motor bearings. Generally, 1-2 shots should be enough. Use a hand operated grease gun at
no more than 40 PSI.
IF POSSIBLE, CAREFULLY
lubricate the motor bearings while the motor is running.
C. Wheel Balance:
All blower wheels are balanced at the factory. It is not uncommon that additional “trim balancing” is required after the
blower is assembled. Trim balancing of the blower assembly, in the field, is typically always necessary for all replace-
ment wheels.
After any wheel is installed, the final balance of the entire blower assembly should be checked.
Refer to Section B on page 8 and Fig. 4 on page 9. Air stream material or chemicals can cause abrasion or corrosion
of the blower parts. This wear is generally uneven and, over time, will lead to the wheel becoming unbalanced, causing
excessive vibration. When that happens, the wheel must be rebalanced or replaced. The other air stream components
should also be inspected for wear or structural damage and cleaned or replaced if necessary.
After cleaning any
blower wheel, it should be balanced and then “trim balanced” on the motor shaft.
There are three ways to balance a blower wheel:
1. Add balancing weights for fabricated aluminum, steel or stainless steel wheels:
Balance weights should be rigidly attached to the wheel at a location that will not interfere with the blower
housing nor disrupt air flow. They should (if at all possible) be welded to the wheel. When trim balancing the
wheel,
on the blower,
be sure to ground the welder
directly
to the blower wheel. Otherwise, the welding
current will likely pass through the motor and damage the motor bearings.
2. Grinding off material for cast aluminum wheels:
If you are grinding on the wheel to remove material, be very careful not to grind too much in one area. That
could affect the structural integrity of the wheel.
3. Forward curved wheels, Model LM only (also known as squirrel cage or multivane wheels).
These wheels have balancing clips attached to individual blades around the wheel. That is the only proper
way to balance this type of wheel.
NOTE:
Removing any forward curve wheel from the blower to clean it, requires special attention when reinstalling
the wheel back into the blower housing. Make sure you reinstall the wheel so the proper wheel-to-inlet
clearance is maintained. Failure to do this will affect the blowers airflow (CFM), static pressure (SP) capabil-
ities and efficiency. Consult Cincinnati Fan or our local sales office for your area for assistance if necessary.
D. Vibration:
As mentioned previously in this manual, excessive vibration can cause premature motor bearing failure that could lead
to catastrophic failure of the blower. After performing any routine maintenance, the vibration readings should be taken
again. New readings should be taken (maximum every 12 months) and compared to the readings you recorded in
Figure 3
, on page 8, during the initial startup.
If any major differences are present, the cause should be deter-
mined and corrected before the blower is put back into operation.
The most common causes of vibration problems are:
1. Wheel unbalance.
3. Poor blower inlet and/or discharge conditions.
2. Mechanical looseness.
4. Foundation stiffness.
E. Dampers and Valves: (Airflow control devices)
Turn off and lock out power to the blower motor. Any dampers or valves should be periodically inspected to make sure
all parts are still operable within their full range and there is no interference with any other damper or blower compo-
nents. Any bearings or seals should be checked for their proper function. The manufacturers maintenance instructions
should be followed.
F. Safety Equipment & Accessories:
It is the users responsibility to make sure that all safety guards required by the company, local, state and OSHA regu-
lations are properly attached and fully functional at all times. If any guards become defective or non-functional at any
time,
the power to the blower MUST be turned off and locked out
until complete repairs and/or replacements have
been made, installed and inspected by authorized personnel.
OMM-23-1009-page 10