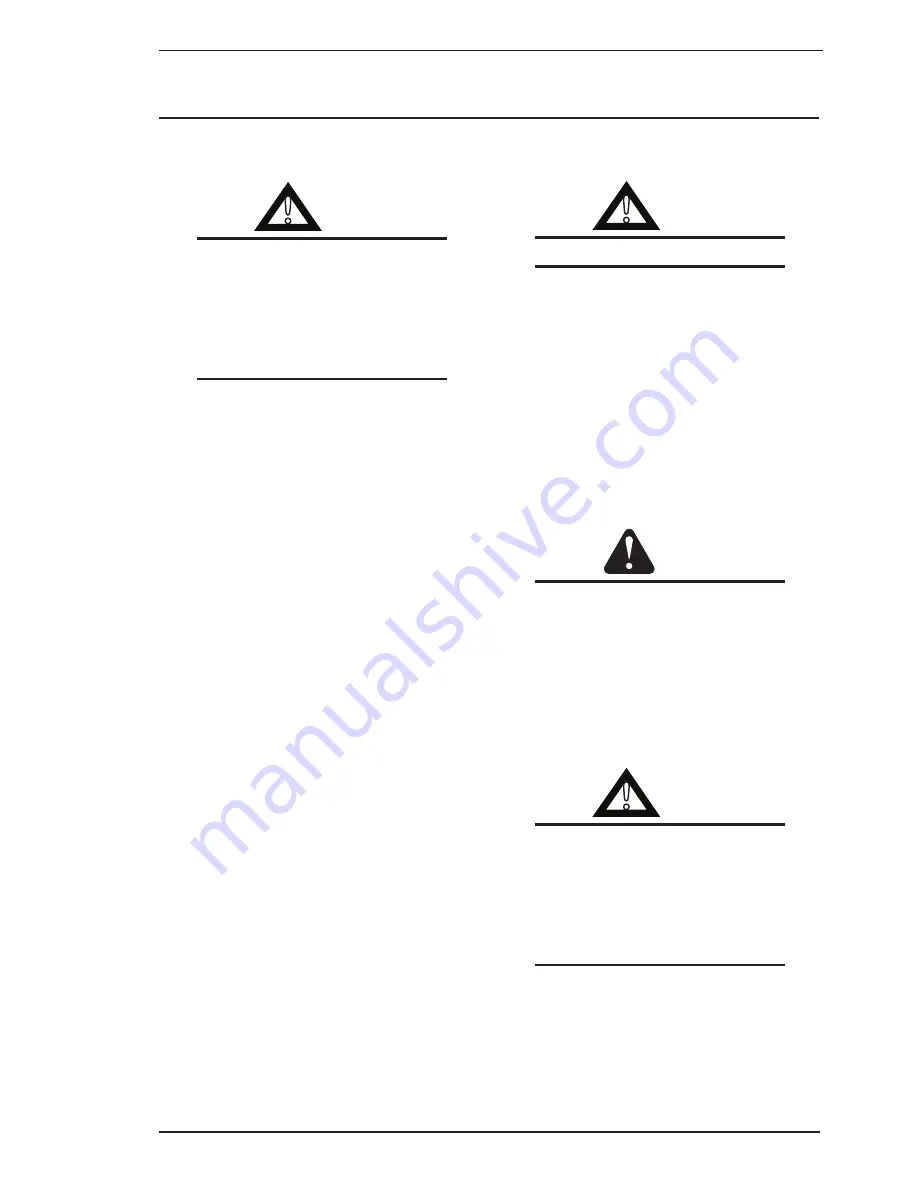
weldskill 100, 135, 150 MiG
5-1
Service
SECTION 5:
SERVICE
5.01 Routine Maintenance &
Inspection
!
WARNING
There are extremely dangerous voltage and
power levels present inside this product.
Do not attempt to open or repair unless
you are a qualified electrical tradesperson.
Disconnect the Welding Power Source
from the Mains Supply Voltage before
disassembling.
Welding equipment should be regularly checked by a
qualified electrical tradesperson to ensure that:
• The main earth wire of the electrical installation
is intact.
• Power point for the Welding Power Source
is effectively earthed and of adequate current
rating.
• Plugs and cord extension sockets are correctly
wired.
• Flexible cord is of the 3-core tough rubber
or plastic sheathed type of adequate rating,
correctly connected and in good condition.
• Welding terminals are shrouded to prevent
inadvertent contact or short circuit.
• The frame of the Welding Power Source is
effectively earthed.
• Welding leads and electrode holder are in good
condition.
• The Welding Power Source is clean internally,
especially from metal filing, slag, and loose
material. If any parts are damaged for any
reason, replacement is recommended.
5.02 Cleaning the Welding Power
Source
!
WARNING
Refer to WARNING on page 3-2.
To clean the Welding Power Source, open the
enclosure and use a vacuum cleaner to remove
any accumulated dirt, metal filings, slag and loose
material. Keep the shunt and lead screw surfaces
clean as accumulated foreign material may reduce
the welders output welding current.
5.03 Cleaning the Feed Rolls
Clean the grooves in the drive rolls frequently. This
can be done by using a small wire brush. Also wipe
off, or clean the grooves on the upper feed roll. After
cleaning, tighten the feed roll retaining knobs.
CAUTION
Do not use compressed air to clean the
Welding Power Source. Compressed air
can force metal particles to lodge between
live electrical parts and earthed metal parts
within the Welding Power Source. This
may result in arcing between this parts
and their eventual failure.
5.04 Basic Troubleshooting
!
WARNING
There are extremely dangerous voltage
and power levels present inside this
product. Do not attempt to open or
repair unless you are a qualified electrical
tradesperson and you have had training in
power measurements and troubleshooting
techniques.
If major complex subassemblies are faulty, then
the Welding Power Source must be returned to an
Accredited CIGWELD Service Provider for repair.
The basic level of troubleshooting is that which
can be performed without special equipment or
knowledge.
Summary of Contents for weldskill 100
Page 6: ......
Page 18: ...Weldskill 100 135 150 MIG 2 6 Introduction This page left blank intentionally...
Page 36: ...Weldskill 100 135 150 MIG 3 18 Installation This Page Left Intentionally Blank...
Page 44: ...Weldskill 100 135 150 MIG 4 8 Operation This Page Intentionally Left Blank...
Page 54: ...weldskill 100 135 150 MIG A 4 Appendix This page left blank intentionally...
Page 58: ......