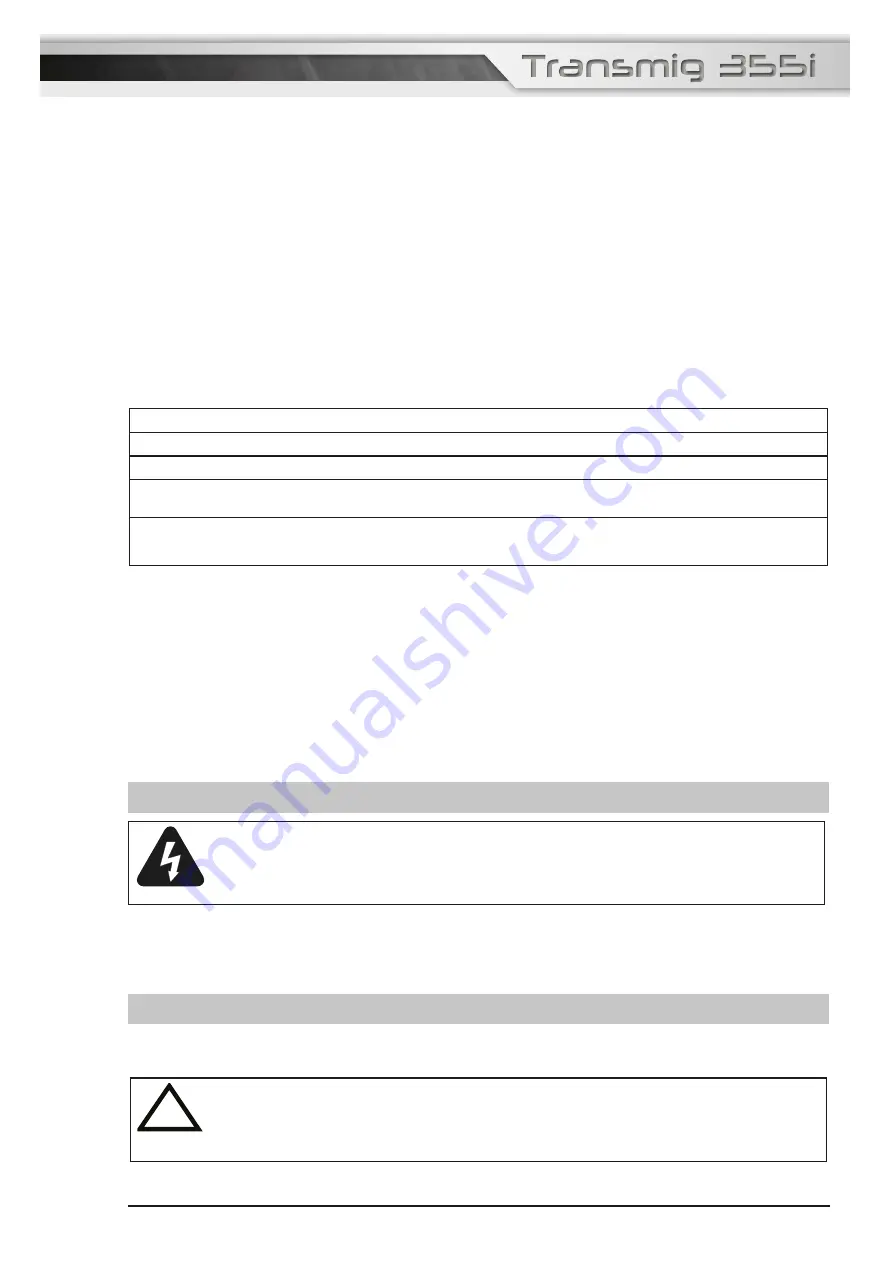
OPERATING MANUAL
Transmig 220i
Manual 0-5586
8-3
ROUTINE SERVICE REQUIREMENTS AND POWER SOURCE PROBLEMS
Power Source Calibration
A. Schedule
Output testing of all Cigweld Inverter Power Sources and applicable accessories shall be conducted at
regular intervals to ensure they fall within specified levels. Calibration intervals shall be as outlined below -
1. For transportable equipment, at least once every 3 months; and
2. For fixed equipment, at least once every 12 months.
If equipment is to be used in a hazardous location or environments with a high risk of electrocution as
outlined in AS 1674.2 - 2007, then the above tests should be carried out prior to entering this location.
B. Calibration Requirements
Where applicable, the tests outlined in Table 8-3 below shall be conducted by an accredited CIGWELD
service agent.
Testing Requirements
Output current (A) to be checked to ensure it falls within applicable Cigweld power source specifications
Output Voltage (V) to be checked to ensure it falls within applicable Cigweld power source specifications
Motor Speed (RPM) of wire drive motors to be checked to ensure it falls within required Cigweld power
source / wire feeder specifications
Accuracy of digital meters to be checked to ensure it falls within applicable Cigweld power source specifi-
cations
Table 8-3: Calibration Parameters
Periodic calibration of other parameters such as timing functions are not required unless a specific fault
has been identified.
C. Calibration Equipment
All equipment used for Power Source calibration shall be in proper working condition and be suitable for
conducting the measurement in question. Only test equipment with valid calibration certificates (NATA
certified laboratories) shall be utilized.
8.02 Cleaning the Welding Power Source
WARNING
There are extremely dangerous voltage and power levels present inside this Inverter Power Source. Do not attempt to
open or repair unless you are an accredited CIGWELD Service Provider. Disconnect the Welding Power Source from the
Mains Supply Voltage before disassembling.
To clean the Welding Power Source, open the enclosure and use a vacuum cleaner to remove any accumulated
dirt, metal filings, slag and loose material. Keep the shunt and lead screw surfaces clean as accumulated foreign
material may reduce the welders output welding current.
8.03 Cleaning the Feed Rolls
Clean the grooves in the drive rolls frequently. This can be done by using a small wire brush. Also wipe off, or
clean the grooves on the upper feed roll. After cleaning, tighten the feed roll retaining knobs.
!!
CAUTION
Do not use compressed air to clean the Welding Power Source. Compressed air can force metal particles to lodge between
live electrical parts and earthed metal parts within the Welding Power Source. This may result in arcing between this
parts and their eventual failure.
Summary of Contents for Transmig 355i
Page 8: ...This Page Intentionally Blank ...
Page 14: ...OPERATING MANUAL GENERAL INFORMATION 1 6 Manual 0 5586 This Page Intentionally Blank ...
Page 24: ...OPERATING MANUAL INTRODUCTION 2 10 Manual 0 5586 This Page Intentionally Blank ...
Page 28: ...OPERATING MANUAL INSTALLATION 3 4 Manual 0 5586 This Page Intentionally Blank ...
Page 84: ...OPERATING MANUAL TIG GTAW WELDING 6 10 Manual 0 5586 This Page Intentionally Blank ...
Page 110: ...OPERATING MANUAL KEY SPARE PARTS 9 4 Manual 0 5586 This page intentionally blank ...
Page 112: ...OPERATING MANUAL APPENDIX A 2 Manual 0 5550 This Page Intentionally Blank ...
Page 115: ...OPERATING MANUAL Transmig 220i This Page Intentionally Blank ...