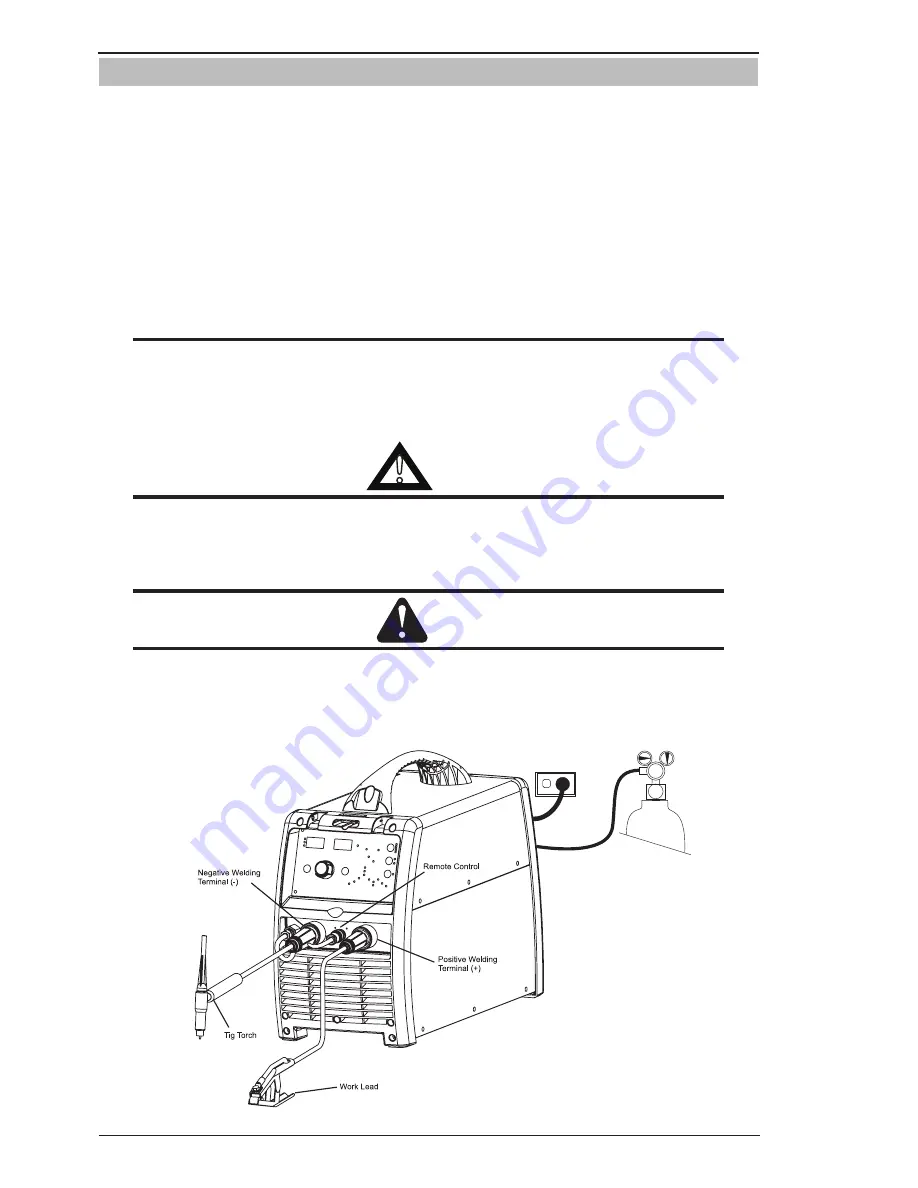
TRANSTIG 300Pi
INSTALLATION, OPERATION AND SETUP
3-10
Manual 0-5309
3.07 Setup for TIG (GTAW) Welding
A. Select HF TIG or Lift TIG mode with the process selection control (refer to Section 3.06.11 for further
information).
B. Connect the TIG Torch to the negative welding terminal (-). Welding current flows from the power source
via heavy duty bayonet type terminals. It is essential, however, that the male plug is inserted and turned
securely to achieve a sound electrical connection.
C. Connect the work lead to the positive welding terminal (+). Welding current flows from the Power Source
via heavy duty bayonet type terminals. It is essential, however, that the male plug is inserted and turned
securely to achieve a sound electrical connection.
D. Connect the TIG torch trigger switch via the 8 pin socket located on the front of the power source as shown
below. The TIG torch will require a trigger switch to operate in HF TIG and Lift TIG Mode.
NOTE
If the TIG torch has a remote TIG torch current control fitted then it will require to be connected to
the 8 pin socket. (Refer to section 3.06.08 Remote Control Socket for further information).
E. Fit the welding grade shielding gas regulator/flowmeter to the shielding gas cylinder (refer to Section 3.10)
then connect the shielding gas hose from the Power Source to the regulator/flowmeter outlet.
!
WARNING
Before connecting the work clamp to the work and inserting the tungsten electrode in the TIG Torch
make sure the mains power supply is switched off.
Secure the welding grade shielding gas cylinder in an upright position by chaining it to a stationary
support to prevent falling or tipping.
CAUTION
Remove any packaging material prior to use. Do not block the air vents at the front or rear of the
Welding Power Source.
Loose welding terminal connections can cause overheating and result in the male plug being fused
in the terminal.
A-12102
Figure 3-6: Setup for TIG Welding