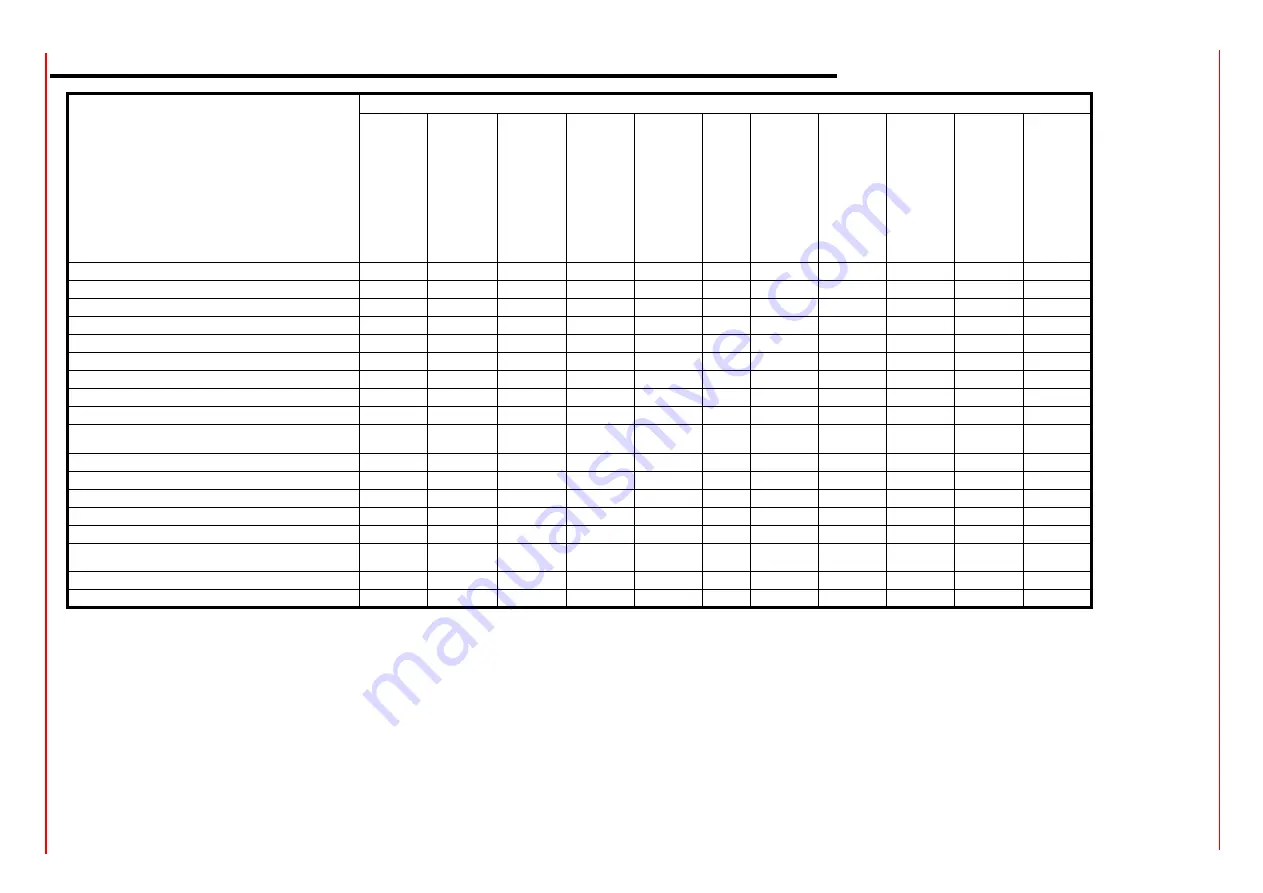
P
A
R
T
IV
: MAIN
TENANCE
31
8.0 TROUBLESHOOTING
CAUSE
TROUBLE
THE BURNER
DO
ESN’TSTART
CON
T
INUE WITH PRE-
PU
R
G
E
DOESN’T
START A
ND LOCK-
OUT
DOESN’T START
A
ND
REP
EATS
THE
CYCLE
ST
AR
T
S
AN
D
R
E
PE
A
T
S
TH
E
CYCL
E
ST
AR
T
S
AN
D
L
O
C
K
-O
U
T
THE FLAME
MON
ITO
R
DEV
ICE
DOE
S
N’T
GIV
E
CONSE
N
T
TO START
DOESEN’T
SWIT
CH TO HIGH
FLAME
DOESEN’T
RETURN IN L
O
W
FLAME
LOCK-OUT
DURING
O
PERATI
O
N
TTURNS OF
A
N
D
REP
EATS
CYCL
E D
URING OPE
R
ATION
MAIN SWITCH OPEN
z
LACK OF GAS
z
z
MAXIMUM GAS PRESSURE SWITCH DEFECTIVE
z
z
THERMOSTATS/PRESSURE SWITCHES DEFECTIVES
z
z
z
OVERLOAD TRIPPED INTERVENTION
z
AUXILIARIES FUSE INTERRUPTED
z
DEFECTIVE CONTROL BOX
z
z
z
z
z
DEFECTIVE ACTUATOR
z
z
z
AIR PRESSURE SWITCH FAULT OR BAD SETTING
z
z
z
z
MINIMUM GAS PRESSURE SWITCH DEFECTIVE OR GAS
FILTER DIRTY
z
z
z
z
z
IGNITION TRANSFORMER FAULT
z
IGNITION ELECTRODES BAD POSITION
z
BUTTERFLY VALVE BAD SETTING
z
z
DEFECTIVE GAS GOVERNOR
z
z
z
z
GAS VALVE DEFECTIVE
z
BAD CONNECTION OR DEFECTIVE HIGH/LOW FLAME
THERMOSTAT OR PRESSURE SWITCH
z
z
ACTUATOR CAM WRONG SETTING
z
z
z
UV PROBE DIRTY OR DEFECTIVE
z
z
z
Summary of Contents for Low NOx Series
Page 33: ...PART IV MAINTENANCE 33 ...
Page 35: ......