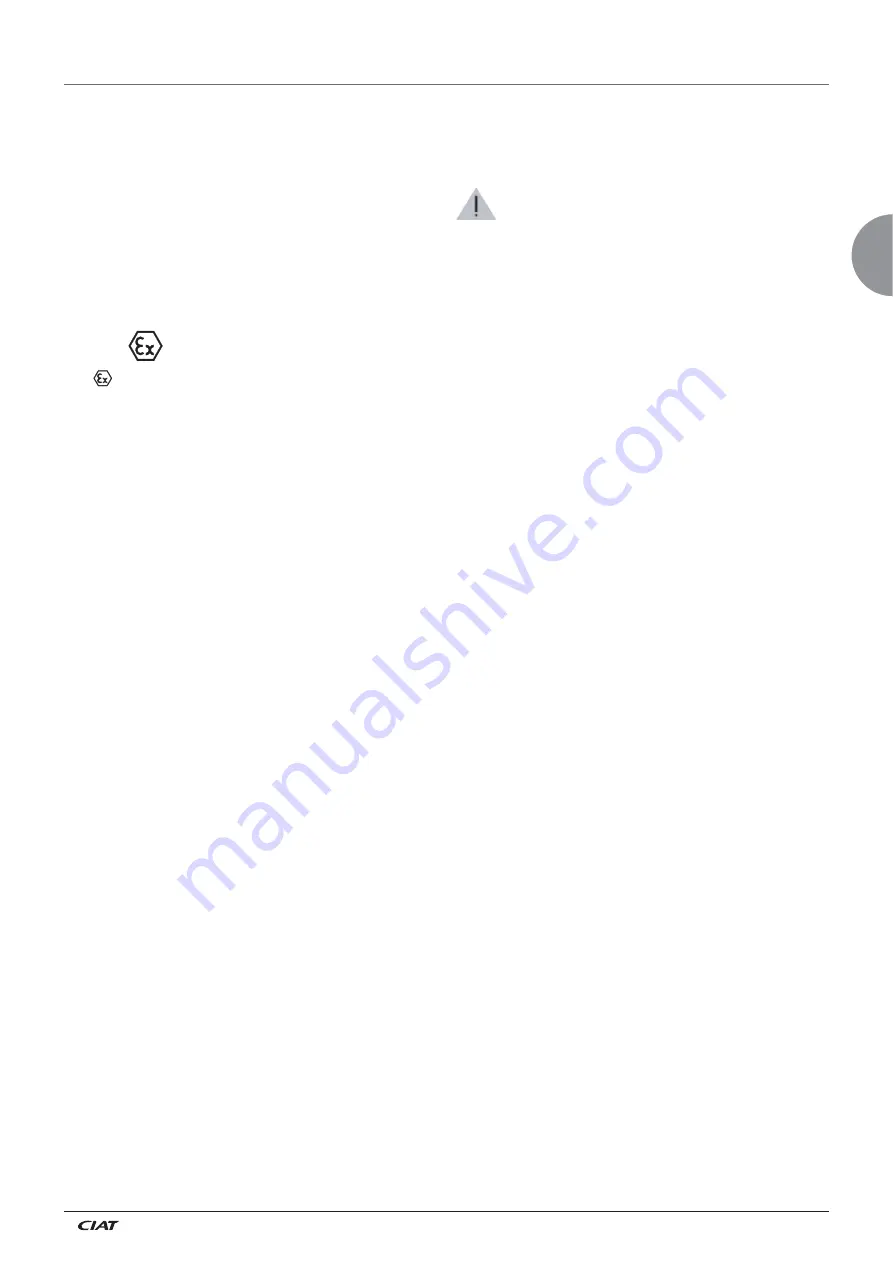
E N
EN - 21
NA 03.28 D
7. Special information for ATEX areas
in accordance with directive 94/9/EC (explosive atmospheres)
7.2 Marking
Each unit is supplied with an ATEX Conformity Certificate; the ATEX marking is inscribed on the name plate as shown below:
Example:
II 3/2 G / D* c IIA T5
: standardised ATEX logo
II: Group II = surface industries
3/2: Equipment category: 3 = installation in zone 2 or 22 , 2 = installation in zone 1, 2 or 22
G: Equipment which can be installed in a gas zone
D: Equipment which can be installed in a dust zone, (*): only in zone 22 (category 3 equipment)
c: Constructional safety
IIA: Gas/Dust explosion group (Gas groups IIA, IIB, IIC. Dust groups IIIA, IIIB, IIIC)
T5: Temperature class (T1 to T6 for gas, actual temperature for dust)
For category 2, a copy of the technical conformity dossier is saved and archived for 10 years by a notified body. The archiving number
for the dossier is sent to the customer.
> The units must be installed and commissioned by a qualified
professional.
> All the provisions set out by the current directives and
standards must be respected during installation, for example,
automatically linking the unit's supply to the presence of a flow
rate detected by a sensor.
> In all cases, refer to the general information section of this
manual, to the specific manuals for the ATEX components
built into the unit and listed in the ATEX dossier, and to the
specific precautions below:
Install the units so that the temperatures at and around the
intake are between – 20 and + 60 °C.
The units and the additional metal elements must be
connected electrically by a grounding cable linked to the
frame.
Select and install all the electrical connection and control
components according to the risk zone in which they will
be installed.
All remote metal components (sheaths, pipes, etc.) must
be grounded, if necessary by grounding cables.
Always connect the motor heat protection
(see § 4 – SYSTEM START-UP)
> The installer must use all available devices to ensure that
the temperature of the various elements of the installation
remains below the autoignition temperature of the gas and/or
the dust in question.
> If the connections to the various pieces of built-in equipment
require feeding through walls (passage of cables, sensors,
etc.), these feedthroughs must be sealed to prevent the
"ATEX" atmosphere from dispersing. The same is true for the
connections between the various blocks which form the unit
and for the connections to the ducts.
> Any modification to the unit without prior approval from CIAT is
prohibited.
> Ensure that, during assembly or maintenance operations, no
element (tools, screws, components) are left in the unit,
as this could cause a dangerous situation to arise (see
section "Information concerning the use of tools in explosive
atmospheres").
> Prior to any maintenance operation, ensure that the unit is
powered off.
> After each maintenance operation, check that all the removed
components have been refitted and secured in their original
position.
> Ensure that the ground straps are in good condition and
reconnected.
> Regularly check that removable components, such as enclosures
or covers, and movable components, such as damper blades
or filter runners, are secure.
> Evaluation of the level of danger of explosion established
in accordance with standards EN 13463-1 : 2009 and
EN 1127-1 : 2011.
> The units are certified as complying with the recommendations
in standard EN 13463-5 : 2003 "Protection by constructional
safety 'c'.
> The user must classify the various potentially explosive areas in
accordance with directive 1999/92/EC.
> The air handling units are selected and manufactured based on
the type of area defined by the user.
A unit must never operate under conditions other than
those it was designed for.
7.1 General information
7.3 System start-up, maintenance