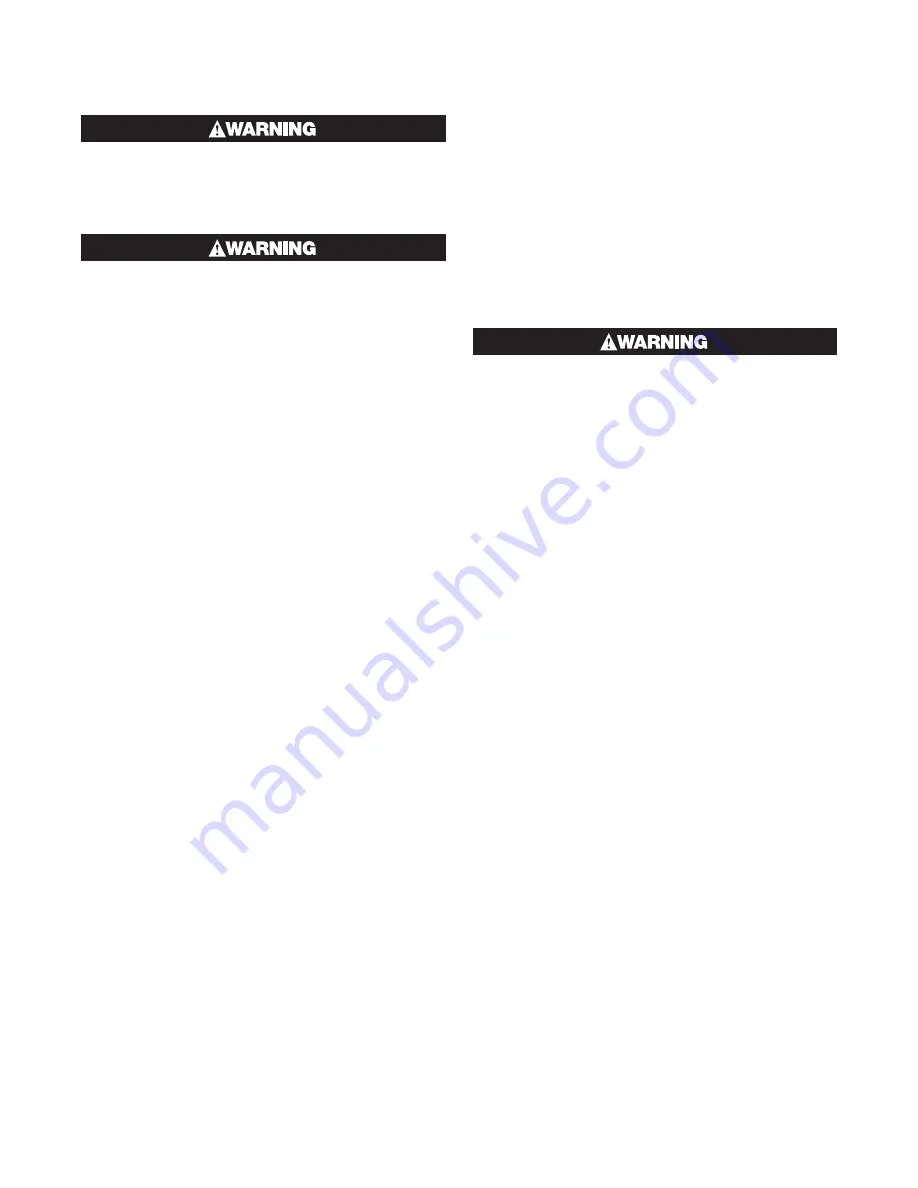
11
Pump Removal/Replacement
ELECTRIC SHOCK HAZARD. Disconnect all
power to system before servicing. Failure to
comply can result in personal injury or equip-
ment damage.
BURN HAZARD. Never service system while
hot. Allow system to cool to room temperature
before servicing.
1. If pump requires service, drain system and remove
top and side panels.
2. Pump/motor can be removed from the system as
an assembly for service.
3. Disconnect piping at unions on inlet and outlet pip-
ing leading to the pump.
4. Remove four bolts which hold the pump/motor
base to the base of the system.
5. After verifying power is disconnected remove con-
duit and wiring from the motor.
6. Lift out pump/motor assembly.
7. Service pump per pump manufacturers instruc-
tions.
8. If replacing the pump, be sure to remove piping
from old pump casing before discarding. Clean
thread on pipe and thread into new pump casing
using high temperature oil resistant thread sealant.
DO NOT USE TFE OR OTHER TAPE SEALANTS.
9. Install new pump in system reconnect piping.
10. Reconnect wiring and check rotation as indicated
in “INSTALLATION” section.
ELECTRIC SHOCK HAZARD. Close the front
electrical enclosure door and retighten the
locking screw. This must be done to limit ac-
cess to high voltage components. Failure to
comply could result in personal injury or equip-
ment damage.