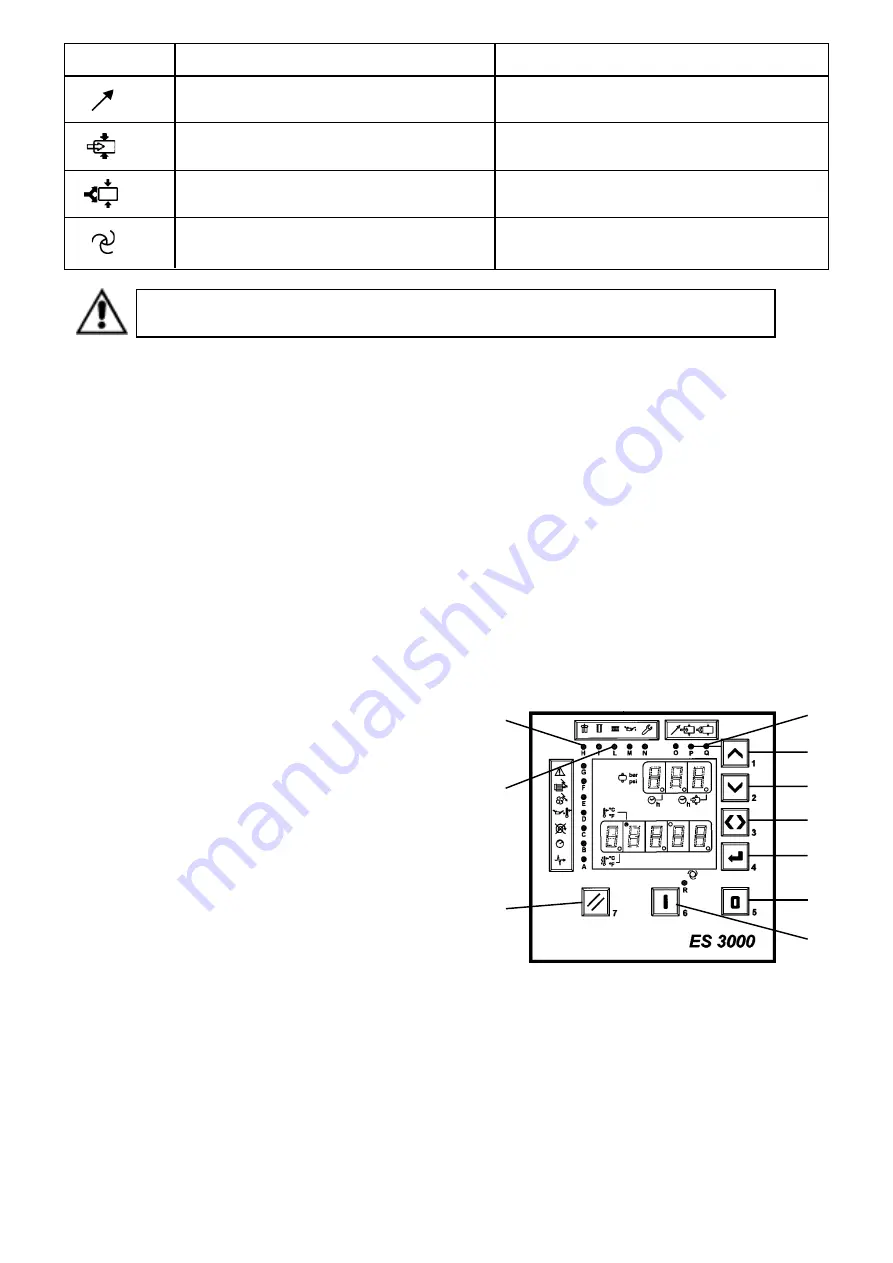
Chicago Pneumatic Compressors
62 305 454 65
01/2008
Page 14
Symbol
Flashing LED
LED on
Deactivated
Deactivated
-
Compressor operation charged
Manually purged compressor
No load compressor operation
Compressor on stand by(15 seconds) or in stopping
Compressor operating
process(30 seconds)
ATTENTION : To restart after the intervention of a protective device (Alarm) press "RESET"
and then press the start button " I " (6).
(O)
(P)
(Q)
(R)
Operation of the controller
The controller is programmed for Energy Saving; it switches off
the compressor, thus reducing idle running to a minimum.
The controller operates with no load before stopping for a period
of time which becomes shorter as air consumption decreases.
The controller also indicates if maintenance is required on the
filters, etc.
(Yellow LEDs)
.
3 - Operating hours display
Press
item. 3 Fig. 7a
in order to view the total number of operating
hours. The amount of operating hours is displayed on the lower
section of the screen. A small dot comes on (confirmation light)
on the upper left of the screen. To see the LOADED operating
hours press again on
item. 3 Fig 7a
and a small dot appears on
the upper right of the screen (confirm LED).
4 - Operating hours display for components
requiring maintenance
To display the amount of operating hours for each component
requiring maintenance folw the instructions in
Section 4 - 5
up to
point 4; the operating hours will be displayed on the lower screen.
- Press button
Item. 3 Fig. 7a
to exit.
5 - Resetting the maintenance meters (YELLOW
LEDs excluding LED "A")
If a meter is to be returned to zero (for example
Item. L
air filter)
after maintenance has been carried out, proceed as follows: (See
Fig. 7a
)
1) Press buttons
Item. 7
and
Item. 4
at the same time until the
indicator light comes on
Item. H.
2) Release buttons
Item. 7
and
Item. 4
3) Use buttons
Item. 1
and
Item. 2
to select LED
Item. L
(air
filter) for the required component.
4) Up to 5 figures are displayed on the lower section of the
screen showing the component's operating hours
Item. L
(air filter).
5) Press once on button
Item. 4
, the displayed value flashes,
press for a second time on the button
Item. 4
, the lower
screen is then returned to zero and the LED
Item. L
will
come on.
6) Press button
Item. 3
to exit
RESET
7) To return another component to zero, go LED using but-
tons
Item. 1
and
Item. 2.
After being inactive for 30 seconds the board automatically
exits Setting.
Fig. 7a
L
7
H
Q
1
2
3
4
5
6