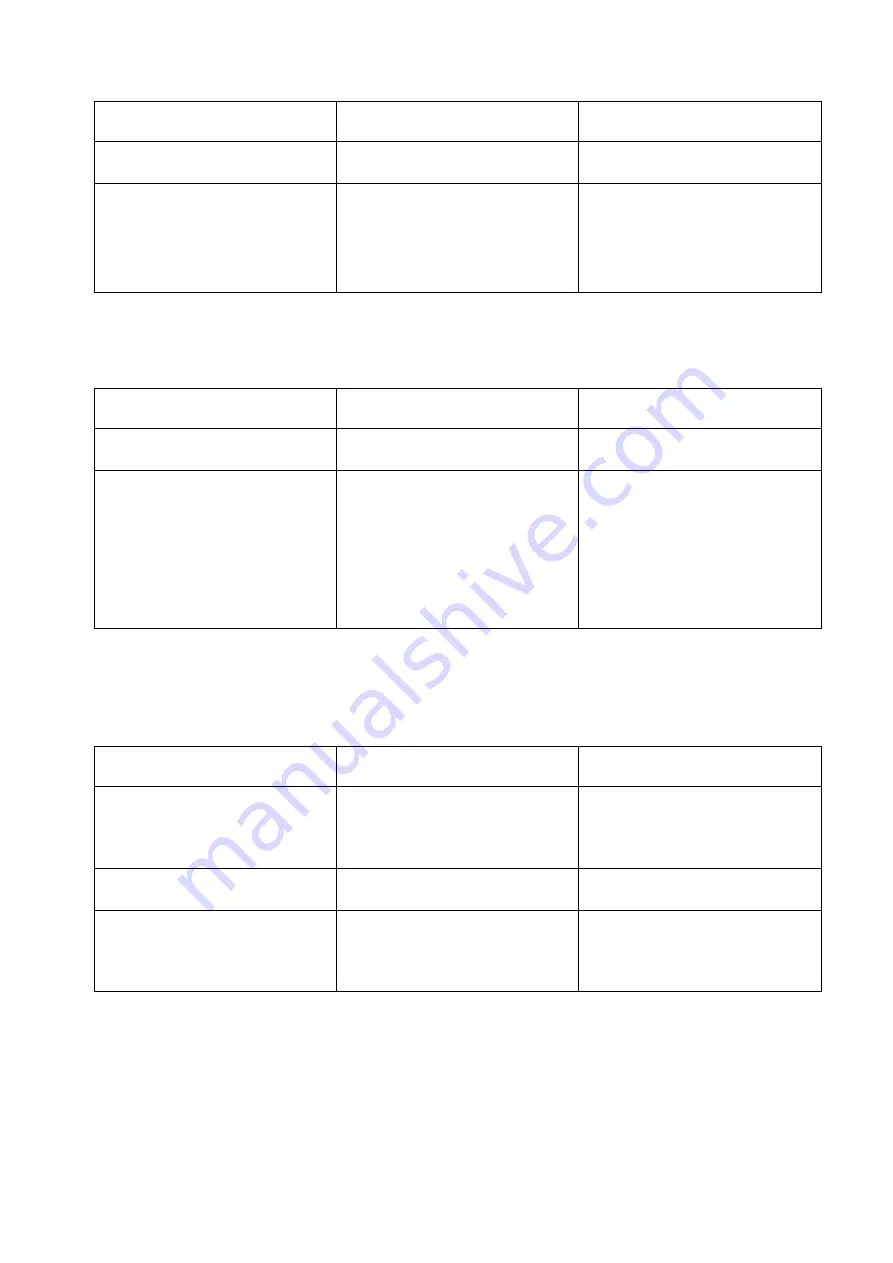
47
11.3
Impact force too low
ÂÂÂÂÂÂÂÂÂÂÂ
ÂÂÂÂÂÂÂÂÂÂÂ
ÂÂÂÂÂÂÂÂÂÂÂ
Cause
ÂÂÂÂÂÂÂÂÂÂÂÂ
ÂÂÂÂÂÂÂÂÂÂÂÂ
ÂÂÂÂÂÂÂÂÂÂÂÂ
Remedy
ÂÂÂÂÂÂÂÂÂÂÂ
ÂÂÂÂÂÂÂÂÂÂÂ
ÂÂÂÂÂÂÂÂÂÂÂ
by
G
as pressure too low
Fill piston accumulator
E
x
ca
v
ator dri
v
er
Deli
v
ery rate from hydraulic
system pump inade
q
uate
Check pump characteristics with
measuring de
v
ice and compare
with original specifications; if
necessary replace pump
Checking:
Chicago Pneumatic
Customer Center
/
dealer in your
region
Replacing:
Aftermarket depart
ment of e
x
ca
v
ator manufacturer
11.4
Impact rate too high and impact force too low
ÂÂÂÂÂÂÂÂÂÂÂ
ÂÂÂÂÂÂÂÂÂÂÂ
ÂÂÂÂÂÂÂÂÂÂÂ
Cause
ÂÂÂÂÂÂÂÂÂÂÂÂ
ÂÂÂÂÂÂÂÂÂÂÂÂ
ÂÂÂÂÂÂÂÂÂÂÂÂ
Remedy
ÂÂÂÂÂÂÂÂÂÂÂ
ÂÂÂÂÂÂÂÂÂÂÂ
ÂÂÂÂÂÂÂÂÂÂÂ
by
No gas in piston accumulator
Fill piston accumulator
E
x
ca
v
ator dri
v
er
O
rings defecti
v
e
(CP 550 parts
9
and
1
2)
K
(CP 750 part
1
03)
K
(CP
11
50 parts
1
20 and
1
2
6
)
K
(CP
16
50 parts
1
7 and 5
1
)
K
(CP 2250 parts
1
8
and 20)
K
(CP 3050 and CP4250
parts 2
8
and 42)
K
Replace
O
rings
Workshop
K
parts nos refer to
v
alid spare parts lists
11.5
Oil leaks from ports »P« and »T«
ÂÂÂÂÂÂÂÂÂÂÂ
ÂÂÂÂÂÂÂÂÂÂÂ
ÂÂÂÂÂÂÂÂÂÂÂ
Cause
ÂÂÂÂÂÂÂÂÂÂÂÂ
ÂÂÂÂÂÂÂÂÂÂÂÂ
ÂÂÂÂÂÂÂÂÂÂÂÂ
Remedy
ÂÂÂÂÂÂÂÂÂÂÂ
ÂÂÂÂÂÂÂÂÂÂÂ
ÂÂÂÂÂÂÂÂÂÂÂ
by
Threaded connections between
connecting flange and breaker
hose are loose CP2250
Tighten threaded connections
E
x
ca
v
ator dri
v
er
Cap nuts loose
Tighten cap nuts
E
x
ca
v
ator dri
v
er
C
L
hose connection on port
»P«
for CP
−L
ube (or plug if
CP
−L
ube not fitted) loose
Tighten hose connections
Tighten plug
E
x
ca
v
ator dri
v
er