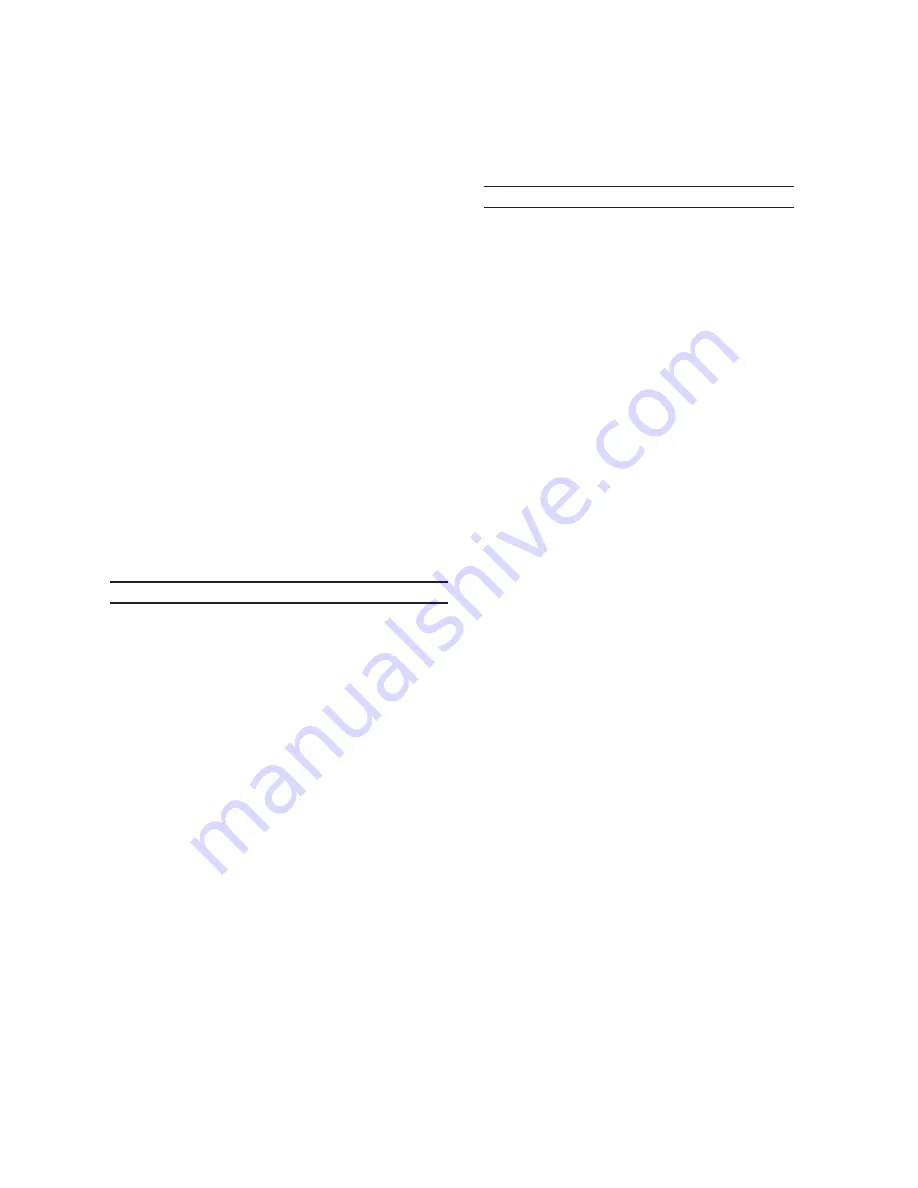
SKU 66660
For technical questions, please call 1-800-444-3353.
Page 15
scale graduations are stamped on the
face of Bevel Angle Bracket (101). An
indexing pointer is stamped on the
adjacent tab. For greater accuracy,
use an angle finder (not supplied)
to measure and confirm the desired
angle. To adjust the bevel angle
passed 45 degrees and up to 51.5
degrees, pushing in the Bevel Angle
Release Push button (90) will allow
the Bevel Angle Bracket to be further
tilted. Rotate the Cam Lever (88B)
clockwise to lock-in the setting.
Prior to the initial use, make a 90º de-
4.
gree cut on a solid piece of wood (do
not use particle board or plywood).
With a protractor verify whether the
cut is square. For fine tuning the
“Zero” degree setting of the Bevel
Angle Bracket (101), use the Set
Screw (94).
Work piece and Work area Set Up
Designate a work area that is clean
1.
and well-lit. The work area must not
allow access by children or pets to
prevent injury and distraction.
Route the power cord along a safe
2.
route to reach the work area without
creating a tripping hazard or exposing
the power cord to possible damage.
The power cord must reach the work
area with enough extra length to al-
low free movement while working.
Secure loose work pieces using a
3.
vise or clamps (not included) to pre-
vent movement while working.
There must not be hazardous ob-
4.
jects, such as utility lines or foreign
objects, nearby that will present a
hazard while working.
Be sure to select and install an ap-
5.
propriate saw blade in good condition
before starting work.
General operating Instructions
Clean the work surface and under-
1.
side of the Base Plate (103).
Check lubricating oil level before
2.
initial use and after every 25 hours
of operation. Locate the Base Plate
(103) at the corner of work bench
with the rear end accessible and
the Lower Guard resting against the
bench. Use a “C” Clamp to secure
the end of the Base Plate to the
bench.
With a 6mm hex key remove the Oil
3.
Fill Plug (50).
Oil level should just reach bottom of
4.
the threads in the Worm Gear Hous-
ing (18).
If required, fill with exact brand of oil
5.
specified in the Specifications section
of this manual.
Prior to reattaching the Oil Fill Plug,
6.
inspect the condition of the O-ring
gasket. Replace if torn, damaged or
elongated.
Replace the plug and tighten snug.
7.
Do not over tighten.
To operate tool, place it at the end
8.
of the work piece, with the blade not
touching the work piece.
Squeeze the Trigger (79) to start the
9.
tool operating.
Guide the saw along the line to be cut.
10.
When the cut is complete, release the
11.
Trigger to allow the Blade to come to
a complete stop.