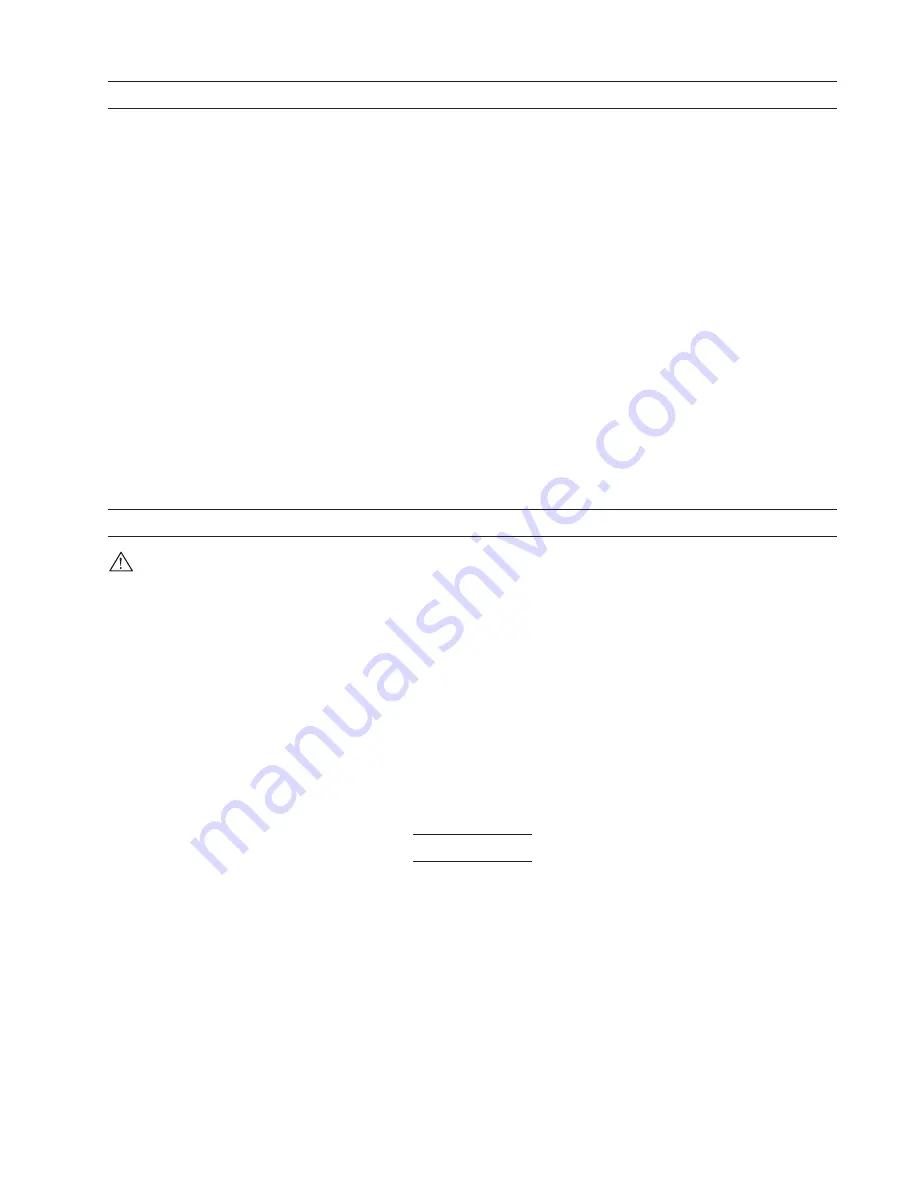
Page 7
SKU 07570
For technical questions, please call 1-800-444-3353.
REV 01/05
OPERATING INSTRUCTIONS
Before initial operation, verify that:
1.
The Motor is dry.
2.
The voltage and frequency stamped on motor and control nameplates correspond with
that of the input power line.
3.
All connections to the motor are correct.
4.
The rotor turns freely when disconnected from the load.
5.
The motor is detached from the load for the initial start. Operate the motor without a load
for about one hour to test for any localized heating in bearings and windings.
6.
The motor operates in counterclockwise rotation.
7.
The voltage is correct and balanced at the motor terminals, and no-load current draw (in
amps) is correct.
8.
The motor comes up to its operational speed and is not being overloaded.
INSPECTION, MAINTENANCE, AND CLEANING
WARNING! Make sure the Power Switch of the Motor is in its “OFF” position and that
the tool is unplugged or disconnected from its electrical outlet before performing any
inspection, maintenance, or cleaning procedures.
1.
Before each use, inspect the general condition of the Motor. Check for loose screws,
misalignment or binding of moving parts, cracked or broken parts, damaged electrical
wiring, and any other condition that may affect its safe operation. If abnormal noise or
vibration occurs, have the problem corrected before further use. Do not use damaged
equipment.
2.
Maintenance and repairs should only be done by a qualified technician.
3.
Periodically recheck all nuts, bolts, and screws for tightness.
4.
Store in a clean and dry location.
Lubrication
Note: If lubrication instructions are shown on motor, they will supersede this general
instruction. Lubrication should be completed by a qualified technician.
1.
The Motor is properly lubricated at the time of manufacture. It is not necessary to lubricate
at time of installation unless the motor has been in storage for a period of 12 months or
longer.
2.
Re-oil sleeve bearings with drops of 5W20 viscosity motor oil every 2000 hours of normal
service. Direct drive operation (no pulleys) requires lubrication every 3000 hours of normal
service.
3.
Sealed ball bearings require no attention during the life of the bearing.
Brought to You by Augusta Flint