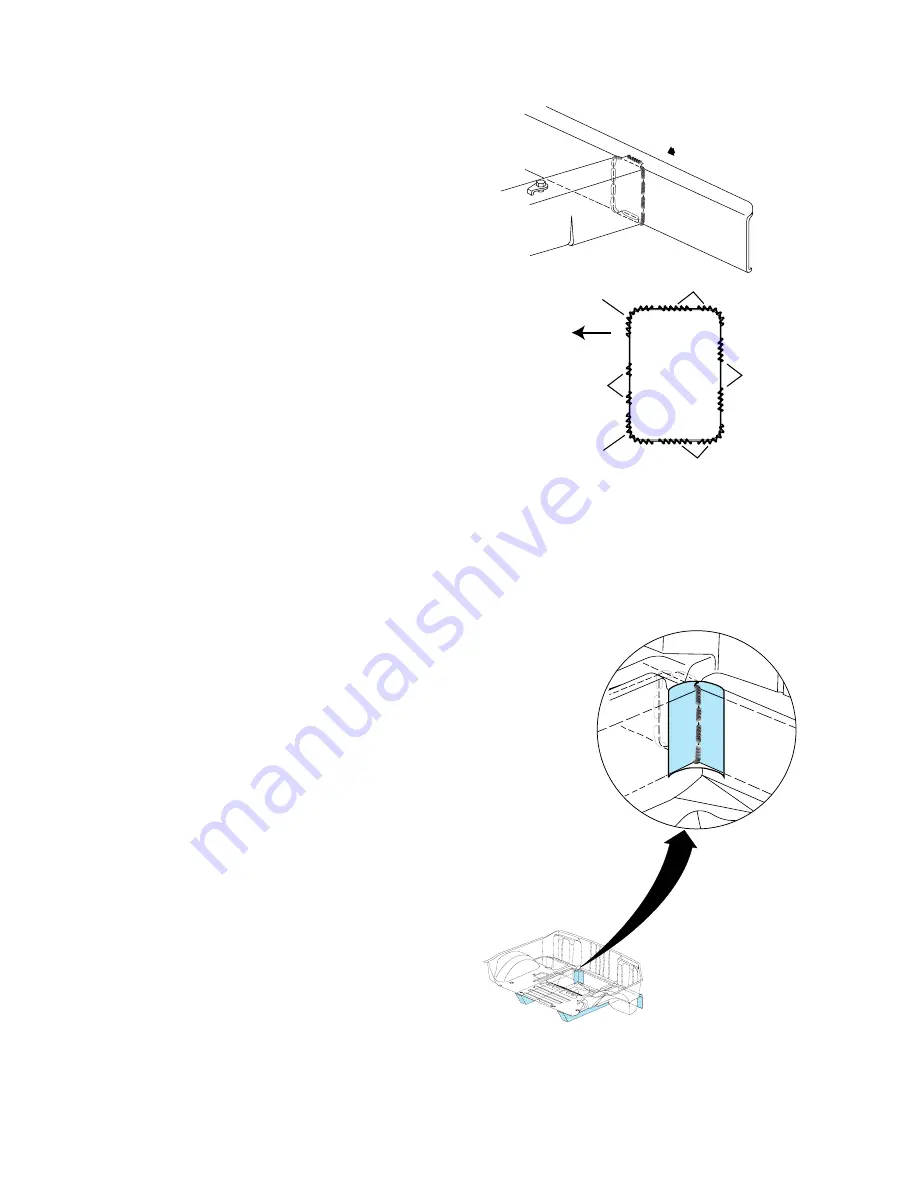
1997/98 Chevrolet Corvette
Collision Repair
3-35
Rear Bumper Impact Bar
,,
,
,
,
,,
,
,
View A
40mm
50mm
15mm
30mm
50mm
40mm
View A
C of
vehicle
L
Fig.␣ 3.74 — Weld Perimeter of Joint, as Indicated
,
,,
,
,
,
,
,
,
,
,
,
,
,
,
,
,
,
,
Fig.␣ 3.75 — Prime Bare Metal Areas
Before Installing Window Cutouts
2
Temporarily position the impact bar and
scribe lines into the primer indicating where
the welds will be made. Remove the primer
from the areas to be MIG welded by sanding
with 80-grit paper on a ‘Dual-Action’ sander
(DA). Do Not use a grinder to remove the
primer.
3
Prepare all bare metal surfaces and apply
weld-through primer as necessary. Be sure to
apply primer to the inside of the ‘fishmouth’
area also.
4
Position the bumper impact bar using
three-dimensional measuring equipment and
install per the original weld locations. Stitch
weld around the ‘fishmouth’ joint. If not trace
of the original welds are present, use
Fig.␣ 3.74 as a guide for welding the side rails
to the impact bar. This weld pattern will
create a solid weld joint with minimal heat
distortion.
5
Clean and prepare all welded surfaces,
use 3M’s Scotch-Brite Clean-N-Strip Discs
(disc P/N 07460, mandrel P/N 07491), or
equivalent (Fig.␣ 3.75).
Important: Prior to refinishing, refer to
GM P/N 4901 Refinish Manual for
recommended products.
6
Apply approved anti-corrosion primer.
Notice: DO NOT top-coat any bonding
surfaces.
Notice: Top surface of impact bar (where
it is to be bonded to the rear
compartment panel), must not be
top-coated, see Fig.␣ 3.73. The bonding
area must remain a ‘primer only’ surface
7
Apply 50mm (2 inch) wide tape over the
‘windows’ cut in the rear compartment panel,
from outside the vehicle. Apply adhesive to
the inside of the tape backer, and install the
previously cut-out pieces in their original
locations (Fig.␣ 3.76). (
Refer to SMC repair
procedures.)
Important: Use US Chemical and Plastics
82014B System 2000 Structural Adhesive,
a PLIOGRIP
®
adhesive manufactured by
Ashland Chemical Company, or equivalent.
Note the 9 minute working time and 1
hour cure time.