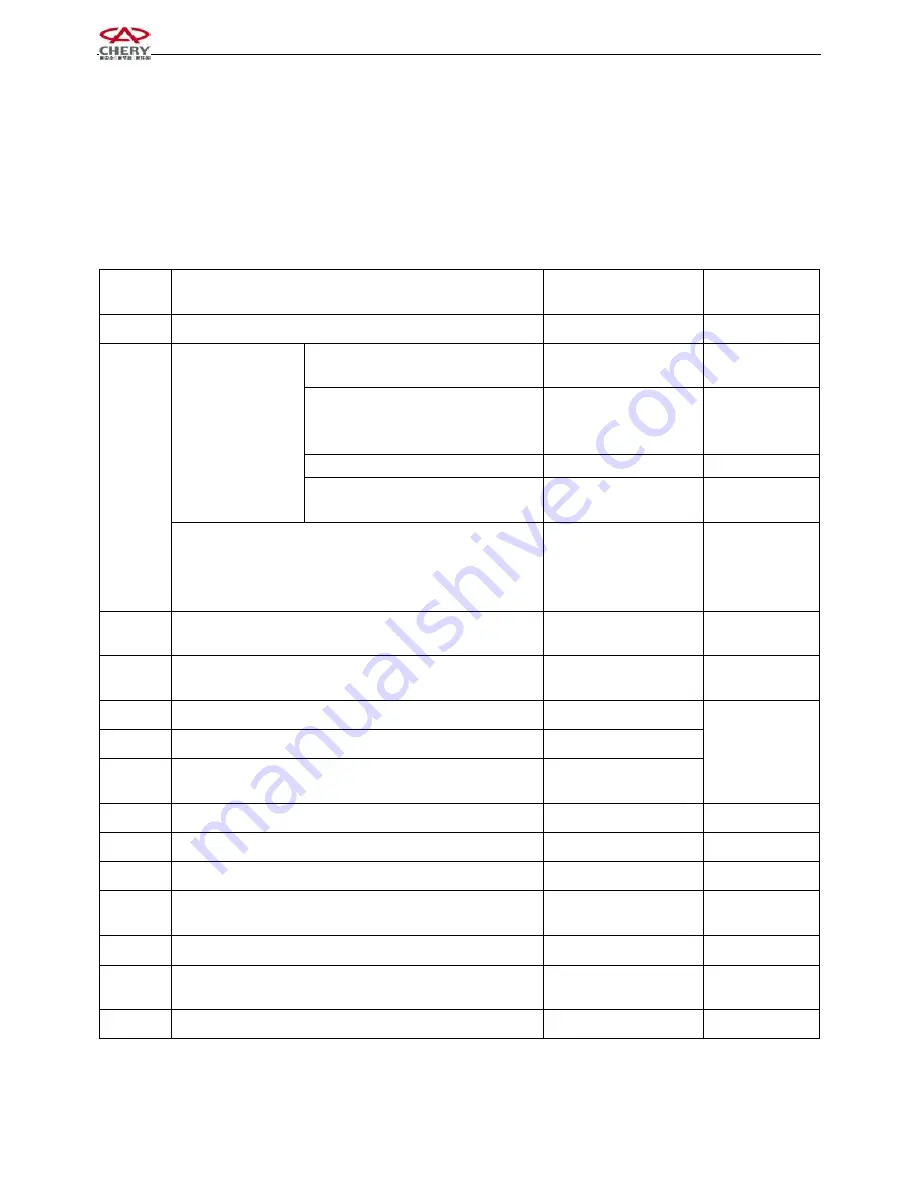
Chery QQ Service Manual
Mechanical Part of SQR 472Engine
52
Remarks: In the above tables, the capital letter and suffix following the sizes (For example, H
7
of
φ
28H
7
) mean the
process precision, which are unconcerned with the maintenance and may be ignored in the course of maintenance.
Chapter 4. Table
of
Measurement
Parameters
of
SQR472
EngineSQR472
No.
Measuring Items
Acceptance value
Remark
1
Axial clearance of crankshaft
0.089-0.211mm
Assemble the crankshaft and tighten the
main bearing cap bolt
≤
1 Nm
Mount the piston connecting rod
assembly and tighten the connecting
rod bolt
≤
5.5Nm
≤
6Nm
Torque of crankshaft
when rotating at
uniform speed
Installing timing belt and spark plug
≤
26 Nm
2
Mount the valve, spring and camshaft (excluding timing belt
and spark plug) on the cyllinder head, tighten the camshaft
bolt, and then measure the torque of the camshaft rotating at
uniform speed
≤
32 Nm
3
Distance between the outer edge of steel ball and the front end
of camshaft
5.65
±
0.5mm
4
Distance between the outer edge of steel ball and the rear end
of camshaft
8.65
±
0.5mm
5
Axial clearance of intake camshaft
0.10~0.179
6
Axial clearance of exhaust camshaft
0.10~0.253
7
Jumping amount of installation surface of flywheel wearing
piece
0.10mm
max
8
Protrusion height of crankshaft woodruff key
2
~
2.20mm
9
Intake valve clearance
0.18
±
0.05mm
10
Exhaust valve clearance
0.25
±
0.05mm
11
Tension of timing belt (When the middle part of the rigth side
is pressed down for 4-5mm
)
200
~
280N.m
12
Compression pressure of cylinder
10~14bar
13
Tension of generator belt
(
When the part between the
generator and water pump is pressed down for 4-5mm
)
98N.m
14
Refilling amount of engine oil (including filter)
3.5 Liter
Summary of Contents for QQ
Page 58: ......
Page 59: ......
Page 60: ...01 2 1 0 1 0...
Page 61: ...3 4 5 6 7 7 2 8 6 6 9 4 3...
Page 62: ...4 2 6 4 4 4 9 9 6 4 2 6 9 4 6 9 6 9 6 7 9 8 8 8 7 6 6...
Page 63: ...8 4 6 7 4 8 9 5 8 8 2 8 8 2 8 A A 8...
Page 65: ...7 7 5E 7 5 847 60141 7 6 9 D 7 6 9 7 6 4 8 8 F 3 3 3 3 3 8...
Page 68: ...7...
Page 69: ...D 4 00 0 02 012D 7 03 0145406 768 4694 2D 5 3 7 9 7 9 7 9 7 5 847 60141 7 D 8 5 5 461 8 3 7 5...
Page 70: ...7 1123 605492 0G 8 9...
Page 72: ...7 5 847 60141 7 D 3 6 8 9 6 7 1123 605492 9 04 0 9 M 9 9 7 7 9...
Page 73: ...4 D 8 9 0 4 1 8 9 7...
Page 74: ...D 4 0 0 02 012 7 7 8 7 6 7 A8 7 7 N 7 4 4 0I 4 0I 8 03 0145406D 8 7 1123 M 9 7 4 7...
Page 79: ...M 6 05492D...
Page 81: ...012 7 2 9 9 03 0145406 768 4694 2 7 8 7 7 5 847 60141 7 4 4 4 E 0I 2 4 461 8 7 A...
Page 82: ...012 9 6 6 4 03 0145406 4 3 4 6 4 1123 2H 4 23265 7 5 847 60141 4 D 05492 6 4 M 8...
Page 84: ...1 4 9 4 9 D P Q 7 9 A 9 3 9 7 2 9...
Page 85: ...8 A P Q 9 S 9 8 S A A 7 S A 7 2 2 A 7 8...
Page 86: ...1 A P Q 9 S 9 2 2 9 2 2 E A A A 8 2 42 2 O2 A 7 A 7 2 2 2 A 7...
Page 87: ...0 5 A 9 9 8 3 E A 9 5 8 3 A 9 A 7 0 8 3 A 7 5...
Page 88: ...8 8 8 A P Q 9 2 2 9 A 7 0 2 2 2 9 9 A 7 7 8 2 2 0 2 A 7 8...
Page 90: ...8 8 A P Q 9 9 2 2 A 7 2 2 2 A A 7 2 2 2 A 7 8...
Page 91: ...E A P Q 9 9 2 O2 2 42 A 7 2 2 2 A A 7 2 2 A 7...
Page 93: ...A 9 S 9 6 6 S 9 6 9 00 S A 7 2 2 0E A S A 2 9 A S A 7 7 2 A 7 A...
Page 94: ...A P Q 9 S 9 S 9 A S A 7 0 7 6 A 7 S A 9 9 S A 2 9 A...
Page 95: ...8 A 9 S 9 6 8 0 0 A S 9 8 A S A 9 7 1 0 6 S A 8...
Page 96: ...1 2 2 2 2 2 4 2 4 2 2 4 4 12 2 7 9 2 2 2 2 9 9 8 D 8 9 8...
Page 97: ...0 A S 9 4 A S 9 P Q 04 A S 9 A S 9 A S A 9 S 6 9 S 9 A...
Page 99: ...A S A 6 2 A S 9 7 7 7 7 A S A 9 S A 1 6 9 S 9 0 A S A 7...
Page 101: ......
Page 102: ...A S P Q 9 S 9 A S 9 8 S A S 9 0 0 1 S 6 6 6 9 S 9 6 A 6 S A S 9 1 0 S 9 0...
Page 103: ...S A 2 A 6 S A 6 A S A 6 A S 9 6 I A S 9 P Q D 1 0 S 9 A 7 I 8 6 S 9 S A 6 9 S A 7 1 A...
Page 104: ...A S P Q 9 S 9 E 7 0 2 A S 9 7 D 1 0 S 9 A S 9 8 4 4 S 9 S 9 6 I A S 9 2 0 S 1 6 6 6 9 0 6 S 9...
Page 105: ...A 6 S S 9 0 S 9 S A 2 A 6 S A 6 A S A 6 2 A S 9 S A 9 S A 1 6 A 7...
Page 107: ...0 A 6 S S 9 0 S 9 S A 2 A 6 S A 6 A S A 6 2 A S 6 9 S 9 1 A 8 9 9 S 0 9 S 9...
Page 108: ...S P Q 9 S 9 A S 9 A S 9 7 7 S 9 6 A S 9 A...
Page 110: ...2 A 6 S A 6 A S A 6 2 A S A 9 S 9 S 9 M A S A 9 S A 7 1 A...
Page 111: ...S P Q 9 S 9 7 7 0 8 2 S 9 A S 9 P Q 7 1 0 2 S A 6 9 S A 7 A...
Page 113: ...9 S A 7 A S P Q 9 S 8 6 9 S A 9 S 9 A S A 9 S A A 9 S A 9 S A 6 9 S A 1 A 9 S 9 0 6 A S A 7 A...
Page 117: ...0 S A A 6 S A 6 A S A 6 A S 9 A S 9 8 6 S A 7...
Page 118: ...S 9 4 UV 4 S A 4 A 9 S 9 7 7 0 8 2 WX A 9 S A 7 2 A 7...
Page 119: ...2 A 4 4 0 2 A 4 4 6 4 2 8 4 4 2 4 D 8 4 A S 4 6 8 8 6 6 2 M 9 2...
Page 120: ...00 6732 695406 00 6732D 695406D 00 6732D 695406D 6...
Page 121: ...00 6732D 695406D A C 00 6732D 6 695406D 6 00 6732D 695406D 00 6732D 695406...
Page 122: ......
Page 123: ...0 1 2 3 2 2 4 5...
Page 124: ...6 1 7 8 9 9 6...
Page 125: ...2 5 1...
Page 375: ...Chery QQ Service Manual BCM Computer Control System 3 Audio circuit diagram 96...
Page 405: ...Chery QQ Service Manual BCM Computer Control System 126 Fuse and relay of the engine chamber...
Page 406: ...Chery QQ Service Manual Inspection and Repair of BCM Computer Control System 127...
Page 413: ...Chery QQ Service Manual Chery Automobile Co Ltd 129...
Page 511: ...Chery QQ Service Manual 283 Chery Automobile Co Ltd...
Page 515: ...Chery QQ Service Manual 287 PDF created with pdfFactory Pro trial version www pdffactory com...
Page 516: ...Chery QQ Service Manual 288 PDF created with pdfFactory Pro trial version www pdffactory com...
Page 518: ...308 Chery Automobile Co Ltd Chery QQ Service Manual...
Page 538: ...Chery QQ Service Manual Body System 2 5 2 2 Front view figure 27 Chery Automobile Co Ltd...
Page 544: ...Chery QQ Service Manual Body System 2 5 2 3 Rear view figure 33 Chery Automobile Co Ltd...
Page 551: ...Chery QQ Service Manual Body System 2 5 2 6 Crossbeam size 40 Chery Automobile Co Ltd...
Page 555: ...PDF created with pdfFactory Pro trial version www pdffactory com...
Page 557: ...PDF created with pdfFactory Pro trial version www pdffactory com...
Page 600: ...S11 Brake System...
Page 617: ...5 Rear end Leakage In contact Primary piston Secondary piston Rear end leakage...
Page 619: ...Proportioning valve Proportioning Valve...
Page 622: ...LF wheel Proportioning Valve RR wheel RF wheel RF wheel...
Page 627: ...2 When the Braking Pressure is High In contact Piston...
Page 630: ...Front wheel Brake...
Page 631: ...Rear wheel Brake...
Page 632: ...0 1 2 0 3...
Page 633: ...2 4...
Page 634: ...0 00 0 0 1 2 1 3 4 0 5 4 4 1 0 4 4 0 4 0 3 0 4 6 0 1 5 4 0 0 0 4 7 3 4 8 2 7 4 6 6...
Page 635: ...0 4 4 0 3 0 3 9 0 3 4 6 0 5 0 6 0 0 3 3 0 3 0 0...