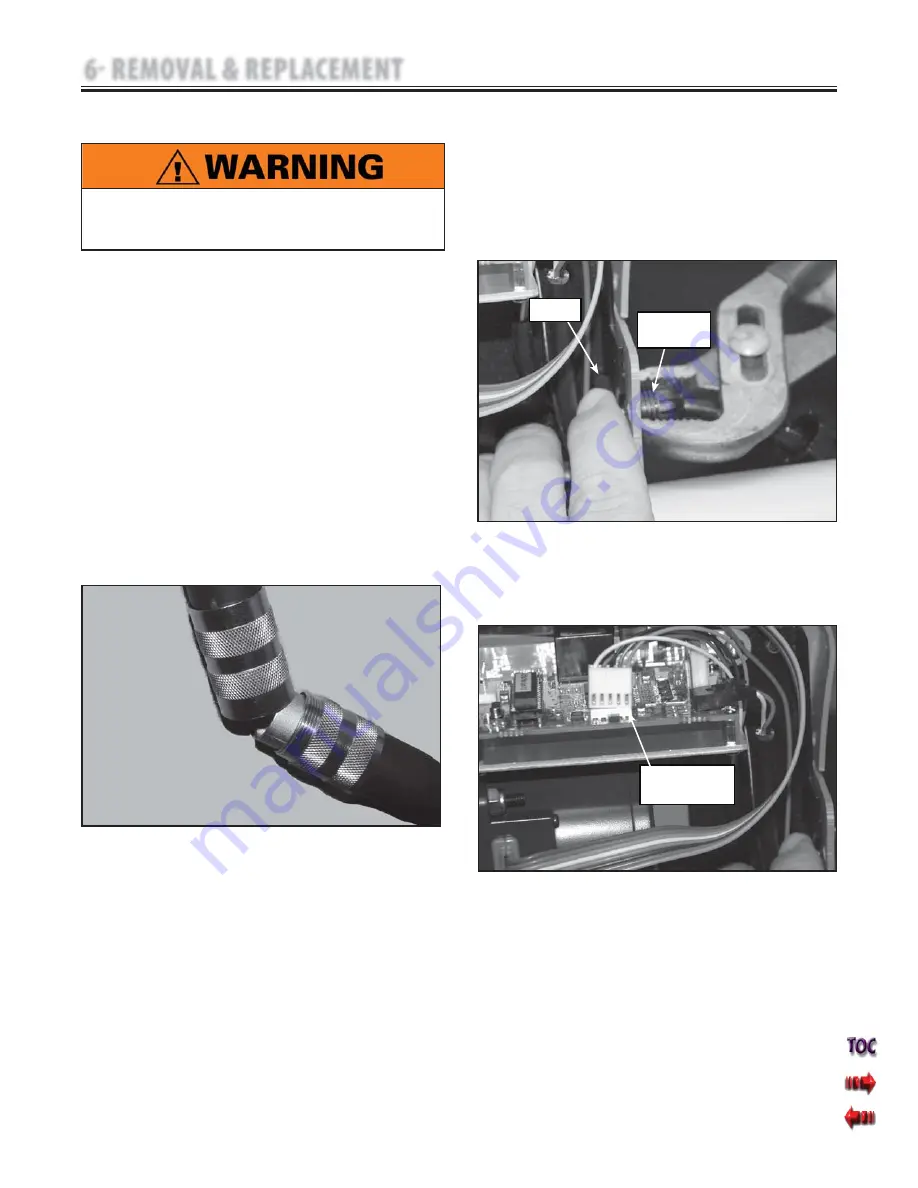
26
OptiFlex® 3 Continuous Passive Motion (CPM) Therapy Unit
A. Part Number
. . . . . . . . . . . . . . . . . . . . . . . . . . .89852
B. Tools and Equipment Required
Adjustable Pliers
NOTE:
Refer to
Section B
of the section referenced
below for additional tools needed.
C. Pendant Receptacle Cable Removal &
Replacement
1. Refer to
Section 6.1, part C
, Rear Cover
Removal and Replacement to remove the
Rear Cover of the unit.
2. Disconnect the Pendant Cable from the
Pendant Cable Receptacle by turning the
Pendant Cable connector counterclockwise.
Continue to unscrew to release.
Refer to
Figure
6.18.
•
FIGURE 6.18
Disconnect the pendant from the unit before
attempting any removal or replacement procedures
to prevent electrical shock.
3. Hold the nut inside of the unit Frame
securing the Receptacle Cable. Using a pair of
adjustable pliers, turn the housing on
the outside of the unit counterclockwise to
release. Continue to unscrew and remove the
Receptacle
Cable.
Refer to Figure 6.19.
NUT
CABLE
HOUSING
4. Disconnect the 5 pin connector from the
Control
Board.
Refer to Figure 6.20.
FIGURE 6.19
5. Replace in reverse order.
FIGURE 6.20
5 PIN
CONNECTOR
6 REMOVAL & REPLACEMENT
6.9 PENDANT RECEPTACLE CABLE