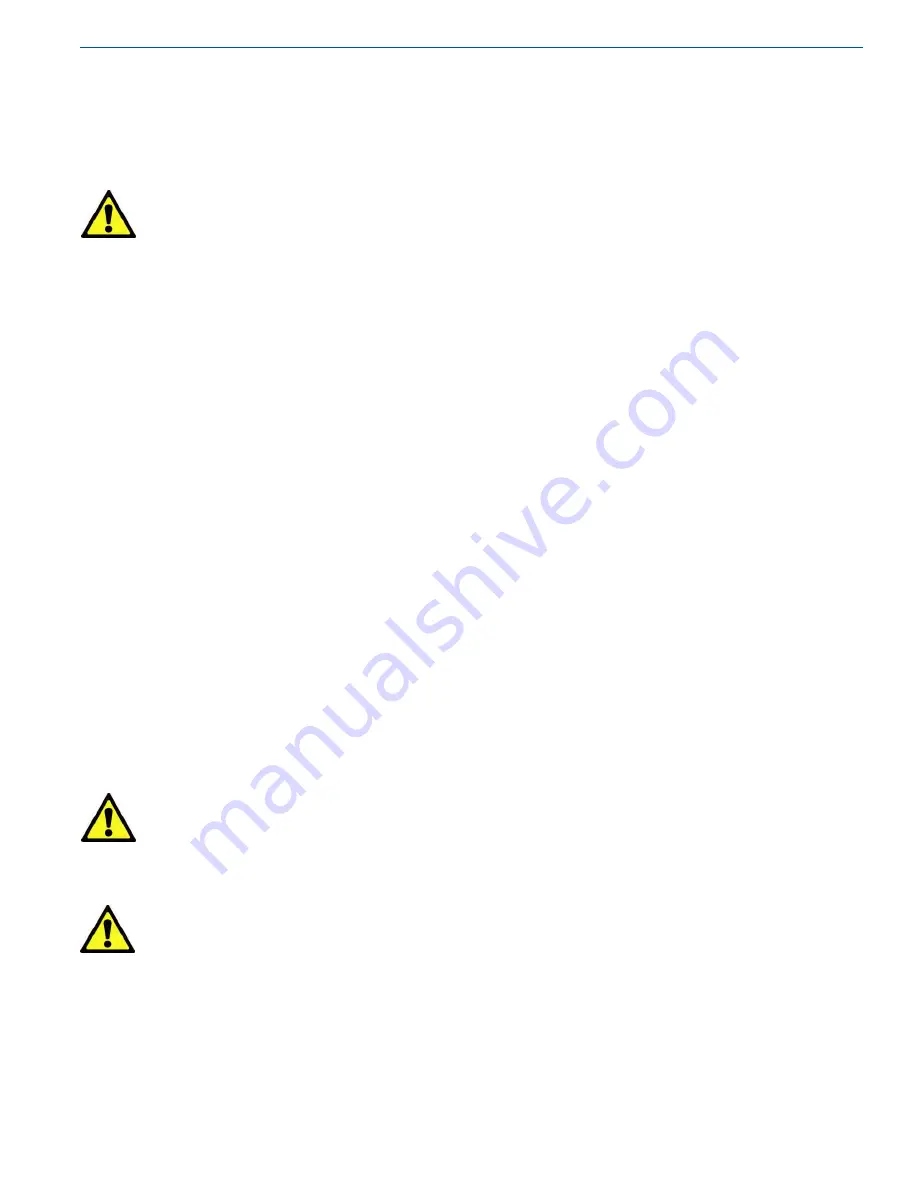
21
Operations
Product Manual - Liquid Cylinders
7
When the transfer is complete close the receiving
equipment’s valve. Close the liquid valve on the
cylinder and relieve pressure from the hose.
8
Disconnect or remove the hose from the receiving
equipment.
Caution! The liquid and vent valves on
liquid cylinders should always be
kept closed to protect the inner
vessel and plumbing from being
contaminated.
Gas Withdrawal
The high pressure liquid cylinder will deliver gas at various
flow rates and temperatures for different applications.
The flow rate is controlled by the equipment that is being
supplied gas by the liquid cylinder. The continuous flow rate
indicates the flow rate that will normally provide gas at a
reasonable temperature and should not be exceeded. Higher
flow rates may provide very cold gas that could damage the
equipment attached to them.
To supply gaseous product follow this step-by-step
procedure:
1
Connect the proper regulator to the liquid cylinder’s gas
use outlet
2
Connect the proper hose between the liquid cylinder gas
use regulator and the receiving equipment.
3
Open the pressure building valve.
4
Allow pressure to build to the operating pressure.
5
Open the gas use valve.
6
Adjust the gas use regulator for the proper delivery
pressure.
7
When the gas delivery is completed, close all liquid
cylinder valves
Caution! The liquid and vent valves on
an empty liquid cylinder should
always be kept closed to protect
the inner vessel and plumbing
from being contaminated.
Caution! In the Dura-Cyl HP/Cryo-Cyl HP
liquid cylinders the pressure
must be kept above 70 psig for
CO
2
to prevent solidifying the
CO
2
.
Service and Maintenance
Refer to the Maintenance section of this manual to
troubleshoot problems and service these liquid cylinders.
Dura-Cyl
®
LCCM HP Liquid Cylinders
The Dura-Cyl LCCM HP liquid cylinder models are
functionally the same and only vary in capacity. They are
designed to transport, store and deliver liquid oxygen,
nitrogen, argon, carbon dioxide, or nitrous oxide as a
cryogenic liquid or gas. They can be used to transport
liquid carbon dioxide or nitrous oxide in Canada with the
exemption Chart has received from Transport Canada. The
common application for these high pressure liquid cylinders
is to provide gas at pressures up to 350 psi (24.1 bar) or
deliver liquid CO
2
. The high pressure liquid cylinder will
build and maintain pressure with a pressure control manifold.
The pressure building portion of the regulator has a setting of
300 psi (20.7 bar). If the pressure exceeds 325 psi (22.4 bar)
the economizer portion of the regulator will supply gas from
the tank vapor space to the receiving equipment which will
reduce the cylinder pressure. A continuous gas flow can be
automatically provided from these cylinders.
Filling Procedures
The high pressure liquid cylinder is regulated by the DOT/
Transport Canada for transporting liquid oxygen, nitrogen,
argon, carbon dioxide, or nitrous oxide. The filling of these
high pressure liquid cylinders must be done by product
weight. This will allow enough gas space above the liquid
to keep the cylinder from becoming liquid full if its pressure
rises to the relief valve settings The standard relief valve
setting is 350 psig (24.1 bar). The filling procedure will
explain the proper way to use the filling weight table.
The high pressure liquid cylinder is equipped with liquid and
vent valves that are used during the filling procedure. The
liquid valve is equipped with a dip tube that extends into the
inner vessel of the cylinder and reaches to the bottom The
vent valve has a dip tube attached to it that also extends into
the inner vessel of the cylinder This vent tube is designed to
spray the liquid into the top of the vessel so that pump filling
through the vent valve will keep head pressure down in the
cylinder
Filling can be accomplished by either pressure transfer
or pump fill. The following procedure should be used for
pressure transfer fillings.
1
Sample the residual gas that is in the cylinder. Purge the
cylinder if necessary to ensure the proper purity.
2
Place the cylinder on the filling scale. Record the
weight. Compare this weight to the registered tare
weight on the data plate. The difference is the weight of
the residual gas
3
Connect the transfer hose to the fill valve. Record the
new weight The difference between this weight and the
initial weight is the weight of the transfer hose
4
To determine the total filling weight add the tare weight
of the cylinder, the hose weight and the proper filling
weight from the filling table (i.e. Dura-Cyl 160 HP
Summary of Contents for Cryo-Cyl80HP
Page 2: ......
Page 6: ......
Page 12: ......
Page 32: ......
Page 50: ...44 Specifications Product Manual Liquid Cylinders MCR Plumbing Configuration...
Page 52: ...46 Specifications Product Manual Liquid Cylinders LCCM Plumbing Configuration...
Page 54: ......
Page 56: ......
Page 57: ...51 Product Manual Liquid Cylinders Appendix 1 Troubleshooting Guides Cutaway Explanation...
Page 62: ...56 Appendix 1 Product Manual Liquid Cylinders Troubleshooting Flow Chart 3...