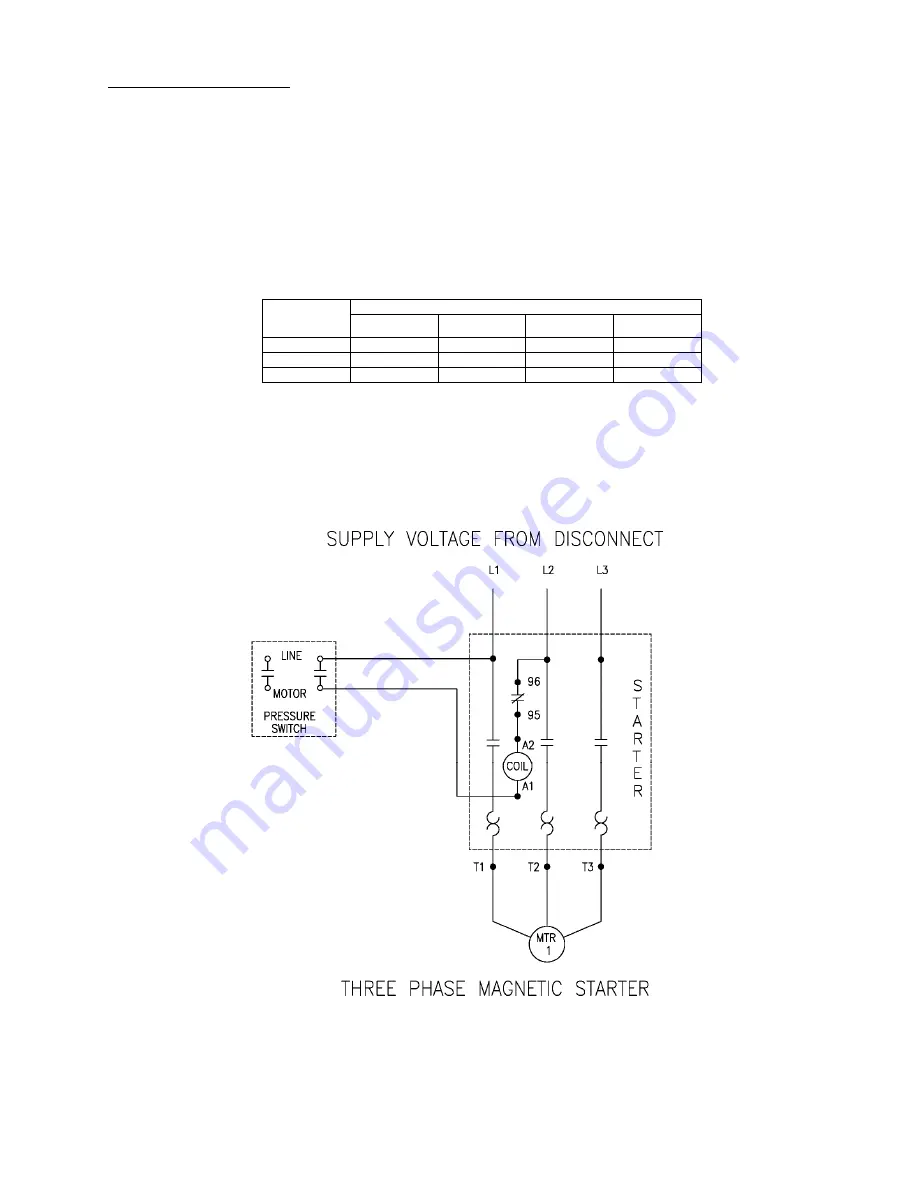
9
INSTALLATION (CONT’D)
ELECTRICAL POWER SUPPLY
It is essential that the power supply and the supply wiring are adequately sized and that the voltage
correspond to the unit specifications. Branch circuit protection must be provided at installation a
specified in the National Electrical Code.
All wiring should be performed by a licensed electrician or electrical contractor. Wiring must meet
applicable codes for area of installation. The table gives recommended wire sizes based on the
1999
NEC.
WIRE SIZE (AWG) – 75°C COPPER – 30°C AMBIENT
3 PHASE
MOTOR
HP
200/208V
230V
460V
575V
20 3
(0)
4 (1)
8 (6)
10 (6)
25 1
(000)
2 (00)
6 (4)
8 (6)
30 0
(0000)
1 (000)
6 (3)
8 (4)
Values in ( ) for Duplex Unit w/one incoming power line to both motors.
All models require a properly sized magnetic starter as specified in the National Electric Code (NEC).
See Figure 1-1 for simplex wiring diagram and Figure 1-2 for duplex wiring diagram.
If ordered with a factory mounted magnetic starter, compressor is wired at factory. It is necessary only to
bring lines from a properly sized disconnect switch to the magnetic starter mounted on the unit.
Figure 1-1 Simplex Wiring Diagram
304CAS546-A
(Ref. Drawing)