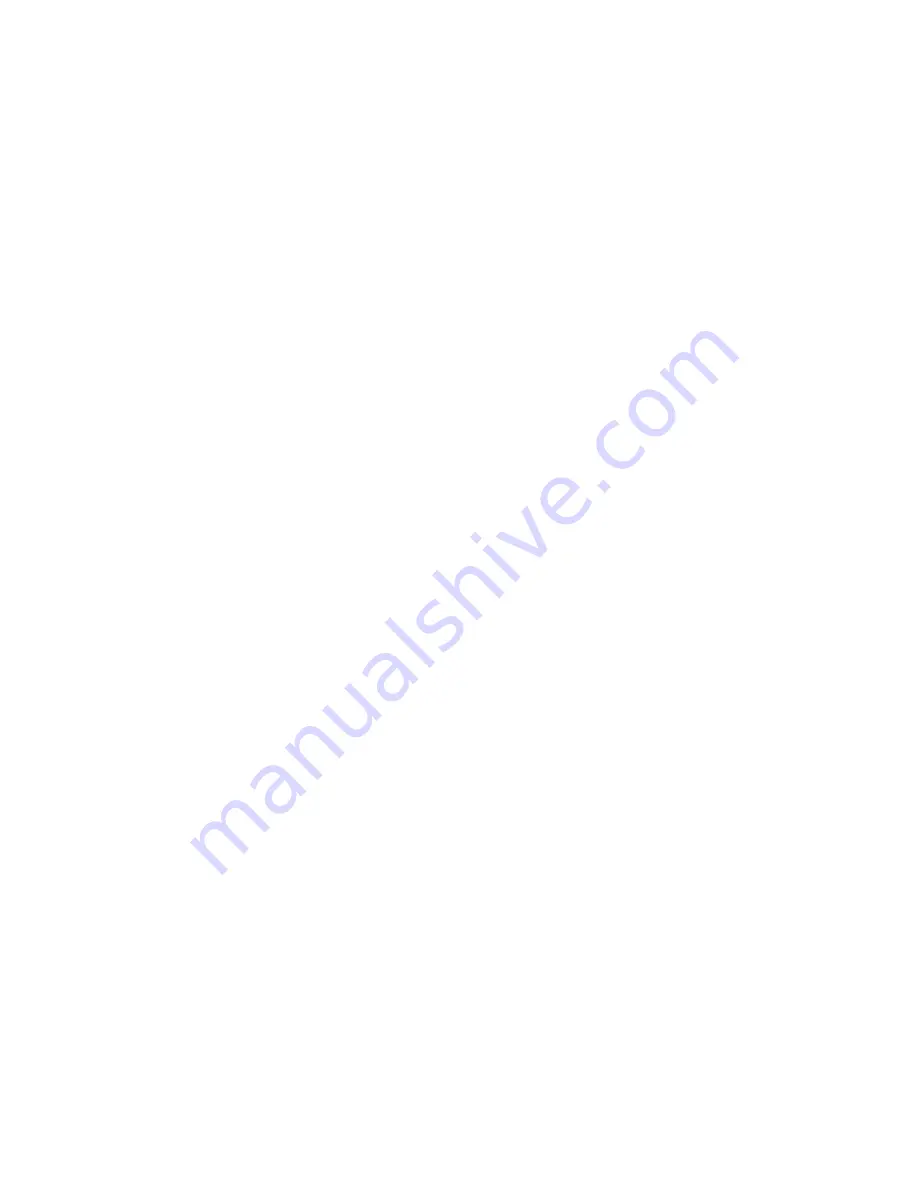
5
SAFETY AND OPERATION PRECAUTIONS
___________________________________________________________________________________
Because an air compressor is a piece of machinery with moving and rotating parts, the same precautions
should be observed as with any piece of machinery of this type where carelessness in operation or
maintenance is hazardous to personnel. In addition to the many obvious safety rules that should be
followed with this type of machinery, the additional safety precautions as listed below must be observed:
1.
Read all instructions completely before operating air compressor or unit.
2.
For installation, follow all local electrical and safety codes, as well as the National Electrical Code
(NEC) and the Occupational Safety and Health Act (OSHA).
3.
Electric motors must be securely and adequately grounded. This can be accomplished by wiring
with a grounded, metal-clad raceway system to the starter; by using a separate ground wire
connected to the bare metal of the motor frame; or other suitable means.
4.
Protect the power cable from coming in contact with sharp objects. Do not kink power cable and
never allow the cable to come in contact with oil, grease, hot surfaces, or chemicals.
5.
Make certain that the power source conforms to the requirements of your equipment.
6.
Pull main electrical disconnect switch and disconnect any separate control lines, if used, before
attempting to work or perform maintenance on the air compressor or unit. "Tag Out" or "Lock Out"
all power sources.
7.
Do not attempt to remove any compressor parts without first relieving the entire system of
pressure.
8.
Do not attempt to service any part while machine is in an operational mode.
9.
Do not operate the compressor at pressures in excess of its rating.
10.
Do not operate compressor at speeds in excess of its rating.
11.
Periodically check all safety devices for proper operation. Do not change pressure setting or
restrict operation in any way.
12.
Be sure no tools or rags or loose parts are left on the compressor or drive parts.
13.
Do not use flammable solvents for cleaning the air inlet filter or element and other parts.
14.
Exercise cleanliness during maintenance and when making repairs. Keep dirt away from parts by
covering parts and exposed openings with clean cloth or Kraft paper.
15.
Do not operate the compressor without guards, shields and screens in place.
16.
Do not install a shut-off valve in the discharge line, unless a pressure relief valve, of proper design
and size, is installed in the line between the compressor unit and shut-off valve.
17.
Do not operate compressor in areas where there is a possibility of ingesting flammable or toxic
fumes.
18.
Be careful when touching the exterior of a recently run motor - it may be hot enough to be painful
or cause injury. With modern motors this condition is normal if operated at rated load - modern
motors are built to operate at higher temperatures.
19.
Inspect unit daily to observe and correct any unsafe operating conditions found.
20.
Do not "play around" with compressed air, nor direct air stream at body, because this can cause
injuries.
21.
Compressed air from this machine absolutely must not be used for food processing or breathing
air without adequate downstream filters, purifiers and controls.
22.
Always use an air pressure regulating device at the point of use, and do not use air pressure
greater than marked maximum pressure of attachment.
23.
Check hoses for weak or worn condition before each use and make certain that all connections
are secure.
24.
Always wear safety glasses when using a compressed air blowgun.
The user of any air compressor package manufactured by Champion is hereby warned that failure to
follow the preceding Safety and Operation Precautions can result in injuries or equipment damage.
However, Champion does not state as fact or does not mean to imply that the preceding list of Safety and
Operating Precautions is all inclusive, and further that the observance of this list will prevent all injuries or
equipment damage.
Summary of Contents for CCE10
Page 28: ...28 UNIT HAZARD DECALS ...
Page 29: ...29 PUMP HAZARD DECALS F ...