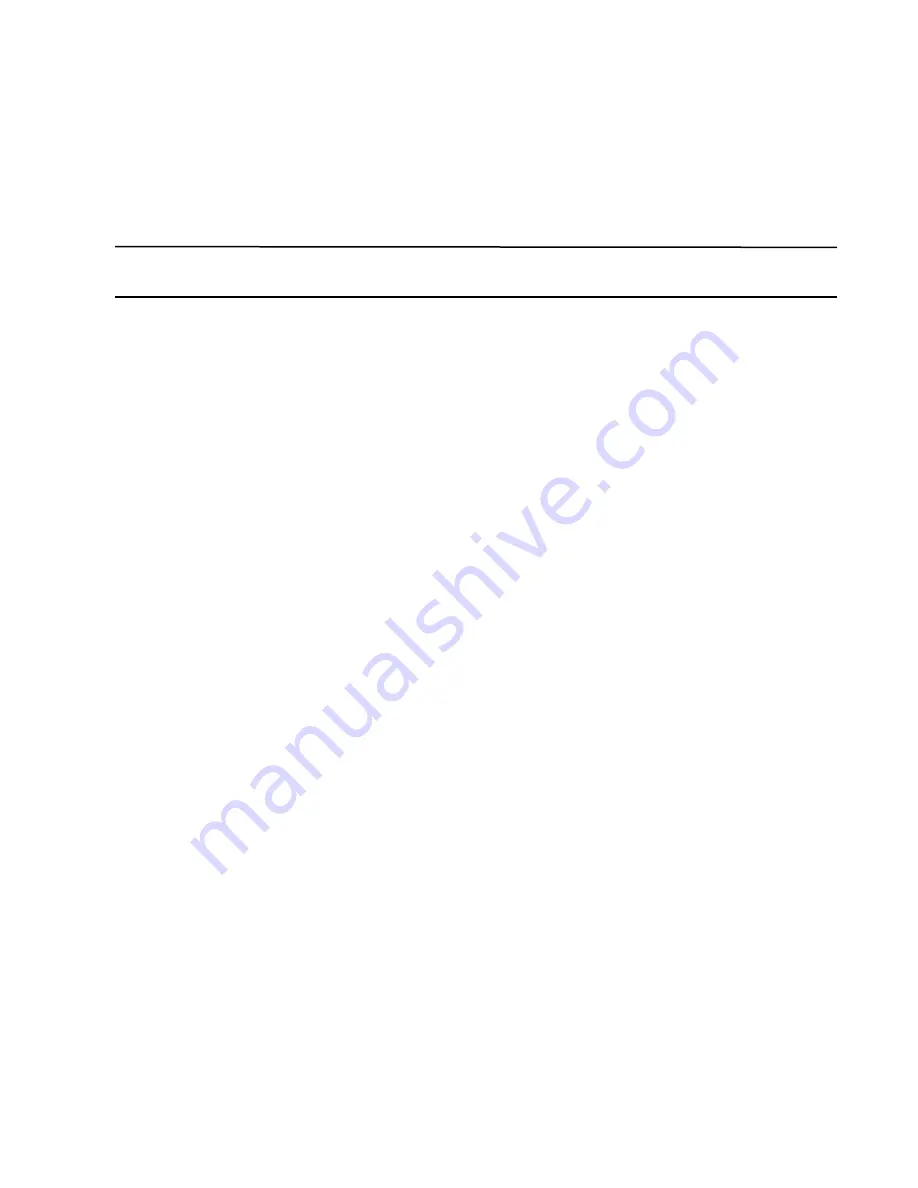
i
Revision History
Revision History
Specifications are subject to change based on continual product improvement. Dishwasher
owners may a request a manual by calling 1(800) 858-4477 in the USA and 1(800) 263-5798 in
Canada.
Revision
Revised
Serial Number
Description
Date
Pages Effectivity
3.5.21
All
RP20102891
Released First Edition
3.29.21
15
All
Revised the HRU venting instructions.
5.21.21
5
All
Added warning to HP mounting instructions.
http://champdw.us/PRO