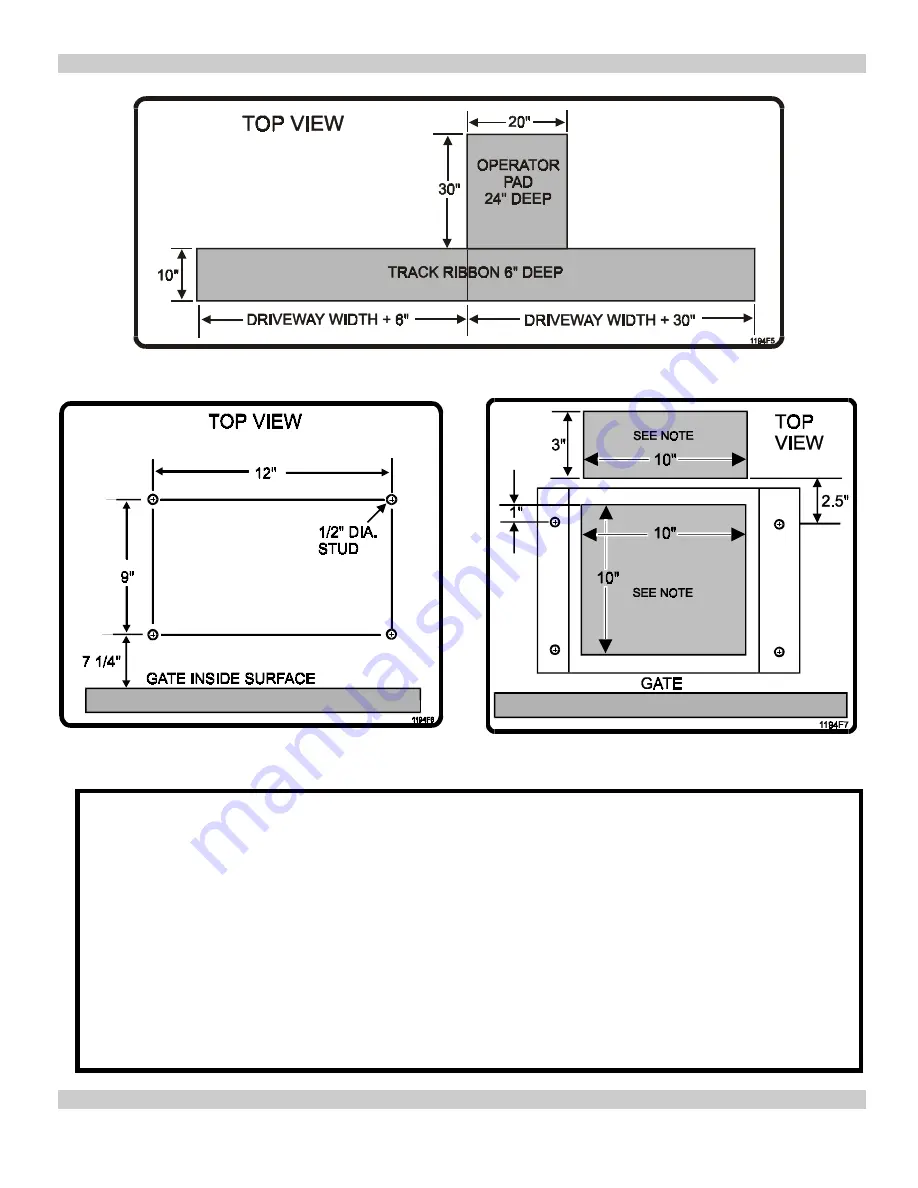
Rev C
Doc
6001194
(01-20259)
4 of 36
B. PAD AND MOUNT
Figure 4. Pad And Track Ribbon.
Figure 5. Bolt Down Pattern.
Figure 6. Conduit Entrance Areas.
1. The concrete pad must be sufficient to support the gate operator and the forces created by the
moving gate. LiftMaster recommends a pad 20” wide by 30” long by 24” deep (Figure 4).
2. The operator must be level and parallel to the gate, so the pad should be level and about 4” above
ground level to prevent water entrance.
3. Four anchor bolts are required to secure the gate operator to the pad. The mounting holes in the
gate operator are 5/8” in diameter. ½” x 3½ “ Red Head bolts are recommended (Figure 5).
4. Be sure to provide access for wiring conduits (Figure 6).
NOTE:
Shading indicates acceptable areas for conduit stub access.
5. Track installation should be on concrete, not asphalt, and should be at least 10’’ wide and 6” deep.
6. A 6” gate overlap at the open end of the gate when closed should be provided.
7.
A 30” gate overlap at closed end of the gate when closed should be provided.