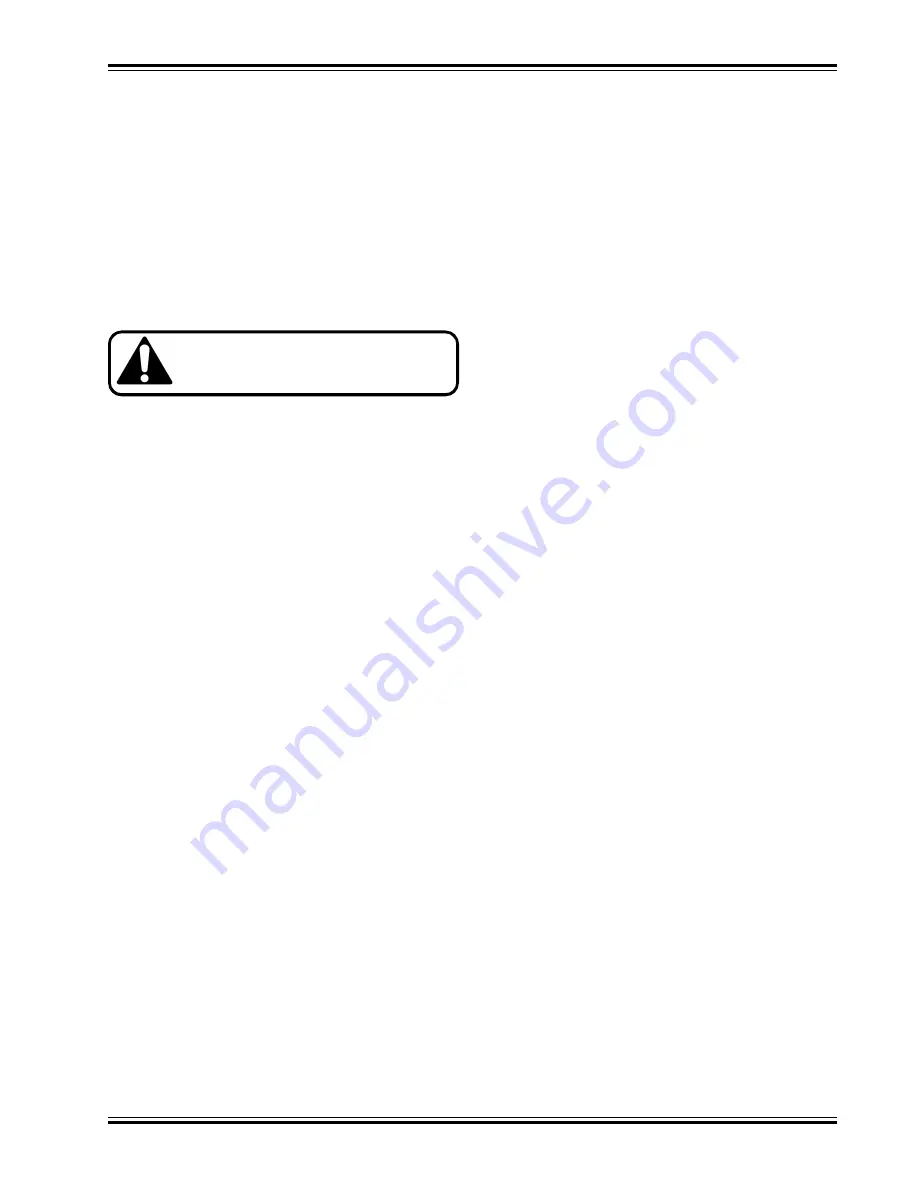
2-1
F.352-KO/EH-3C DRILL/AUG 03
2.0 OPERATION
2.0 OPERATION
2.1 STARTING THE MACHINE
The power for this machine is supplied by two motors;
one is for the hydraulic power pack, the other is for the
spindle. They are both started and stopped simulta-
neously by a single set of start-stop buttons located on
the stand under the table (fig. 1-1). Be sure both mo-
tors are operating before trying to drill paper.
2.2 OPERATING THE DRILL
Pressing down on the foot switch activates the hydraulic
unit which brings the drill heads (and drills) down to
the table. When the drills reach the bottom of their
stroke, they will automatically return the “up” position.
(Note: The vertical stroke of the drills must be set be-
fore drilling to provide the proper drill depth. See sec-
tion 2.3 for adjustment procedures). The pedal must
be released and depressed again before drilling the
next set of holes, assuring full control and allowing no
repeat stroke. By releasing the pedal, the operator
can stop the drills in their downward stroke at any time
allowing them to return to their normal position, thus
preventing costly errors.
NEVER REST YOUR FOOT
ON THE TREADLE WITHOUT INTENDING TO
BRING DOWN THE DRILLS!
2.3 ADJUSTING THE VERTICAL STROKE
The vertical stroke of the machine determines the exact
depth the drills will reach at the bottom of their stroke.
Whenever installing a new set of drills, the vertical stroke
must be adjusted before drilling.
The two outside heads are provided with independent
height adjustment while the center head works from the
center overall adjusting screw. This is necessary be-
cause of the variance in length of the drills. Start by
adjusting the center head to its highest point. This is
accomplished by turning the drill depth adjustment
screw (fig. 1-1) counterclockwise until it stops turning.
Then adjust the side heads all the way up by turning
the knurled ring on the heads clockwise (use the pro-
vided drill drift in the holes if necessary). Now, with
the new drills in the place, put two or three sheets of
paper under the heads. The center spindle should then
be adjusted so that the center drill just cuts through
the paper. Too deep will cause a ragged hole in the
bottom sheets as well as a shorter drill life from drilling
into the cutting block. After the center drill is adjusted,
each outside spindle can be adjusted. Turn counter-
clockwise to lower and clockwise to raise. No locking
is necessary. Once all three drills are set, drill through
a full lift of paper. A final adjustment of the drill depth
adjusting screw may be necessary to obtain the best
results.
2.4 SETTING THE DISTANCE BETWEEN
DRILL HEADS
This machine incorporates three drilling heads operat-
ing on three belt-driven spindles. The center head is
stationary while the two outside heads have a lateral
adjustment of 1
3
/
4
” each.
This provides an adjustment range of 2
3
/
4
” to 4
1
/
2
” (7
cm to 11 cm) between the center drill and either of the
outside drills, or a range of 5
1
/
2
” to 9” (14 cm to 23 cm)
between the two outside drills.
The lateral adjustment is accomplished by loosening
the clamp knob (a black, plastic hand knob) located at
the rear of each outside head, and then turning the 4-
lobed, black knob located at the outside of each head.
This moves the heads along a shaft. A scale and pointer
located at the front of the heads gives a reading in
inches and millimeters of the center line relationship to
the center head. When a setting is made, make cer-
tain that the clamp knob is tightened again.
Any combination of three heads can be used, that is
one, two, or three holes may be drilled if desired. It is
recommended, however that no more than two half inch
hollow drills be used at the same time.
2.5 SETTING THE BACKGAUGE
POSITION
The backgauge position is adjusted by first loosening
the two thumb screws under the table. This will allow
the backgauge to move freely. Then use the two scales
on the top of the table to set the backgauge to the de-
sired position. The scales read in inches and millime-
ters and will give the distance from the edge of the
sheet to the center of the holes. Be sure the 1” (2.5
cm) square pieces mounted to the backgauge are
aligned on top of the scales to provide the proper read-
ing (fig. 1-1). Tighten the thumbscrews when finished.
CAUTION: Always wear safety glasses
when operating this machine.